Inventory Planning
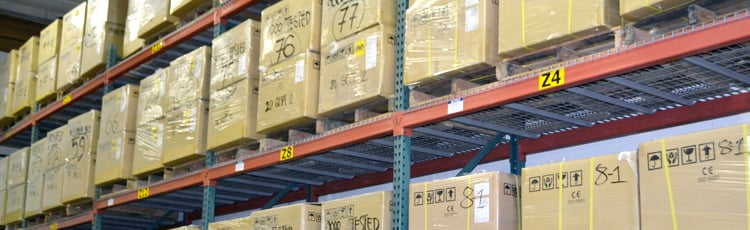
What is Inventory?
The word "inventory" can have a number of definitions. In this article, we'll be talking about inventory in the sense of an accumulation of material, parts, supplies or products. This might be an inventory of products for resale. It might be the in-stock supply of parts and materials used to manufacture products. An inventory might also be the supply of spare parts, supplies and materials needed to service and repair the machines that make the products. It can also be an inventory of materials that are not directly related to production, such as an inventory of safety supplies.
What is Inventory Planning?
There is a significant cost associated with inventory. The items in inventory must be purchased and the invoices paid. Inventory uses space that must be built or leased. The space must be heated and lighted, resulting in monthly utility bills. Plus, there is the cost of money used to finance the inventory. All of these add up to a significant cost that needs to be minimized. This is, in part, what inventory planning does. Inventory planning also ensures that items are available when they are needed. It establishes reorder points, and minimum stocking levels.
Inventory planning system needs gather information from across departmental lines, including the operations, production, and the maintenance departments. For example, the maintenance department will provide information that identifies what replacement parts will be needed and when they will be needed.
What are Inventory Turns?
Inventory turn is an important part of inventory planning. The term "inventory turn" refers to the number of times an item is 100% used (completely removed from inventory) and replaced. For example, if 100 units are used each year, and typically 10 units are stocked. The inventory turn is ten. The inventory of that item is completely replaced ten times each year.
In some cases, inventory turns may not be important. For example, if a critical part is needed for a machine, that part may always be kept in stock even if it is not frequently used. The inventory turn for that item may be very low, but having several in stock when they are needed may save a significant amount of money.
Inventory planning must take all of these factors into account.
Other Objectives of Inventory Planning
Some of the objectives of inventory planning include eliminating redundancies and preventing obsolescence.
Redundancies happen when too many of an item are in inventory, or several different items that all serve the same purpose are being stocked. An inventory planning system will help to identify and eliminate redundancies.
Obsolescence happens when items remain in inventory for long periods of time. Let's say that each time a new supply of an item comes in, it is placed on the front of the shelf and existing items are pushed to the back. The ones at the back of the shelf may never move off the shelf. Over time, as design improvements are made to the item, those at the back of the shelf become obsolete and unusable... or at best they must be sold at a discount.
Determining the economic order quantity is another aspect of inventory planning. This not only takes into account the costs associated with inventory, but also the costs of ordering and the possibilities of receiving a discount for a larger order. The economic order quantity overall minimizes the combination of both total inventory costs and ordering costs.
Another problem that can be addressed through inventory planning is variability in the supply chain. Certain items may come into your warehouse at unpredictable times and in various quantities, depending on supplier and transportation issues. At certain times of the year, you may want to plan for possible disruptions in supply due to weather. If there is a possibility of a strike disrupting the shipment of parts you need, you may want to plan your inventory to minimize that risk. This is all part of inventory planning.
Inventory Planning - Reasons for Maintaining a Large Inventory
Some of the advantages of having a large inventory include:
- Having the ability to quickly meet customer needs (resulting in satisfied customers).
- Having the ability to meet unexpected surges in demand (creating happy customers).
- Having a buffer against supplier problems or disruptions.
- Having a buffer against different production capabilities within your organization.
- Improved economies of scale. Buying in bulk can reduce costs.
- A larger inventory can increase delivery speed (resulting in grateful customers).
Inventory Planning - Reasons for Minimizing Inventory Levels
There are many disadvantages to having a large inventory. These include:
- Increased costs. Inventory itself has a cost, plus there is a cost to store it and maintain it in good condition. (Lower costs can make you more competitive.)
- Items may deteriorate, get soiled, decay, spoil, or be damaged. The longer an item is kept in inventory, the greater the risk. (Unusable items increase your costs.)
- Loses from inventory shrinkage (theft, items becoming lost, etc.)
- Items may become obsolete, or the market may change, such that the item is no longer needed or desired.
The disadvantages of increased inventory generally all lead to higher costs. This can result in the need to charge customers higher prices. Thus the benefits of maintaining a greater inventory are offset by higher costs. The positives vs. the higher costs must be weighed in each situation to determine the best inventory levels. That's what inventory planning does.
Inventory Planning and Lean Manufacturing
Lean manufacturing techniques such as Kanban strive to reduce inventories to as low a level as possible. The principle is called Just in Time (JIT) delivery. Raw materials and components are not delivered until just before they are needed, and finished products are manufactured in a sufficient quantity to meet customer demand. Ideally, these two, the incoming materials and outgoing products, should balance such that there is no inventory of either incoming material or outgoing products.
In practice, low levels of inventory are still needed, and very good inventory planning is needed to ensure what is needed is available when it is needed.
Related Resources
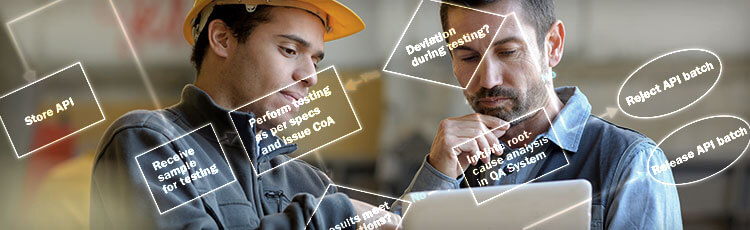
Visualize and Improve Workflows with Process Mapping
Why Map a Process? Maps and flowcharts help make work visible. Increased visibility improves communication ...
Read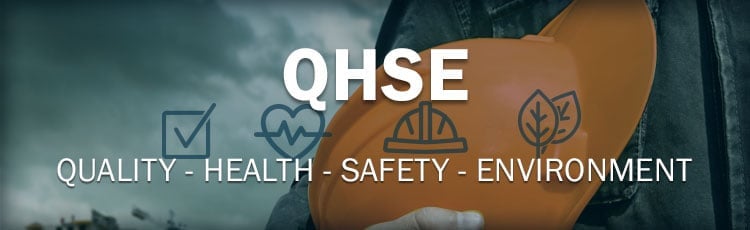
QHSE
Quality, Health, Safety and Environment Management (QHSE) generally refers to a management operation mode ...
Read
Cleanroom Safety Tools: Floor Tape, Signs, and 5S Systems
Why Floor Tape Is Essential in Cleanrooms Cleanrooms require significant investment—often between $250 and ...
Read