Lean on Maintenance
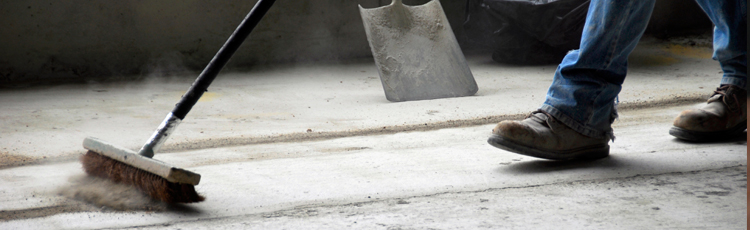
What is Lean Maintenance?
Lean manufacturing is arguably the single greatest advance in plant efficiency during the past 50 years. Lean has helped to systemize, organize and modernize big and small plants the world over. Further, re-engineering the stockroom is an excellent way to increase wrench time.
A custom blueprint for streamlining internal processes, Lean has helped to increase production at many plants. Except, all too often, these plants don't enjoy the maximum return on their investment. This is because managers often limit their Lean implementations to production-related processes.
Such applications provide only a fraction of the benefit Lean is designed to offer and often deprive plants of achieving the true potential for growth and development.
To be truly effective, managers must be willing to apply Lean to every plant process within each department. Of course, converting a department to a Lean process requires the support of all personnel and the dedication of leaders who recognize the benefits of working together in this endeavor. Once globally applied, Lean is known to influence the many routine actions of all employees so a plant can reach its true potential.
Perhaps the most overlooked department in a plant's Lean implementation is maintenance. In many cases, plants are notoriously production-focused and managers might view maintenance as somewhat peripheral. For this reason alone, plant professionals who haven't applied Lean to maintenance fail to recognize how much more Lean could do to improve their plant's efficiency.
In maintenance, the Lean process consists of simplifying routine duties involved in completing repairs. In other words, these processes usually begin with a need for materials that go into storage somewhere along the line. The steps between are all of the actions personnel take to complete an entire process.
To help streamline your maintenance department, group related actions into steps to help make the process as efficient as possible. This helps managers identify inefficiencies more clearly and allows them to customize Lean so it better fits the department it serves. Diagram the process steps to prepare for Lean implementation. This provides a clear picture of an overall process to make modifications more successful.
Lean Components
5S, Kanban and Kaizen are well-known efficiency-improving practices that are suited to support Lean implementations. A byproduct of post-WWII Japan, these practices have roots in both American and Japanese industry. Early inventors and innovators of these practices include the father of The Quality Movement, Dr. W. Edwards Deming and developer of the Toyota Production System, Shigeo Shingo. 5S, Kanban and Kaizen are often integrated as components of Lean implementations and used by plants around the world.
- 5S - a methodology for workplace housekeeping based on sorting, setting in order, cleaning, standardizing and sustaining the discipline
- Kanban - a visual signaling system based on cards, plastic markers, small balls or an empty bin or area of the floor that is used to trigger an efficiency improving action
- Kaizen - a philosophy promoting teamwork, the sharing of ideas and continuous improvement that eliminates waste
When properly applied, Lean maintenance plays a leading role in a plant's overall success. However, it must be tailored for the maintenance department it serves if it is to be truly effective. This means plant managers must be innovative about the processes they design and see the benefits of applying elements of Kanban and 5S wherever possible. Kaizen also should be applied consistently throughout a Lean maintenance implementation. This advances communication and fosters departmental teamwork. Applying the right combination of these techniques produces the greatest return on your Lean investment.
Managing Materials
One must be willing to think critically about the actions personnel take in handling materials. Inefficiencies can ripple throughout an entire plant, causing delays or even downtime. The goal is to streamline each action into one step so less time and energy is wasted.
Maintenance managers often are charged with purchasing parts and supplies for their departments. Inefficiencies here have far-reaching effects. Purchasers must ensure the right parts and tools either are on-hand or readily available. In Lean, this routine duty is treated as a critical element.
To avoid costly purchasing mistakes, maintenance managers should evaluate suppliers of goods and services. Managers should develop and follow a simple checklist of purchasing criteria. Generally, this list includes the minimum requirements for quality and price. Both are important, but rarely are they deciding factors in Lean maintenance.
The leading criterion in supplier selection usually is the additional services - the added value - a supplier offers with the sale. For example, predictable and reliable delivery always is an important service in a Lean maintenance process. If your plant is like most, maintenance parts and tools need to be delivered as soon as possible. Sometimes they even need to arrive the day they're ordered. When suppliers have proven they can deliver on their promises, price becomes less of an issue. Keep in mind that downtime is the enemy in Lean maintenance and relying on "penny smart" purchasing usually winds up being "pound foolish."
Suppliers who meet the established purchasing criteria should be added to a list of approved suppliers. As long as they continue to meet the criteria, make every effort to purchase from them. Over time, reliable suppliers become valuable assets. The additional services they provide might eventually include things like emergency deliveries, 24-hour technical support, discounts and other critical services that a plant comes to rely on. Either way, Lean maintenance departments benefit from lasting relationships with reliable suppliers.
