How to Strengthen Building Safety in Manufacturing Facilities
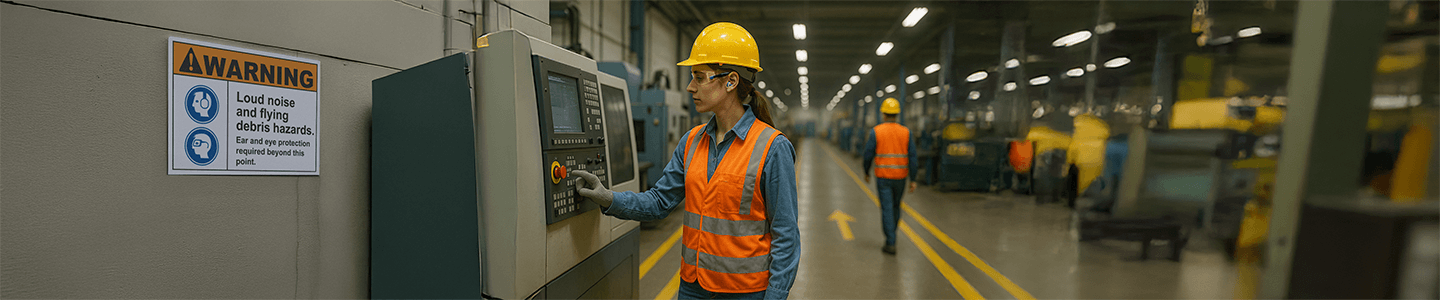
How Do You Keep Manufacturing Facilities Safe and Operational?
Building safety in manufacturing facilities requires more than routine inspections. While buildings are designed for durability, issues like hidden structural fatigue, degraded wiring, or missing safety signage can easily go unnoticed until they lead to serious injuries, shutdowns, or regulatory action. These risks can result in fines, lawsuits, or even fatalities if not addressed proactively.
To avoid these outcomes, building safety must be treated as an ongoing system that includes regular inspections, preventative maintenance, and clear communication using compliant safety signage. A strong building safety program protects workers, ensures uptime, and positions facilities to stay ahead of OSHA requirements and costly surprises.
Why Does Building Safety in the Workplace Matter?
Building-related hazards threaten not only construction workers or engineers but everyone in the facility, whether on the floor, in maintenance, or behind a desk. When safety systems fail, the impact is broad and often avoidable.
According to the Occupational Safety and Health Administration (OSHA), unsafe conditions, such as inadequate exits, structural hazards, and poor signage, are among the leading contributors to workplace injuries.
Effective visual communication using signs, labels, and floor markings helps prevent confusion. Clear instructions support safe decisions and faster responses when something goes wrong.
Maintaining building safety protects workers, promotes regulatory compliance, and supports a culture of prevention.
What Are Common Building Safety Risks?
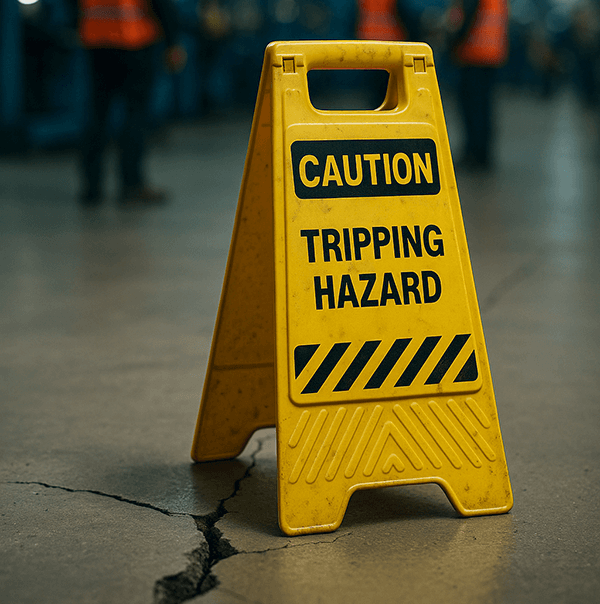
Even well-maintained workplace buildings need proactive safety measures to identify and address hidden risks. Risks often develop gradually, through aging infrastructure, inconsistent maintenance, or failure to enforce established safety protocols. Without regular evaluation and corrective action, these issues can compromise building safety, interrupt operations, and result in noncompliance with safety regulations.
