Building a Safer Work Environment: 5 Powerful Benefits of Safety Training
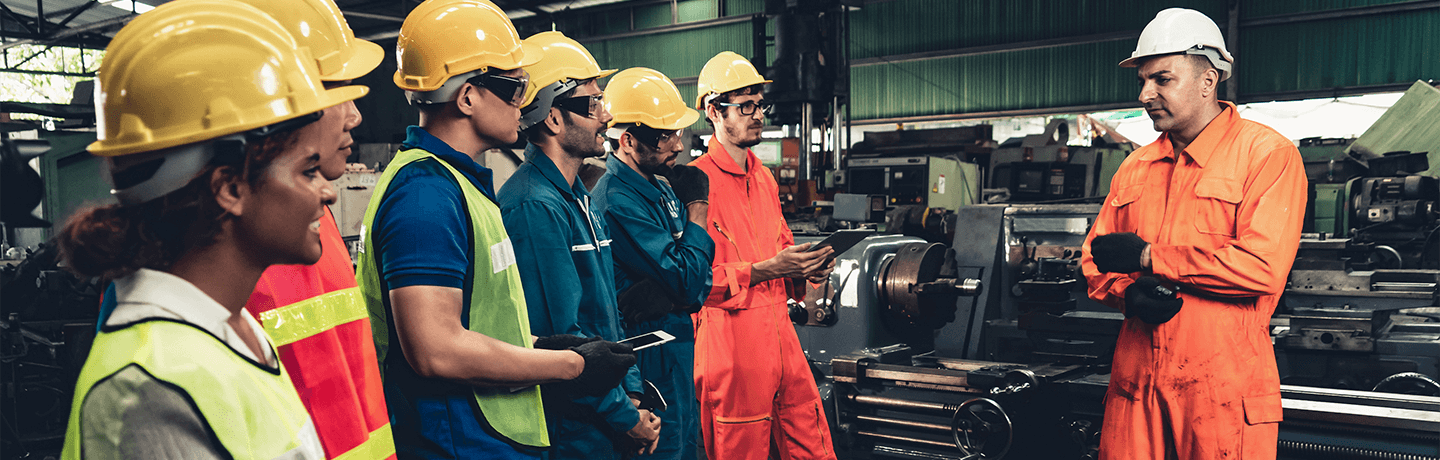
There are 12,900 worker-related injuries every day, according to the National Safety Council, and this equates to one injured person every 7 seconds. Most injuries are due to human error and are often preventable. OSHA's training standard for all industries says all workers must be trained in the tasks, situations, and tools they will use on the job.
- The construction industry has the most workplace deaths each year
- 12,900 worker-related industries each day
- 21,400 non-fatal injuries due to slips, trips, and falls
Training is an investment for both companies and the people they employ, so why are companies that shell so much money into it not receiving quality results? To understand what to do, we first need to understand what not to do.
There are major benefits to regular worker training and often includes enhanced employee performance and a boost in productivity. OSHA conducted a study on safety programs in 8 states and found that training workers on how to be safter reduced the number of injuries by 9-60%. Consider these 5 training benefits:
- Create awareness—Workers should be informed of any hazards that can occur while they are performing their job duties and trained on how to avoid accidents. Safety signs and labels play a big part in this creation of awareness by reminding workers to be alert in job processes through visual cues.
- Boost productivity— Fewer workers calling in sick or missing work are the result of effective training practices being put in place. The more familiar workers are with safety procedures, the more comfortably they will be able to navigate the job site, and this will lead to fewer accidents.
- Improve company culture— An environment where everyone feels validated does not happen overnight, but processes can be implemented and enforced to speed this along. Create regular training sessions that focus on areas where workers struggle the most and follow it up with visual reinforcements such as signs and labels with and provide tips on how they can improve.
- Reduce employee turnover— Companies that encourage their workers to learn more have a 50% engagement and retention rate. The reason the rate is so high is due to employees feeling a sense of motivation to progress in their jobs. When employees do not feel motivated, they often experience a burn out. According to the U.S Chamber of Commerce 1,000 full-time employees were surveyed in 2021: 40% left their previous jobs due to burnout. 28% of employees left their jobs due to burnout and did not secure another position.
- Improve team functionality— Knowing your team will play a crucial part in improving its functionality. Talk to them and get to know their strengths and weaknesses. This way training can be tailored toward optimal effectiveness. “61% of employees in teams led by managers who focus on strengths, are engaged” (Gallup)
How to Create Visual Safety Training that Works
No one benefits if workers are improperly trained. Not only can it negatively impact morale, but businesses can be affected if too much time is wasted on things that do not enhance their workers. Training workers on things that do not reflect in their day-to-day duties often creates stress too.
When managers have reoccurring training on safety standards for new and existing workers, it helps the information stick. There are a variety of effective training methods for various learning styles that range from videos to on-site- training.
Safety signs and labels are designed to be a visual method that reinforces training. All signs and labels must comply with OSHA and ANSI applicable regulations by using universally recognized symbols or icons, and be in visible locations to maximize their impact and effectiveness. Training workers on where these signs are located and why they have been placed there is an important step for reducing workplace injuries. Here are three types of signs and labels you may see in your facilities and their purposes:
- Instructional labels: Use labels with visual instructions to guide employees on how to operate equipment or perform specific tasks. These labels can be placed directly on machinery, tools, or equipment to provide clear step-by-step instructions.
- Equipment maintenance labels: Attach labels to equipment or machinery to indicate maintenance schedules, maintenance procedures, or service contact information. These labels can help employees keep track of maintenance requirements and promote equipment longevity.
