Five Essential Forklift Safety Tips

Forklifts play an essential role in warehouses, retail outlets, and other businesses throughout the United States. More than 1,000,000 forklifts are in operation, shuttling inventory while helping employees stay productive, efficient, and organized.
Despite their reputation for improving efficiency, forklift-related citations are routinely among OSHA's top 10 violations each year. The agency estimates 110,000 accidents involving forklifts occur yearly, and those accidents cost businesses an estimated $135,000,000.
What can employers do to keep workers safe? Here are five tips for improving forklift safety in facilities of any size.
1. Offer Forklift Safety Training
Before an employee takes control of a forklift, they must receive training that meets OSHA requirements. OSHA's standard on powered industrial trucks (29 CFR 1910.178) requires employers to offer the following as part of a forklift safety training program.
- An employer's training program must cover the following:
- General rules of safe operation
- The types of trucks used on site
- Hazards created by forklifts and powered industrial trucks
- OSHA's general safety requirements
- Trainees may only operate a forklift under the supervision of an employee with the training and experience to instruct others
- Trained operators must demonstrate in a workplace evaluation that they know how to do the job safely
- Employers must provide formal training that may consist of lecture, video, software training, written material, demonstrations, and hands-on experience
- Employers must certify that the employee has received all required training and evaluate each forklift operator at least once every three years
- Employers must assess the operator's performance and deem the employee capable of operating a forklift before getting behind the wheel
- Employees must take refresher training whenever they demonstrate a deficiency or inability to safely operate the forklift
2. Check for Hazards Before Operating
Kicking tires and checking oil levels isn't just for long road trips: forklift operators should perform a thorough inspection to ensure a forklift is safe before operation. Here are the steps employees and employers should follow before getting behind the wheel:
- Examine the tires and oil levels
- Check for water, oil, or radiator leaks
- Ensure forks are straight and not cracked
- Test brakes, lights, horn, and steering wheel
- Look for obstructions, uneven surfaces, overhead obstacles, and other potential hazards
3. Keep Employees Safe While Operating a Forklift
There are three primary dangers forklifts pose to workers in a facility:
- Forklifts compete for space with inventory and pedestrians: The potential for accidents between forklifts and pedestrians increases when aisles, pathways, and storage areas aren't marked.
- Pedestrians wander into harm's way: Accidents are more likely to occur when forklift operators don't drive with best practices in mind-or when safety controls don't remind pedestrians to be careful or avoid an area altogether.
- Loads fall over: A forklift's load may tip over when the operator hasn't inserted the forks under the pallet as far as possible, loads are imbalanced or unsecured, or when the operator drives with the load higher than recommended.
Knowing those dangers, forklift drivers can take several steps to keep themselves and their coworkers safe while operating a forklift. Here are a few common actions to improve forklift safety:
- Pay attention: Watch for posted speed limits, warning signs, intersections, and floor markings. Operators should also steer clear of areas where forklifts are prohibited or restricted.
- Keep an eye on where you're going: Always look in the direction you're traveling; if a load blocks the view ahead, travel in reverse.
- Alert others of your presence: Use the horn at intersections and where pedestrians may be present.
- Ensure the load is balanced: An imbalanced load can fall off or cause the forklift to tip over.
- Drive safely: Ensure both forks are as far under the load as possible before lifting and drive with the load as low as safely possible.
4. Use Floor Marking to Keep Workers Safe
Floor marking can create aisles, improve workflow, and warn of hazards where forklifts might be present.
Here are a few ways that floor marking can help:
- Create clear aisles and pathways: Aisle markers and pathways alert pedestrians to the presence of forklifts, create separate paths for pedestrians and forklifts, and safely direct traffic throughout a facility. A printable tape can also indicate the direction of traffic. Each of these instructions can help a forklift driver operate safely and more efficiently in congested corridors.
- Use floor signs to create traffic controls: Clear, easy-to-read floor signs warn drivers of speed limits, inform pedestrians of nearby forklifts, notify workers when pedestrians or forklifts aren't allowed in an aisle, establish right-of-ways at intersections, and more.
- Reroute pedestrians: Thoughtful floor marking may keep employees away from forklifts and moving loads.
- Can you use floor signs and aisle markers to send employees around the edges of a busy warehouse?
- Can floor marking direct employees through pedestrian-only zones that are off-limits to forklifts?
- Identify important areas: Floor marking can point out loading docks, warehouse doors, ramps, and other areas that might involve hazards.
- Cordon off storage areas: Alert employees to inventory, pallets, and other materials that forklifts might lift and transport around a facility.