Common safety threats risks include:
- Structural issues: Cracked walls, sagging ceilings, or weakened support beams.
- Fire hazards: Outdated wiring, blocked fire exits, or overloaded circuits.
- Trip and fall hazards: Loose flooring, poor lighting, and wet surfaces.
- HVAC system issues: Poor air quality, mold buildup, or temperature control issues.
- Accessibility obstacles: Broken elevators, blocked pathways, or lack of ADA-compliant features.
- Signage and labeling gaps: Missing evacuation maps, hazard signs, or equipment labels.
How Can Employers Improve Building Safety?
Building safety starts with consistency. Employers must take deliberate steps to assess risks and enforce protocols that reduce hazards. A strong safety program includes scheduled inspections, updated signage, and clear emergency procedures. These actions protect workers and integrate safety into the daily routine.
To improve facility safety and reduce risk, employers should:
- Conduct regular building inspections: Assign qualified inspectors to evaluate structures, exits, HVAC systems, and utilities using appropriate digital tools.
- Implement preventive maintenance programs: Schedule maintenance to identify and address early signs of wear or failure.
- Upgrade facility signage systems: Keep warning signs, evacuation maps, and hazard labels current and visible. Custom safety signs help clarify risks in specific areas.
- Enhance staff training: Run regular drills and teach staff how to respond to hazards and emergencies.
- Establish a facility safety documentation system: Record inspections, repairs, training sessions, and compliance activities clearly and consistently.
- Strengthen visual communication in safety protocols: Use floor markings, signs, and labels to identify hazards, routes, and emergency equipment. Effective visual cues help workers act quickly and confidently when issues arise.
What Are the Signs That a Building Might Be Unsafe?
Building-related hazards are rarely abrupt. They are often signaled by early, observable conditions that warrant immediate attention. Overlooking these signs can result in regulatory violations, workplace injuries, and significant operational setbacks.
Recognizing early indicators of building-related issues is critical for maintaining regulatory compliance, mitigating liability, and preventing operational interruptions. These signs often precede more severe hazards and should be addressed without delay. Common indicators include:
- Persistent or unusual odors (e.g., gas, mildew)
- Water damage or leakage
- Electrical flickering or outages
- Visible foundation or wall cracks
- Structural noises (e.g., creaking, popping)
- Doors or windows that fail to open or close properly
These conditions should be reported to safety or facility management immediately for evaluation and corrective action. Prompt intervention can prevent minor issues from escalating into costly liabilities.
Strengthening Building Safety in Manufacturing Environments
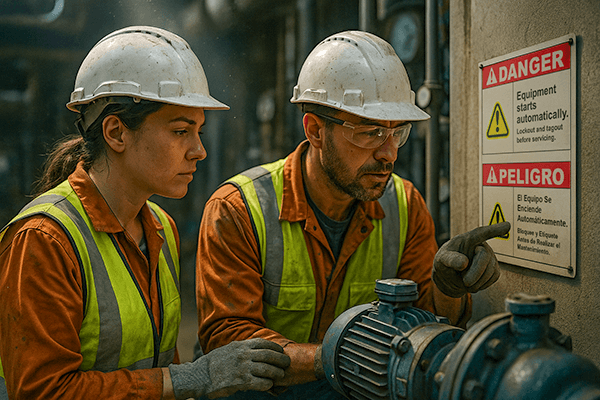
Building safety plays a central role in protecting workers and maintaining safe operations. In industrial environments, where equipment, materials, and personnel interact constantly, even small facility issues can escalate quickly. Routine inspections, clear communication, and consistent maintenance help reduce risks and support compliance.