- Emergency evacuation signage: Install clear and well-placed signs throughout the workplace that indicate emergency exits, evacuation routes, and assembly points. These signs should be highly visible and easy to understand, aiding employees during emergency situations.
Find the methods that work best for your workers and implement them into your training sessions. Create an environment where safety becomes a part of daily operations. This will result in a safer and positive work experience for everyone. Creating a culture of safety will take time and effort. Consistency and active employee engagement are two primary components to improve workplace safety programs, which leads to fewer incidents, better productivity, and higher morale.
Sources
“Only One in 10 People Possess the Talent to Manage” Gallup
“4 Essential Safety Measures to Prevent Construction Job Site Injury” Build
“What is the Link Between Training and Retention?” EnduMe
Related Resources
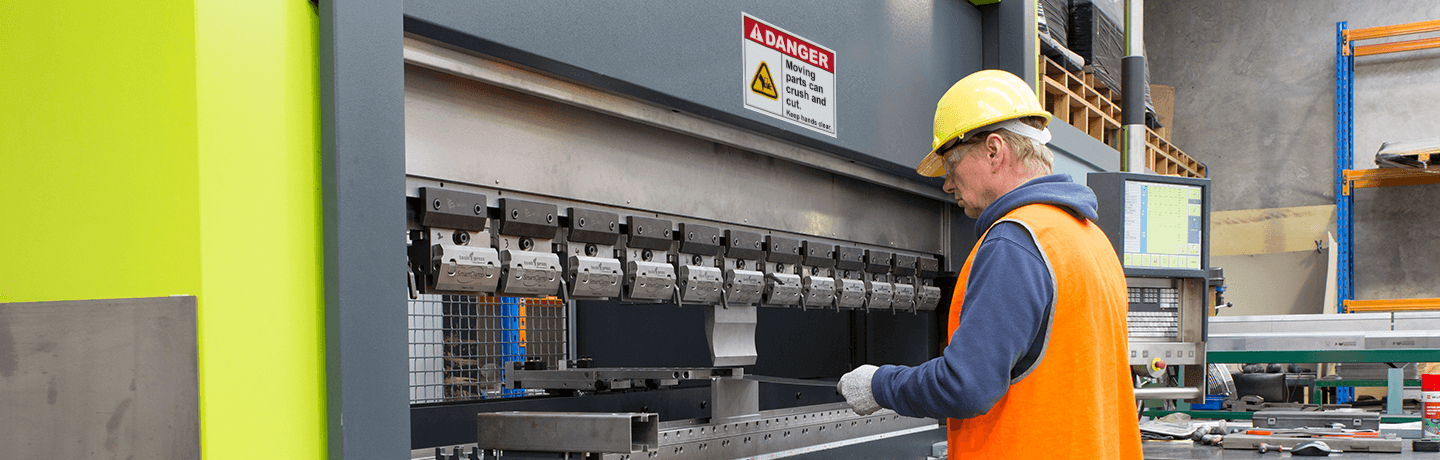
9 Tips for Effective Safety Messaging to Prevent Common Injuries
Organizations are required under the OSHA General Duty clause to provide a working environment "free from ...
Read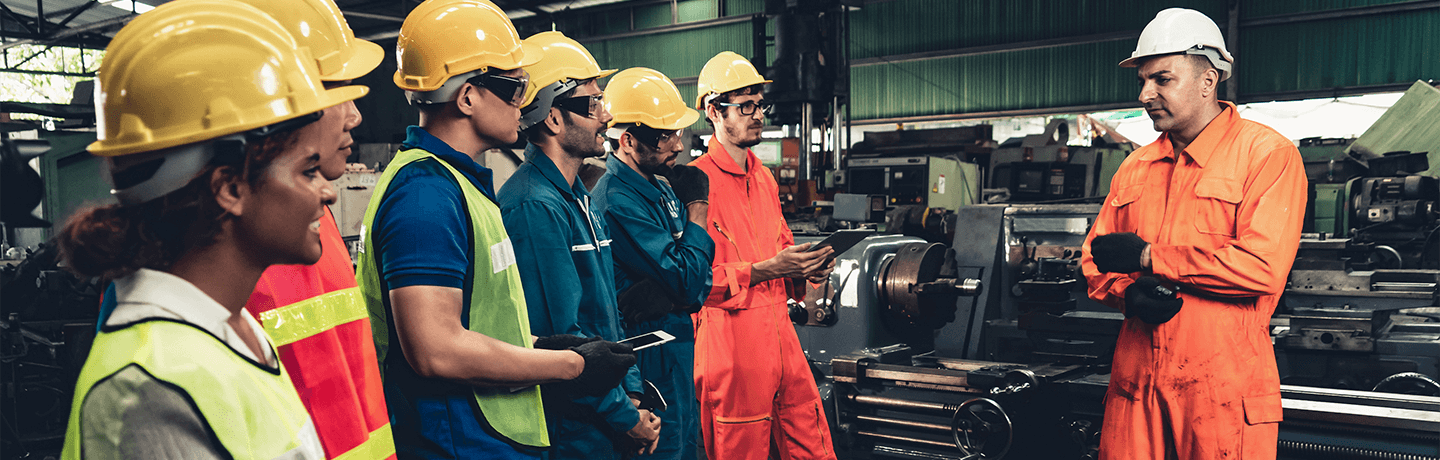
Tips From Fipps: It Pays to Be Safe, The Business Case for Workplace Safety
Workplace safety is not only crucial for protecting employees' well-being but also for the overall success of ...
Read
Tips from Fipps: Be Your Own Safety Superhero
Ensuring a safe and secure work environment is a shared responsibility that each one of us plays a crucial ...
Read