Boosting Workplace Efficiency Amid Labor Shortages: The Power of 5S
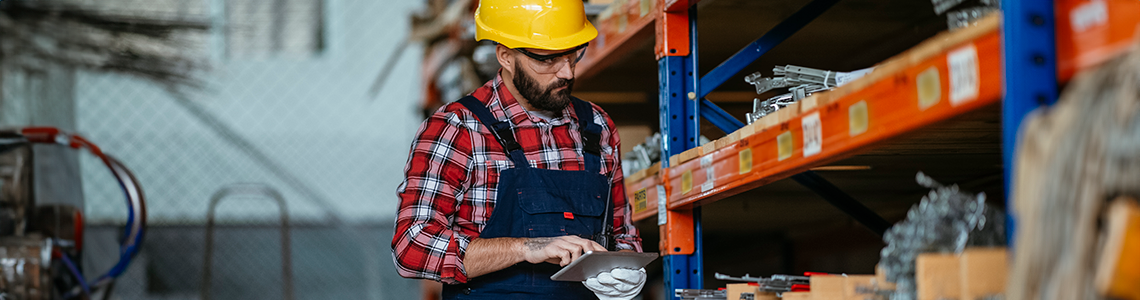
One of the most pressing challenges companies face is the shortage of skilled labor. As organizations strive to maintain productivity and quality in the face of this scarcity, implementing effective strategies becomes imperative. The adoption of 5S methodologies is an approach that has been swiftly gaining traction, coupled with enhancements in visual communication. Let’s look at how integrating 5S strategies and visual communication can bolster workplace efficiency, helping businesses navigate the hurdles posed by labor shortages.
Understanding 5S Methodologies:
Originating from Japanese manufacturing techniques, the 5S principles—Sort, Set in Order, Shine, Standardize, and Sustain—offer a systematic approach to organizing and standardizing the workplace. These principles, when combined with effective visual communication strategies, not only enhance efficiency but also contribute to workplace safety, morale, and sustainability.
-
Sort: Elimination of Unnecessary Items
The first step in the 5S methodology, Sort, emphasizes the removal of unnecessary items from the workspace, retaining only those essential for operations. This process reduces clutter, streamlines workflows, and optimizes space utilization. The goal is to create a lean environment that promotes efficiency and minimizes distractions.
Sorting involves evaluating each item based on its necessity, functionality, and relevance to daily tasks. It encourages teams to categorize items into 'keep,' 'remove,' and 'store elsewhere' categories. By implementing visual cues such as color-coded tags or labels, organizations can quickly identify items, enabling teams to make informed decisions during the sorting process.
-
Set in Order: Optimizing Layouts for Efficiency
Set in Order focuses on arranging essential items logically and ergonomically. This step involves creating designated locations for tools and materials which ensures that they are easily accessible and promptly returned after use. Visual communication plays a crucial role in this phase by utilizing floor markings, shadow boards, and signage to clearly indicate storage locations and workflow paths.
Organizations can standardize item placement, reducing search time and enhancing workflow continuity by incorporating visual indicators. For example, color-coded floor markings can denote specific work zones or storage areas by guiding employees to navigate the workspace efficiently.
-
Shine: Promoting Cleanliness and Maintenance
Shine emphasizes the importance of cleanliness and regular maintenance to uphold operational excellence and safety standards. Visual communication reinforces this aspect by employing visual checklists, signage, and color-coded cleaning schedules. These tools serve as reminders for employees, encouraging proactive participation in cleanliness initiatives.
Visual communication tools like cleanliness scorecards or maintenance charts can track compliance with cleaning schedules, fostering accountability and ensuring a consistently tidy workplace. The result is a safer, more organized environment that enhances employee well-being and productivity.
-
Standardize: Establishing Consistent Procedures
Standardize involves creating and implementing standardized procedures for maintaining the organized workspace. Visual standard operating procedures (SOPs) play a critical role in this phase by providing clear, visual guidelines for performing tasks consistently. Visual aids such as flowcharts, diagrams, and process maps simplify complex procedures, reducing errors and variability.
Visual SOPs ensure that every team member follows the same protocols, promoting efficiency and quality control. By visualizing workflows and procedures, organizations can streamline operations and adapt quickly to changing demands or staffing transitions by visualizing workflows and procedures..
-
Sustain: Cultivating a Culture of Continuous Improvement
Sustain is the final stage of the 5S methodology, emphasizing the importance of sustaining these practices over the long term. Visual performance metrics, progress charts, and employee recognition boards encourage continuous improvement and reinforce the value of 5S principles.
Visual communication tools highlight achievements, identify areas for improvement, and promote a culture of accountability and teamwork. Organizations empower employees to take ownership of maintaining the workplace's organization and cleanliness by integrating visual feedback mechanisms.
Visual Communication Tools from DuraLabel:
Visual communication serves as a cornerstone in the successful implementation of 5S strategies. By leveraging visual cues such as signs, labels, color coding, and floor markings, organizations can enhance communication, streamline processes, and reinforce adherence to 5S standards by leveraging visual cues such as signs, labels, color coding, and floor markings. Here's are five visual communication tools for each stage of the 5S methodology:
- Sort: Color-coded labels and visual indicators help distinguish between necessary and unnecessary items, facilitating the sorting process. Print OSHA and ANSI-compliant labels with the complete line of DuraLabel Industrial Label Printers.