After the purchased hardware arrives at the dock, the Lean maintenance process begins. Normally, maintenance materials are prioritized for immediate in-plant delivery upon receipt. Nothing is more frustrating than waiting for the tools or parts needed to complete a critical plant repair. Maintenance materials should be fast-tracked so in-plant deliveries are always made without delay.
Because receiving is the point at which most plants unload and separate materials by department, it makes sense to combine these and other related actions into a single step. Elements of Kanban and 5S can complement Lean implementations and are particularly useful in helping improve receiving. Many can be integrated directly into this step to streamline the rapid and error free delivery of materials in-plant.
Typical actions in receiving often include recording receipt of materials, notifying departments the material is in house and labeling materials for in-plant delivery. When these related actions can be completed in a single step, material destinations are never a mystery. The most efficient way to organize receiving is by communicating ownership by department visually.
Each item is clearly labeled so a maintenance technician can identify maintenance materials from a distance. Just like a well-organized filing cabinet, color-coded labels help employees find materials more quickly and with less effort. Integrating color-coded labels into a Kanban card labeling system (Figure 1) helps improve in-plant tracking, control and ultimate delivery.
Once the materials are delivered, the maintenance department should take immediate action to prevent critical tools or parts from sitting in limbo. A properly designed maintenance department won't experience the clutter arising from subsequent deliveries. Depending on a plant's size and layout, dedicated floor space near or in the maintenance area can be used for temporary storage of larger materials. These are commonly the large-quantity materials shipped by pallet or in multiple bins. Like the labels used to identify material ownership, these dedicated storage spaces should also be identified visually with a maintenance department's standardized color.
Just as at the dock, a maintenance department's receiving process should be a single step. Materials get sorted and stored, receipt gets documented and in-plant notifications provided. When done immediately, maintenance personnel never wait for parts or tools once they are in-house.
Storeroom Design
Maintenance storerooms require the same level of organization and efficiency as any other element in a Lean maintenance process. In fact, the storeroom should be viewed as the hub of the entire maintenance department and a critical step in the process. Where organized with easy-to-locate materials, maintenance departments work more efficiently and with less energy. To help make this as efficient as possible, stock the storeroom with an adequate, but lean inventory of materials. Using 5S strategies, design these locations efficiently so technicians always have easy access to the necessary materials.
Wherever possible, sort materials so routinely used tools and parts are stored up front, well organized and near related materials. This helps technicians find the materials they need more quickly and complete routine duties with less effort. As mentioned earlier, storage space can be provided for larger items in dedicated floor space and marked to show boundaries. Known as Kanban queues, these marked spaces should be outlined with color-coded, floor-marking tape to help distinguish departmental ownership. Kanban queues allow maintenance departments to store similar items in neat rows so quantity status is always apparent and shortages are less likely. When sorting, take time to determine the value of the materials being stored. A simple rating system can establish the value of each tool and part. Discard, sell or store off-site any obsolete tools, parts, or other low-value maintenance materials.
The clutter of obsolete materials impedes technicians from accessing the tools and parts they need. It also takes-up valuable storage space. Schedule periodic sorting to keep your storeroom lean and efficient.
Once organized and stocked only with necessary materials, make the storeroom easy to use. Storage containers (bins, closets, shelves, drawers, queues and the like) should communicate visually from a distance the materials they hold and any additional information. Use printed, industrial-grade labels to identify storage locations. These labels provide a sturdy canvas that clearly displays information about stored items so people can work more efficiently in these high-traffic locations.
Using color-coded labels in your storeroom maximizes label recognition rates. Your storage locations will not only be clearly labeled by name and specification, they'll be grouped by a color-coded category. As an example, a 3/8-16 x 6 inch bolt is going to be much easier to find when storage bins for bolts are labeled with the same color. Technicians can narrow searches by color first and then by specific materials they seek.
Provide more information on labels than merely part name, specification and category. Include everything from reorder points to maximum storage quantities on every label. This way, anyone in the maintenance department can easily reorder materials as soon as they run low.
Maintenance storerooms are not only high-traffic locations; they also can be a physical hazard. This means a storeroom's overall design, and not just how materials are stored, affects efficiency. Storerooms need to be large enough to provide space for technicians to retrieve the tools and parts they need without delay. Everything from additional lighting to reconfiguration might be required to better serve the department. OSHA provides many codes and standards that can help with proper storeroom design and safety. These are important guidelines to follow and can reduce injuries in the workplace.
A common storeroom hazard is improperly stored materials. When not easily accessible, they can cause back injuries. In fact, OSHA documented 420,000 workplace back injuries in 1999 alone. According to the survey, "Bending, followed by twisting and turning, were the more commonly cited movements that caused back injuries."
Check Out, Check In
Whenever material leaves the storeroom, maintenance should always be tracking its whereabouts and checking items in and out. This step in the Lean maintenance process should function much like a library. You want to know who is responsible for the return or restocking when tools or parts are taken from the storeroom. With the right tracking system, checking in and checking out can be made seamless, so it becomes a routine step in the process.