Manufacturing facilities face heightened risks due to fast-paced operations and heavy machinery. Common hazards include obstructed exits, ventilation issues, outdated fire protection systems, and missing or unclear equipment labels. Without routine oversight and clearly communicated safety procedures, these conditions can quickly become serious hazards.
According to the Bureau of Labor Statistics (BLS), the manufacturing sector reported approximately 385,100 nonfatal workplace injuries in 2022. Many of these incidents were linked to environmental and structural hazards. Addressing such vulnerabilities requires a coordinated approach grounded in visibility, accountability, and regulatory compliance.
Key considerations for building safety in manufacturing include:
- Routine inspections of structural systems and equipment areas to identify signs of deterioration or improper installation.
- Use of custom safety signs to communicate specific hazards relevant to particular zones or machinery.
- Implementation of clear facility signage systems that support efficient evacuation and emergency response.
- Proper ventilation and HVAC maintenance to support indoor air quality and temperature control.
- Deployment of visual communication tools such as floor tape, warning labels, and color-coded pathways.
- Integration of digital inspection tools to streamline reporting, documentation, and corrective action planning.
A systematic approach to building safety reduces workplace hazards and lowers the risk of injury. It reinforces OSHA compliance while protecting both personnel and the infrastructure that supports daily operations.
Build a Safety Culture that Supports Building Safety
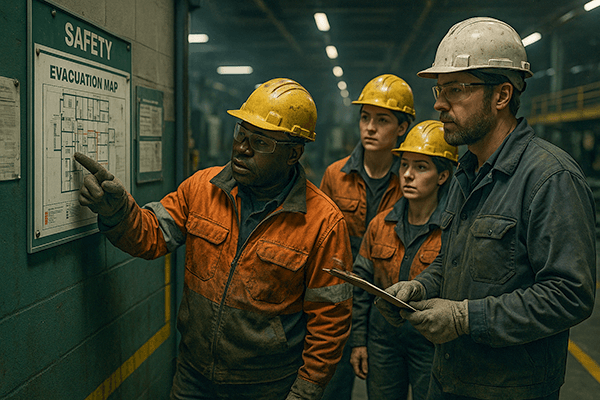
A strong safety culture depends on participation from everyone in the facility. While policies and procedures establish expectations, employee engagement drives them forward. Workers who feel responsible for their environment are more likely to notice and report risks, such as a flickering light, an obstructed walkway, or a missing sign.
Leaders play a key role by setting expectations and reinforcing them through clear communication and follow-through. Routine safety briefings, consistent messaging, and visible reminders, such as signage and floor markings, help keep safety top of mind.
Successful programs share common principles: engagement, consistency, and visibility. When employees see that their input is taken seriously, they are more likely to participate in hazard prevention efforts.
Effective visual communication in safety, such as signs, instructional labels, and floor markings, further supports a shared understanding of safe practices without requiring constant oversight. This clarity is especially important in fast-moving environments.
A culture built on shared responsibility doesn’t just reduce incidents. It empowers workers and strengthens the entire workplace.
DuraLabel OSHA Signage Resources
Building safety depends on communication, consistency, and shared accountability. In manufacturing environments, effective signage is essential for reinforcing safe behavior and guiding emergency response. Signs, labels, and floor markings clarify hazards, mark restricted zones, and support OSHA compliance.
DuraLabel offers a full range of visual communication tools, including pre-made Restricted Area Signs designed to meet OSHA formatting standards and improve hazard visibility.
For facilities that need flexibility and mobility, the DuraLabel Toro Max Industrial Label and Sign System makes it easy to create custom safety signs on demand. It is ideal for building-to-building maintenance or field operations. When applied consistently, these tools improve situational awareness and reduce the risk of accidents.