- Set in Order: Floor markings and shadow boards outline designated locations for tools and materials, ensuring they are promptly returned to their designated spots after use. DuraLabel PathFinder® Floor Marking Tapes keep your facility organized.
- Shine: Visual checklists and signage remind employees of cleaning schedules and maintenance tasks, promoting a clean and safe work environment. Free downloadable checklists make maintaining your 5S system a breeze.
- Standardize: Visual standard operating procedures (SOPs) guide employees in performing tasks consistently and efficiently, which reduces variability and errors.
- Sustain: Visual performance metrics and progress charts foster accountability and motivation, encouraging employees to uphold 5S practices proactively. It is also important to train all employees on 5S methods and strategies.
Benefits of Integrating 5S and Visual Communication:
By combining 5S strategies with visual communication enhancements, organizations stand to reap a multitude of benefits:
- Improved Efficiency: Streamlined workflows and optimized layouts minimize wasted time and effort, boosting overall productivity.
- Enhanced Safety: Clear signage and visual cues promote safety awareness, reducing the risk of accidents and injuries in the workplace.
- Heightened Morale: A clean, organized, and visually appealing workspace cultivates a sense of pride and satisfaction among employees, fostering a positive work culture.
- Reduced Waste: By eliminating clutter and optimizing processes, businesses can minimize waste generation and associated costs, contributing to sustainability efforts.
- Greater Adaptability: The standardized and visually intuitive nature of 5S practices enables rapid adaptation to changing operational needs and staffing fluctuations.
Solutions from DuraLabel
In the face of labor shortages and evolving market dynamics, businesses must seek innovative solutions to maintain competitiveness and sustainability. Organizations can unlock new levels of efficiency, resilience, and employee engagement by embracing 5s methodologies and harnessing the power of visual communication. For customized guidance integrating these strategies, driving continuous improvement, and achieving operational excellence contact DuraLabel for a free consultation today at 888-788-9386.
DuraLabel’s free 5S Quick Start Guide will help audit, launch, and improve efficiency in your facility. Download a copy today.
Learn more about how to implement signage in your facility with DuraLabel’s Facility Signage Handbook. It helps take the guesswork out of facility requirements and products designed to your facility specifications.
Related Resources
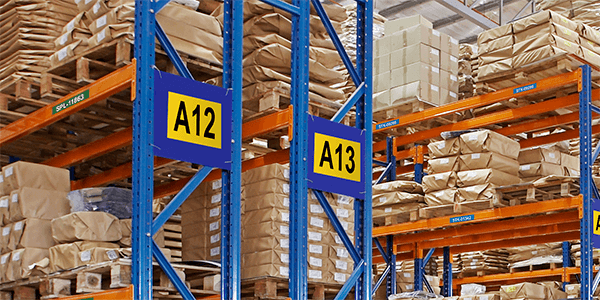
5S Examples in Action: The Good, the Bad, and the Successful
Can 5S Improve Efficiency and Engagement Across Industries? The 5S systemis a proven method for improving ...
Read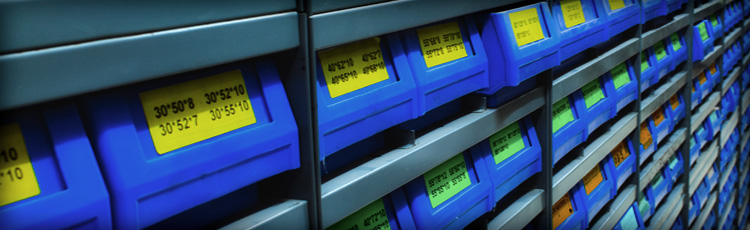
Creating a Visual Factory with the 5S System
What Is a Visual Factory with the 5S System? The term "visual factory" refers to an approach to lean ...
Read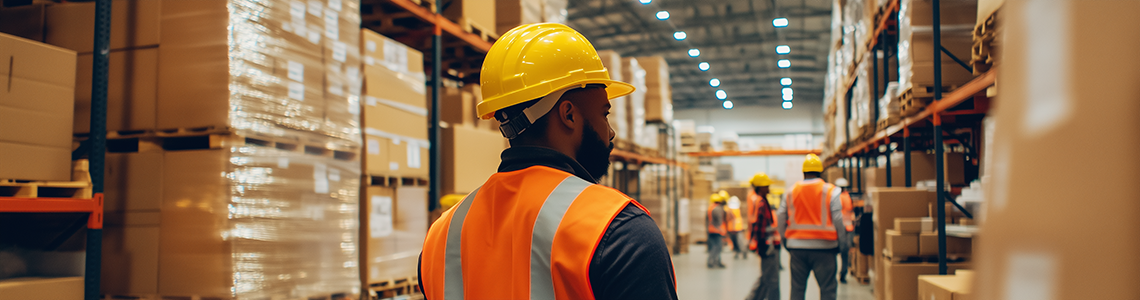
How to Build a 5S Implementation Team for Lean Success
What is a 5S Implementation Team? A 5S implementation team is a group of individuals empowered to make quick ...
Read