Periodic Inventory System
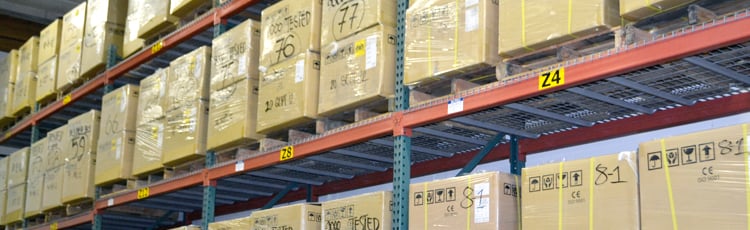
What is a Periodic Inventory System?
A periodic inventory system is an accounting method in which the cost of goods sold is determined periodically, usually annually and typically not more frequently than quarterly. This differs from a perpetual inventory system in which the cost of goods sold is determined as necessary or in some cases continually.
No effort is made to determine the cost of goods sold until an actual count of the inventory is completed. At that point the actual value of the inventory is known and the cost of goods sold can then be calculated using the formula:
- Beginning inventory + purchases ? ending inventory = cost of goods sold
In a periodic inventory system, companies record revenues from the sale of merchandise when sales are made, just as in the perpetual system. Unlike the perpetual system, however, companies do not attempt on the date of sale to record the cost of the merchandise sold. Instead they take a physical inventory count at the end of the period to determine:
- Cost of the merchandise then on hand and
- Cost of goods sold during the period
And, under a periodic system, companies record purchases of merchandise in the purchases account rather than the inventory account. Also, in a periodic system, purchase returns and allowances, purchase discounts, and freight costs on purchases are recorded in separate accounts.
Accounting for Purchases with the Periodic Inventory System
For accounting purposes, when using a periodic inventory system purchases are not added to inventory, but instead are added to an "assets" account. When a physical inventory is conducted the balance in the "assets" account is moved to the "inventory" account. For all practical purposes the "assets" account is an accumulation account. It accumulates the value of all purchases for an accounting period. Then it is completely emptied when the balance is transferred to the inventory account at the end of the accounting period.
An advantage of the periodic inventory system is that there is no need to have separate accounting for raw materials, work in progress, and finished goods inventory. All that is recorded are purchases. Only when the accounting period ends, and a physical inventory count is made, does the value of purchases need to be known. In some respects this simplifies the accounting system and helps to reduce inventory tracking costs.
LIFO
The most significant difficulty with a periodic inventory system is determining the value of inventory. The inventory accounting method most often used with a periodic inventory system is Last In/First Out (LIFO). Under LIFO it is assumed that the most recent purchases are the ones that are first used. The value of the ending inventory is based on the oldest costs for the materials still in inventory.
Periodic Inventory System Disadvantages
While the periodic inventory system works well for some types of businesses, in particular those with high sales volume, it does have some disadvantages. These include not knowing stock levels, a lack of detail, the potential for a loss of revenue, and not collecting useful sales information.
The periodic inventory system was created as a way to track inventory in businesses with high sales volume. Prior to computer technology, barcodes, and RFID tags, when everything had to be counted by hand, it was impractical to continuously track inventory in businesses where sales volume was high, and inventory turn-over was rapid. The periodic inventory system eliminated the need to continuously track inventory and instead used what was essentially a once-a-year "batch" system of inventory accounting.
Unknown Stock Levels
When using lean manufacturing methods it is important to know what is in stock at every point in the production process. Lean manufacturing often involves minimum inventory levels and the use of visual cues called Kanban cards to "pull" products through the production process. Kanaban facilitates just-in-time delivery of needed materials and supplies, with the need driven by customer demand. Planning for changes in demand, determining the optimum level of inventory, and optimizing production all require knowing current inventory levels, including knowing the level of work-in-progress.
Lack of Detail
When inventory levels are determined infrequently, often just once a year, there is the potential for errors and missed opportunities. For example, a once-a-year inventory results in a lack of detail that makes it difficult to spot and minimize factors that contribute to the cost of inventory, such as shipping, purchasing, and handling costs. On the opportunities side, because of the lack of detail, opportunities such as seasonal increases in demand many not be apparent.
Possible Revenue Losses
With the periodical inventory system it can be difficult to notice inventory shrinkage from theft, damage, or from items simply becoming misplaced (employee error). Losses resulting from defective product being exchanged can go unnoticed. Not knowing what is happening in the warehouse opens the door to variety of potential revenue losses that are difficult to spot without tracking current inventory levels, as well as knowing what is going in and out of inventory.
Not Collecting Valuable Information
Many of the disadvantages of the periodic inventory system result from a lack of information. With the availability of technology that makes tracking material flows simple and relatively inexpensive, information can be collected that helps to cut costs and identify business opportunities. Problems, such as a quality issue, can be spotted sooner and resolved before it impacts a large number of customers. Inventory shrinkage becomes easier to detect. And business opportunities, such as increased seasonal sales, become visible.
Using Kanban to Control Inventory
Kanban can be used as a lean method to help minimize inventory. Kanban is a system used to control production so that products are made and delivered when customers need them. When using Kanban raw materials are only ordered when they are needed, and product manufacturing is directly tied to customer purchases. The result, called Just In Time (JIT) delivery, is reduced costs and increased customer satisfaction.
If you're interested in learning more about Kanban, download our free Kanban Best Practices Guide for actionable advice on implementing Kanban for your organization. Get your copy below.
Related Resources
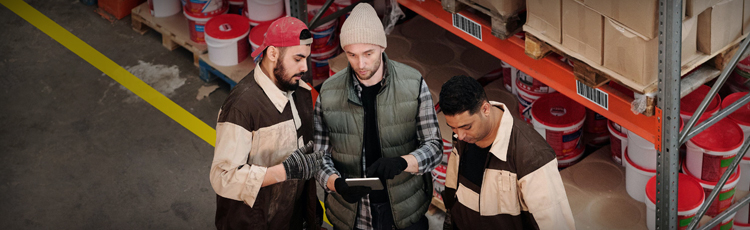
Inventory Management for Manufacturing 4.0
Industrial professionals need inventory management solutions that can handle the chaos of yesterday and the ...
Read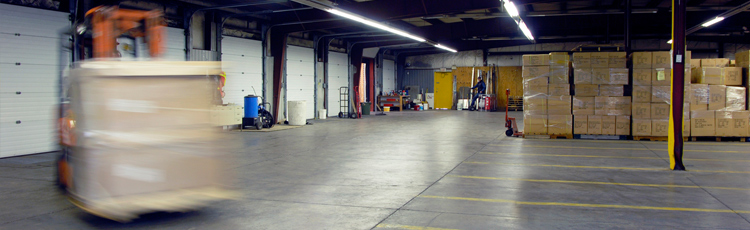
Cross-Docking
What is Cross-Docking? At its most basic, cross-docking establishes a speedy, efficient system for unloading ...
Read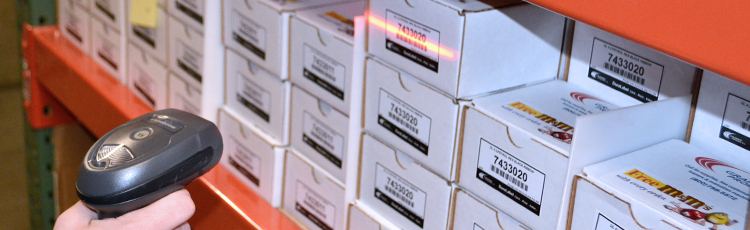
Asset Identification
For Want of a Nail Even when a small, low-value item is missing, it can result in major impact on your ...
Read