Get the Most Out of Toolbox Talks: Workplace Safety and Communication
11
April,
2024
3 MINUTE READ

What Are Toolbox Talks?
Toolbox Talks, short safety meetings typically held at the job site before the commencement of a workday, are instrumental in reinforcing safety protocols and fostering a culture of awareness among workers. Making these gatherings more effective involves engaging participants, fostering active participation, and ensuring that the key safety messages resonate. Here are some tips to enhance the effectiveness of Toolbox Talks:
- Relevance is Key: Tailoring each Talk to the specific tasks and hazards workers face fosters engagement and understanding. Connect safety topics to recent incidents, near misses, or industry news to make them more relatable.
- Encourage Discussion: Fostering interactive discussions encourages participation and understanding. Encourage open discussions rather than a one-sided presentation. Invite questions and experiences from the participants and incorporate real-life examples or anecdotes to illustrate safety points.
- Keep a Schedule: Establish a consistent schedule for Toolbox Talks, ensuring they are held regularly (e.g., weekly or at the beginning of each shift). Consistency helps build a routine and emphasizes the ongoing commitment to safety.
- Do More Than Talk: Utilizing visual aids complements verbal communication, enhancing comprehension and retention. Hands-on demonstrations further reinforce proper techniques, making safety practices more memorable.
- Mix it Up: Rotate through a variety of safety topics to keep the content fresh and prevent disengagement. Cover both general safety topics and those specifically relevant to the current work environment.
- Involve Different Speakers: Rotate speakers to bring different perspectives and voices into the Toolbox Talks. Encourage supervisors, experienced workers, or safety professionals to lead discussions.
- Set and Measure Goals: Set achievable safety goals and challenges related to the Toolbox Talk topics. Establish a feedback mechanism to assess the effectiveness of Toolbox Talks. Celebrate achievements and recognize individuals or teams for their commitment to safety. Encourage workers to provide input on topics they find beneficial or suggest areas that need more attention.
- Document and Follow-Up: Maintain records of Toolbox Talks, including topics covered, attendance, and any actions or commitments made. Reinforce messages with regular follow-up discussions, safety audits, or assessments. Documentation ensures accountability and provides a reference for discussion of how the safety practices covered in the talks are being implemented and identify areas for improvement.
Regular Toolbox Talks are an invaluable tool in promoting a culture of safety, ensuring that every worker is equipped with the knowledge and awareness needed to carry out their tasks in a secure and health-conscious manner. By implementing these tips, Toolbox Talks can become more than just routine safety meetings—they can be dynamic, engaging sessions that actively contribute to a culture of safety within the workplace.
Here are some Toolbox Talk topics to enhance workplace safety:
Personal Protective Equipment (PPE) Emphasis: Remind workers about the importance of consistently wearing and maintaining their PPE. Discuss specific PPE requirements for the day's tasks, ensuring everyone is equipped appropriately.
Housekeeping Matters: Stress the significance of maintaining a clean and organized work area to prevent accidents and injuries. Encourage workers to promptly report and address any spills, debris, or potential hazards.
Equipment Inspection: Emphasize the importance of pre-task equipment inspections to identify and address any defects or malfunctions. Encourage a proactive approach by reporting equipment issues promptly for timely resolution.
Communication Protocols: Reinforce effective communication practices, including the use of hand signals and clear verbal communication. Discuss the importance of regular check-ins and updates, especially when working in teams or alongside heavy machinery.
Emergency Response Planning: Review emergency response procedures, ensuring everyone knows the location of emergency exits, first aid kits, and fire extinguishers. Conduct periodic drills to reinforce the proper response to various emergency scenarios.
Workplace Ergonomics: Discuss proper ergonomics to minimize the risk of musculoskeletal injuries. Highlight the importance of using ergonomic tools, maintaining good posture, and taking breaks as needed.
Weather Awareness: Address the impact of adverse weather conditions on safety. Provide guidelines on working safely during inclement weather and the importance of staying informed about weather forecasts.
Fall Prevention: Emphasize the use of fall protection equipment when working at heights. Discuss the potential hazards associated with elevated workspaces and the necessity of proper fall prevention measures.
Tool Safety: Remind workers to use tools for their intended purpose and inspect them for any damage before use. Discuss proper tool storage practices to prevent accidents and ensure tools are in good working condition.
Mental Health Awareness: Acknowledge the importance of mental health in overall well-being. Encourage an open dialogue about stressors and provide resources for mental health support if available.
DuraLabel Resources
Creating a positive safety culture is beneficial to not only the mental well-being of workers, but also their physical well-being too. Through positive reinforcement, employees tend to be happier, more productive, and more efficient in the workplace. Need help setting up a system in your workplace? Call now and one of our safety professionals can help guide you through the process at 1-888-326-9244.
DuraLabel’s free 5s Instant Action Guide helps set and reinforce facility standards, while optimizing safety and efficiency in any workplace. Download your free copy today.
Read Next:
Engage and Protect: Create a Safety Culture that Sticks
RELATED RESOURCES

Understanding the Four Types of Arc Flash
Understanding Arc Flash Arc flash incidents are among the most hazardous risks faced by personnel working ...
Read
Steps for Arc Flash Safety and Security in Electrical Substations
Electrical substations truly have the power. In the wrong hands, that power is dangerous. That's why it's ...
Read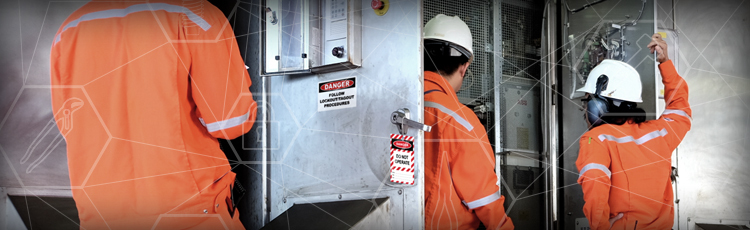
CMMS and Safety in the Workplace
Manufacturing and other industries are harnessing the power of CMMS for maintenance efficiency and safety. ...
Read