If your team is working to improve facility signage, the free OSHA Signage Quick Start Guide is a great place to begin. This guide explains the basic requirements of OSHA-compliant signage, including formatting, signal words, and application guidelines. It also includes real-world examples of facility signs, labeling best practices, and advice on material selection. Whether you’re updating existing signs or developing a facility-wide system, this guide can help ensure your visual communication strategy meets OSHA standards.
Have questions about OSHA or other labeling needs? Call us at 1-888-789-7964 and a safety and compliance specialist will guide you through the process.
Read Next
Engage and Protect: Create a Safety Culture That Sticks
OSHA Floor Marking Practices for a Safer and More Efficient Workplace
Related Resources
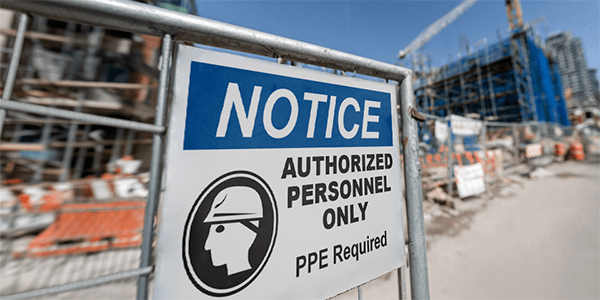
5 Industries that Benefit from Custom Workplace Signs and Why
Why Are Custom Workplace Signs Essential for Protecting Workers? In every high-risk workplace, silent ...
Read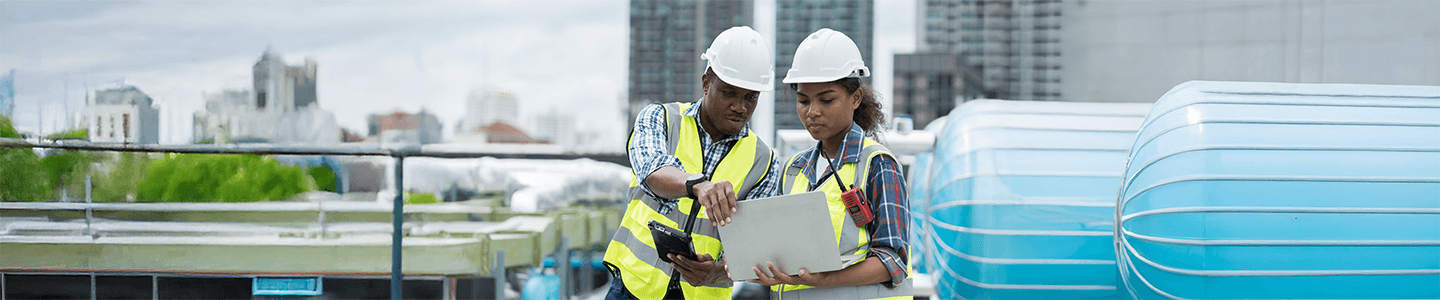
Top 5 Challenges Mechanical Project Managers Face
What Are the Biggest Obstacles Mechanical Project Managers Face? Mechanical project managers oversee ...
Read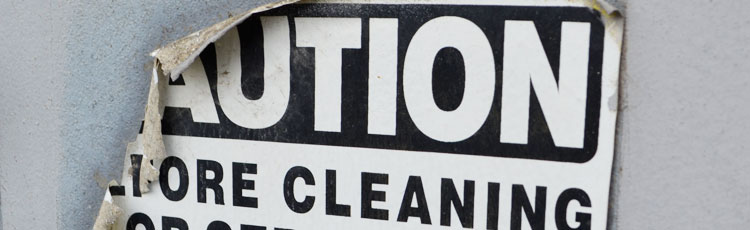
4 Signs Your Safety Communication Needs an Update
Safety signs and labels that are up to date, clearly worded, and in tact play a key role in achieving ...
Read