This is why maintenance departments should consider using technology to help implement a truly Lean process (Figure 2). Computer databases are, by far, the most efficient way to record material inventories and should, at the very least, be used to check materials in and out. Barcodes can be integrated into labels and Kanban cards (Figure 3) to provide unlimited information about individual materials. Departments also might find it beneficial to affix barcode labels to parts and tools to make checking in and checking out faster and more reliable.
In addition to a computerized database, publish a physical catalog of parts and tools. If the catalog shows the barcodes, technicians can hand-scan checkouts from color-coded and alphabetized lists of material. Barcodes can even be used to scan and automatically record each step in the Lean maintenance process, which simplifies reordering materials. Over time, maintenance departments should be encouraged to be creative with new technology. Innovative applications can improve efficiencies, thereby saving time and money.
Where used appropriately, technology teamed with Lean offers the greatest efficiencies and savings. As long as maintenance is recognized as a critical plant element, worthy of Lean, it will continue to offer very reliable support. Enjoy the benefits of 5S. Download our free 5S System guide below.
Related Resources
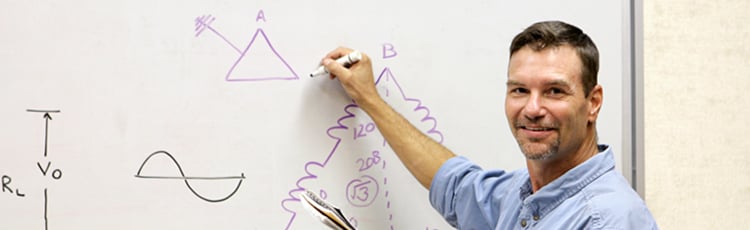
DFSS (Design For Six Sigma): A Customer Centered Process
What Is Design for Six Sigma and How Does It Improve Product Design? Design for Six Sigma (DFSS) is a ...
Read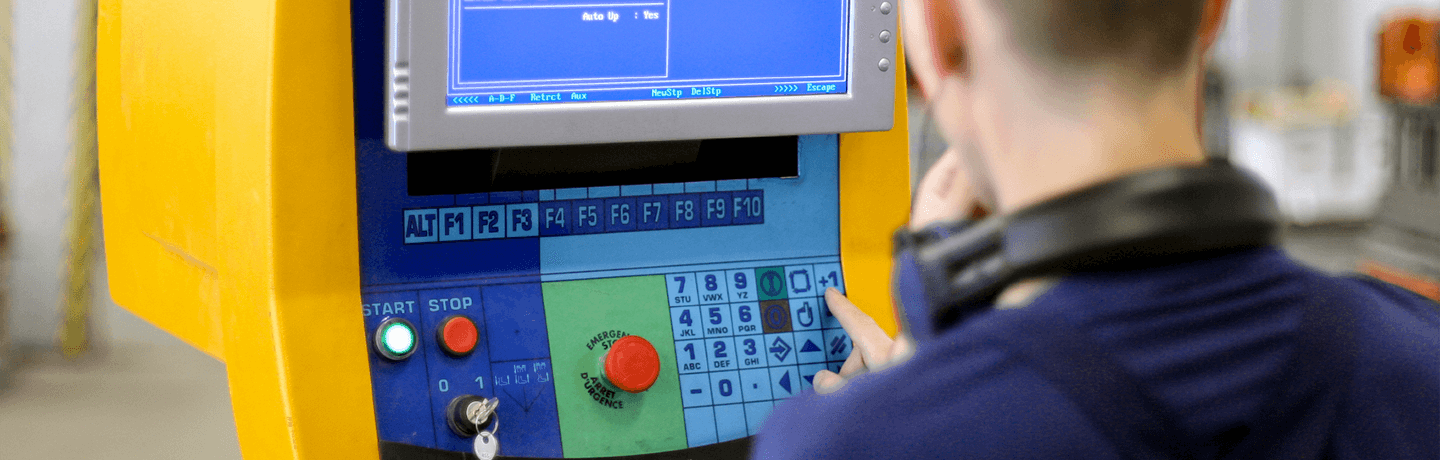
Six Sigma Principles: Exploring Six Sigma, Lean, and The 5S System
What is Six Sigma? Six Sigma is a systematic approach to eliminating errors that harmonizes with 5S and 5S ...
Read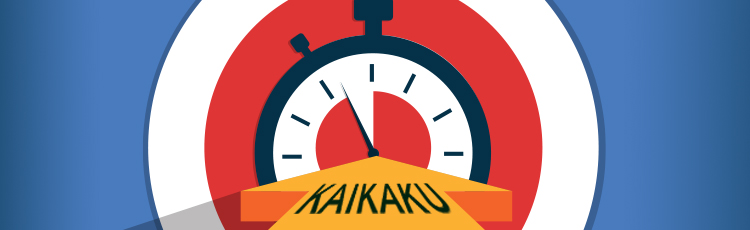
Kaikaku: Driving Radical Change in Lean Systems
What Is Kaikaku and How Does It Support Lean Transformation? Kaikaku is the Japanese word for "radical ...
Read