Common Questions about Chemical Laboratory Safety
More than 500,000 U.S. workers are exposed to all kinds of chemicals while working in laboratories. From chemical, biological, physical, and radioactive hazards to musculoskeletal stresses, laboratory safety is covered by multiple OSHA standards to address all types of situations.
What are the types of hazards found in laboratories?
Carcinogens, toxins, irritants, corrosives, sensitizers, hepatotoxins, nephrotoxins, neurotoxins, are all types of agents that can destroy parts of the body internally or externally. We're talking about your lungs, skin, eyes, liver, kidneys, mucous membranes-just to name a few.
Which OSHA standard covers laboratory safety?
Part 1910.1450 (Exposure to Hazardous Chemicals in Laboratories Standard) of the CFR covers all workers in laboratories. Some workers engage in work with hazardous materials including chemicals outside of laboratories. In those cases part 1910.1450 does not pertain due to various industries and jobs. You need to know details from other parts of the CFR such as 1910.1200, 1915.99, 1918.90, and 1926.56 which applies to general industry, shipyard, marine terminals, longshoring, and construction employment. Those standards cover chemical manufacturers, importers, employers, and employees exposed to chemical hazards.
While working in a lab you could be affected by the following hazards or standards which overlap chemical safety outside of Part 1910.1450.
- Toxic and Hazardous Substances, 29 CFR 1910, Subpart Z.
- Hazard Communication Standard (Now referred to as HazCom 2012) 29 CFR 1910.1200
How does Part 1910.1450 define a laboratory?
It does not over QC/QA laboratories found in manufacturing facilities. The standard covers labs that:
- Use hazardous chemicals.
- Use relatively small amounts of hazardous chemicals in a workplace that is nonproduction based.
- Use a variety of chemicals and chemical procedures.
- Maintain procedures that are not part of a production process.
- Implement practices to protect workers and use equipment designed to minimize employee exposure.
What must employees be informed of when beginning work in a chemical laboratory?
- Contents of the occupational exposure standard and its appendices.
- Location and availability of the employer's chemical hygiene plan.
- Permissible Exposure Limits (PELs) for the hazardous substances to which the employees are exposed.
- Signs and symptoms associated with exposures to hazardous chemicals used in the laboratory, and;
- Location and availability of known reference material on the chemical hazards, and their safe handling, storage, and disposal including but not limited to, Safety Data Sheets (SDSs) received from chemical suppliers.
What is a Chemical Hygiene Plan (CHP)?
A CHP is the lab's program, created by the employer, which carries out all parts of the 1910.1450-relating to exposure of hazardous chemicals.
The CHP does the following:
- Addresses all aspects of procurement, handling and storage, and disposal of chemicals used within the laboratory and facility.
- Sets forth procedures, standard operating practices of equipment, personal protective equipment, and work practices designed to protect the employee.
The primary elements of the CHP are:
- Training
- Employers are responsible for providing training and information on the hazards of all the chemicals which employees are exposed to.
- Employees must be trained concerning the following:
- Methods of detecting the presence or release of a hazardous chemical;
- Hazards (both physical and health) of chemicals in the work area;
- Measures that workers and their employers can take to protect employees from hazards, including specific procedures the employer has implemented to protect employees from exposure to hazardous chemicals, such as appropriate work practices, emergency procedures, and personal protective equipment, and
- Details of the employer's written chemical hygiene plan.
- Employee Exposure
- Employee exposure levels must be measured when OSHA regulated substances are used. Ongoing monitoring is required. Results of monitoring must be disclosed in writing to employees 15 working days from occurrence.
- Medical Consultation
- Employees can undergo medical consultation at no cost if:
- The employee shows signs or symptoms related to exposure of chemical hazards.
- It's revealed that exposure levels are above the permissible exposure level.
- A spill, leak or explosion results in the likelihood of a hazardous exposure.
- Employees can undergo medical consultation at no cost if:
- Hazard Identification
- Refer to CFR 1910.1200 for provisions on the maintenance of Safety Data Sheets (SDSs). Follow HazCom 2012 guidelines for labeling hazardous material. Ensure that labels of containers with hazardous chemicals are not defaced or removed.
- Respirators
- Respirators should be provided to employees at no cost if needed to bring exposures below the permissible exposure limit.
- Recordkeeping
- A record of the employers CHP should be up-to-date and accessible for all employees.
- Fume Hood Program
- Hoods need to be routinely checked to ensure proper functioning. Taking inventory and periodic surveys of performance are should be part of the evaluation.
Learn more about evaluating hazardous substances in the laboratory. You can perform self-inspections once you're fully trained on your facility's chemical hygiene plan and hazardous substance communication. Self-inspections will increase safety and efficiency for everyone in your workplace. For a deeper-dive into chemical hazards, download our free HazCom 2012 Labeling Guide to learn the ins-and-outs of chemical labeling. Get your free copy below
Related Resources

Labeling is Crucial: Safety in Bulk Chemical Handling
Safety in handling bulk chemical unloading is a procedure that requires careful work and optimal ...
Read
Ensuring Lab Safety with Proper Labeling
A Comprehensive Guide for Pharmaceutical Companies In the realm of pharmaceutical research and development, ...
Read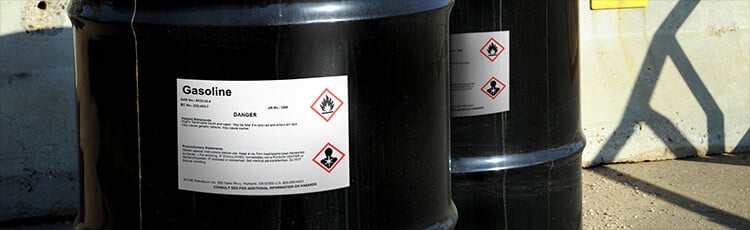
The GHS Framework: Labeling & Compliance
Every two years, the UN publishes a new revision of the Globally Harmonized System (GHS), a standardized ...
Read