- Create boundaries around forklift parking and charging areas: Designated parking areas remind employees not to leave materials there when forklifts are absent and encourage safe practices at all times. Boundaries may also prevent employees from tripping over a forklift's forks.
Though OSHA does not explicitly require any kind of floor marking, its standard on materials handling and storage (29 CFR 1910.176), OSHA says simply: "Permanent aisles and passageways shall be appropriately marked." If forklifts consistently travel between certain areas in a facility, marking those areas helps improve safety and brings you into OSHA compliance.
Beyond that broad requirement, these OSHA interpretations can help steer floor marking decisions:
- The floor markings used to define an aisle may be any color, so long as they make it clear the area is an aisle.
- Floor marking lines should be 2" to 6" wide; any width of 2" or more is acceptable for ensuring maximum visibility.
- Aisles should be a minimum of 4' wide, or at least 3' wider than the largest piece of equipment utilized within the aisle.
- When appropriate or necessary, OSHA allows facilities with unusual surfaces (like dirt floors) to use materials or methods other than paint and tape (most commonly used in conventional warehouses and stockrooms).
OSHA's standard for walking and working surfaces (29 CFR 1910.22) sets no guidelines for specific floor marking colors, but the agency's standard for safety color codes (29 CFR 1910.144) specifies that red and yellow must be used for marking physical hazards.
- Red is for fire-related hazards (identifying fire protection equipment and containers of flammable liquids, for instance), as well as emergency switches, bars, and buttons on hazardous machines.
- Yellow indicates caution and to mark physical hazards (including stumbling, falling, and "caught in-between").
For common standardized floor marking colors that can improve communication, and increase efficiency, download a free one-page Floor Marking Color Chart.
5. Improve Safety Throughout Your Facility
Take steps throughout your facility to keep workers safe while others operate forklifts. Here are a few ideas:
- Use visual communication: Use safety signs, traffic control signs at intersections, aisle markers, and forklift procedure labels with premade signs, custom labels, or a combination.
- Be alert: Nearby workers should watch for unsecured or imbalanced loads, listen for horns, keep away from areas where pedestrians may not be allowed, and be able to make eye contact with any forklift driver in the area.
- Use lockout/tagout devices (LO/TO): Use steering wheel covers and padlocks when necessary. LO/TO equipment prevents forklifts from inadvertently starting up during service or maintenance.
Resources for Forklift Safety
Warn, direct, and support employees in a wide variety of environments with PathFinder floor marking and safety tapes. Our floor marking solutions include anti-slip tapes to prevent slip-and-fall hazards, reflective tapes for increased visibility, heavy-duty tape for heavy-traffic areas, durable floor signage, and more.
Establish and improve your visual communication with Duralabel' Best Practice Guide to Floor Marking. The free guide looks at the benefits of floor marking, shares real-world examples of effective floor marking, and includes an inspection sheet to enhance your floor marking system.
Related Resources
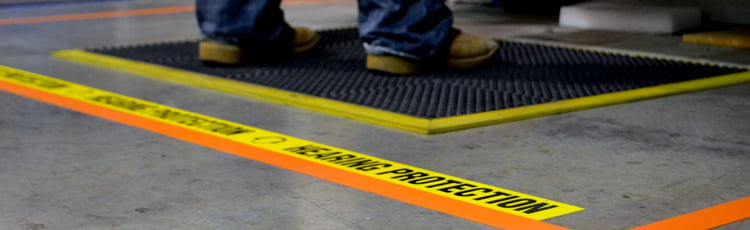
Spring Cleaning Safety Checklist: Floor Marking
When organizing and cleaning up work spaces this spring, consider changing up floor marking for safety, ...
Read
Industrial Wayfinding 101: Navigating the Terrain of Industrial Spaces
In the sprawling landscapes of industrial facilities, warehouses, and manufacturing plants, effective ...
Read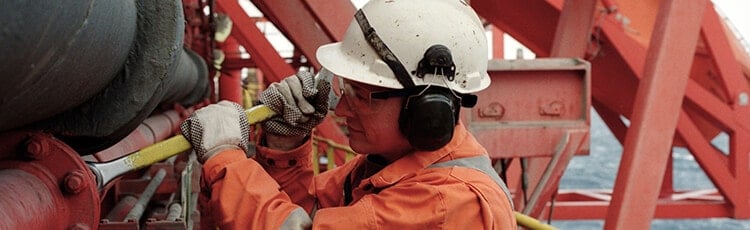
Best Workplace Upgrades to Make Before Fall
It's easy to let time slip away, but when there's work to be done, don't wait until the last minute. Here's a ...
Read