From MSDS to SDS
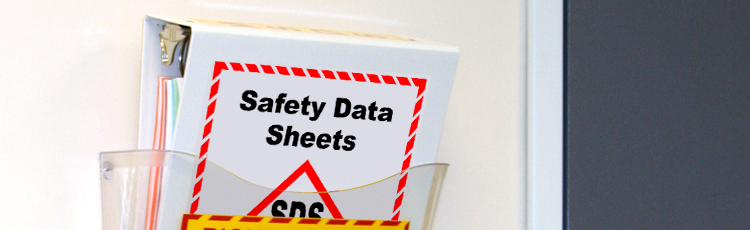
OSHA's HazCom 2012 rules require companies to have a Safety Data Sheet (SDS) for every hazardous chemical in the workplace. The SDS sounds like the old Material Safety Data Sheet (MSDS), but it's not quite the same. For the difference to make sense, you need to know some of the story behind the change.
The Change from MSDS to SDS
Workers have a right to know about the chemical hazards they might be exposed to at work. That's why "Right To Know" (RTK) became a common name for a set of OSHA's older rules about chemical labeling, published in 1994.
One part of the RTK rules required employers to keep a document on file for each hazardous chemical in their facility. These documents gave data about the safety concerns of each material, so they were called Material Safety Data Sheets (MSDS). Since OSHA didn't require any particular MSDS format, two MSDSs for the same chemical could look completely different. This led to a lot of confusion. What good is a "right to know" if you can't understand and act on that knowledge?
OSHA published a major change to the RTK rules in 2012, creating a new system called HazCom 2012. The new rules were based on an existing international standard called the Globally Harmonized System (GHS), which was already popular elsewhere. Under the new rules, workers would have a right to understand chemical hazards, and not just to know about them. To achieve this, the new rules require a single, specific format to be followed in the documents for hazardous chemicals. This format is the Safety Data Sheet (SDS).
The Role of the SDS
Both GHS and HazCom 2012 start by classifying the hazards of a chemical with laboratory tests. Both systems end by posting a standard set of useful information on the container labels that employees will see during their work. The SDS fits between these two steps: it records the results of hazard classification, and provides the detailed information that will be needed on a label. The SDS also gives the information needed for other aspects of a chemical safety program.
Without a standard SDS, the details from the classification stage could be lost. Making an accurate container label would become an enormous task. A complete and compliant SDS can answer any question about a chemical's hazards, though. Using the standard SDS format, chemical suppliers can provide the necessary information reliably and consistently. The people who use those chemicals can understand the information they need to know.
What's the Difference Between an MSDS and an SDS?
The difference between the old MSDS and the new SDS is more than just the "M" at the beginning. The old MSDSs could follow any number of different formats, and could include different kinds of information with different levels of detail. The new SDS format is much stricter. An SDS is made up of sixteen sections, and each section includes specific information using a standardized classification method.
There is likely to be a lot of overlap between an MSDS and an SDS for a given chemical. For instance, a flammable liquid will probably have its flash point noted on both forms. But converting from MSDS to SDS may not be easy. Not all of the details required for an SDS may have been included on the old MSDS. Because there are dozens of ways to organize an MSDS, it may take a careful reading to find out which details are missing.
If moving from an MSDS to an SDS is more than a simple translation, how are businesses supposed to make the change? Fortunately, the process is simpler than you may think.
Request an SDS from Your Supplier
If your hazardous chemical is provided by an outside organization, that supplier is responsible for providing an updated SDS. You may have already received an updated SDS along with your recent shipments. If not, you can request a current SDS by contacting your supplier. Many companies provide these forms on their websites, as well.
"Translate" from MSDS to SDS
If your facility produces the chemical in question, you'll need to make an SDS yourself. This isn't so much about "translating" between formats as it is "filling in the blanks." Don't start with your existing MSDS and try to translate it; instead, start with a listing of the details you need, and copy items over from the existing MSDS. You may find that you don't have some of the required elements. If so, those will be the points that you need to find test results for.
SDS Criteria
In general, every chemical in a workplace that poses a hazard defined by the HazCom 2012 system will need to have an SDS on file in that workplace. Each SDS needs to have 16 sections, organized in a specific, logical sequence, with the goal of making the SDS easy to understand.
- Sections 1-3 give the most basic and important information. They identify what the material is, what hazards it poses, and what important ingredients it includes.
- Sections 4-8 tell workers how to deal with the material. This advice starts with the most urgent concerns, and works down to day-to-day safety.
- Sections 9-11 go into detail about the nature of the material itself, and where its hazards come from.
- Sections 12-15 cover concerns that are not part of OSHA's jurisdiction. These sections are still required as part of the standard SDS format, but they don't directly relate to OSHA's concerns of workplace safety. Environmental concerns and transportation requirements are included here.
- Finally, section 16 is a catch-all for details that might not fit somewhere else, especially information about the document itself-like the date when the SDS was prepared.
OSHA lists these sections, along with the details that need to be included, in Appendix D to the HazCom 2012 regulations. You can use that listing as a framework for your own SDS, filling in the blanks to create a complete and compliant Safety Data Sheet.
Related Resources

Understanding the SDS (Safety Data Sheet)
Chemical safety can be a massive puzzle, with a variety of interconnected elements: inventory lists, storage ...
Read
Hazardous Chemicals Overview
In the eyes of OSHA, hazardous materials run the gamut from household cleaners to deadly gasses. Effects can ...
Read
OSHA and Canada Partner for Chemical Labeling System
Canada and the United States have been working together to align their laws for classifying and labeling ...
Read