Planned Maintenance
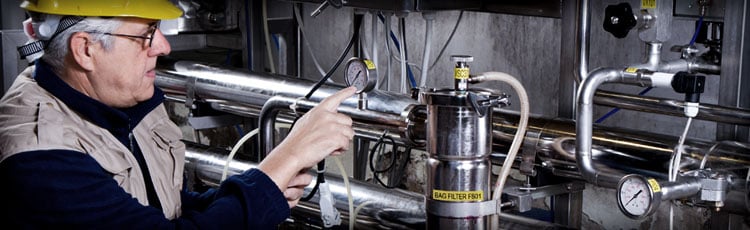
Planned maintenance is a proactive approach to maintenance in which maintenance work is scheduled to take place on a regular basis. The type of work to be done and the frequency varies based on the equipment being maintained, and the environment in which it is operating.
The primary objective of planned maintenance is to maximize equipment performance by keeping equipment running safely for as long as possible, without that equipment deteriorating or having unplanned outages.
Planned maintenance activities include any maintenance work scheduled in advance. For example, changing the oil in a vehicle because the oil light came on is not planned maintenance. Changing the oil because the vehicle had gone 3,000 miles would be planned maintenance. Planned Maintenance is a scheduled maintenance activity, or service visit, that is done to ensure that the equipment, or equipment components, are operating correctly and within the manufacturer's recommendations.
Planned maintenance includes preventive maintenance tasks such as checking oil levels, when those tasks are preplanned.
The schedule for planned maintenance tasks can be based on equipment running hours, number of items produced, distance traveled, or other measurable factors.
Planned Maintenance - Using Computer Systems
Since planned maintenance tasks are done on a regular schedule, they can be used to provide information to feed a computerized system that tracks maintenance needs, as well as being themselves scheduled using a computerized system. However, remember that a computer is only a place to save information and schedule tasks. It does not design your planned maintenance system nor determine how to get the work done.
Working with the production department, and at times a service representative from the manufacturer, equipment maintenance that needs to be regularly scheduled should to be identified and an appropriate schedule developed. A method for measuring the effectiveness of the planned maintenance work should also be designed so that the overall planned maintenance system, as well as the individual tasks, can be evaluated.
One of the key goals of planned maintenance is to ensure the equipment is in compliance with specifications and to proactively identify potential performance problems. The objective is to find and correct problems before they cause an unscheduled outage.
Major Benefits of Planned Maintenance
The key benefit of planned maintenance is that the work can be scheduled in ways such that it does not interfere with overall production. This may mean scheduling planned maintenance during times of the year when there is less demand, or doing maintenance at night when most of the facility is not operating.
Other direct benefits of planned maintenance include:
- Reduces unplanned equipment downtime and improves overall equipment performance
- Repair costs are reduced because problems are fixed while they are minor
- More efficient use of manpower and other resources because maintenance work, parts inventory, tools and financial costs, can be spread more evenly throughout the year.
- Better planning of spare parts use and ordering
- Helping to ensure the manufacturer's requirements for warranty compliance are met
- Reducing overall maintenance costs
There are also a number of secondary benefits that come from using planned maintenance. These include:
- Improved workplace safety
- Procedures are established to plan the use of, monitor, and control maintenance resources
- Improves the communication between maintenance and operations
- Provides a daily plan for maintenance supervisors such that employees have a full day of work every day
- Establishes a performance monitoring system that allows maintenance activities to be better evaluated and improved
Implementing a Planned Maintenance System
As with any other major change, a successful implementation of planned maintenance requires the agreement and participation of everyone affected by the timing and quality of maintenance. This includes the maintenance department, production, safety and possibly the instrument shop. In addition, support from upper level management is needed to ensure the necessary resources to get planned maintenance started are available.
Next get suggestions from, and listen to those who are working with the equipment. They'll be the most knowledgeable about its operation and its problems.
Consider making lean manufacturing techniques such as TPM (Total Productive Maintenance), Kaizen, and 5S part of your planned maintenance system.
Make safety a part of establishing a planned maintenance system. When evaluating equipment to determine the need for planned maintenance, also conduct a Job Hazard Analysis. This will reveal potential hazards that can occur during maintenance as well as bringing out safety issues that can develop during normal operations.
Department Responsibilities
While the production department will have a major voice in scheduling planned maintenance, and if TPM is being used equipment operators may perform some planned maintenance tasks, the bulk of the responsibility for planned maintenance work will fall on the maintenance department. In addition, in cases in which outside expertise is required, either manufacturer's field technicians or qualified third party service personnel will need to be a part of the planned maintenance schedule.
The maintenance department's responsibilities might include:
- Training supervisors so they have the necessary skills and knowledge
- Maintain a sufficient staffing level, without over-staffing, such that all planned maintenance can be accomplished. Train maintenance workers so they are competent to perform the required tasks.
- Ensure all work is done to the required specifications (including using appropriate fluids and replacement parts).
- Inform the purchasing department about planned maintenance needs with sufficient lead time to allow parts and supplies to be ordered on a normal basis.
- Track maintenance tasks, maintain records of the work that was done, and ensure work is done properly.
- Report on equipment problems noticed during planned maintenance so they can be addressed during turn-arounds or scheduled plant outages.
The above list is only intended to provide some ideas. The staff in each facility is organized differently, and there are different priorities. For example, part of the maintenance department's responsibility might be to minimize staffing through scheduling and judicious use of overtime.
The Role of Labels and Signs in Planned Maintenance
Signs and label play a crucial role in a successful planned maintenance system. For example, every lubrication point should be labeled to identify it and to identify the type of lubrication that should be used. Labels should be used to identify by part number locations where spare parts are used. And of course, labels and signs should be used to warn about hazards and provide safety information.
A versatile custom label printer, such as the DuraLabel PRO 300, is needed to meet the range of labeling and sign making requirements that can be encountered when implementing planned maintenance. But, more than that, a printer that has a wide range of supplies is needed. Having the ability to make calibration labels, oily surface labels, and tough-tested vinyl labels ? all with the same printer - eliminates hassles and helps you get the job done quicker.
View more information on DuraLabel printers and tough-tested supplies. They're the custom label printers that easily handle all of the above, and that get the job done right.
Making Planned Maintenance Work For You
Planned maintenance is one component of the greater 5s System which can help to optimize efficiency and production while reducing accident risk. Learn more about implementing 5s in your facility with our free 5s System Guide by downloading your copy below!
Related Resources
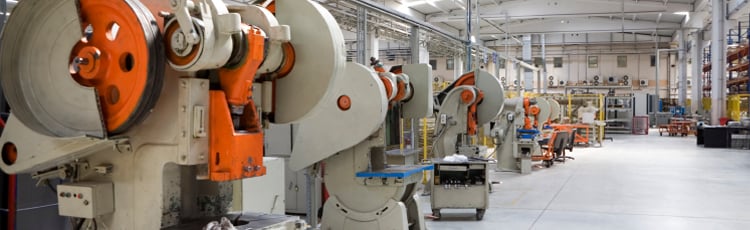
Lean Logistics Techniques
What Are Lean Logistics Techniques? Lean logistics techniqueshelp organizations streamline supply chain ...
Read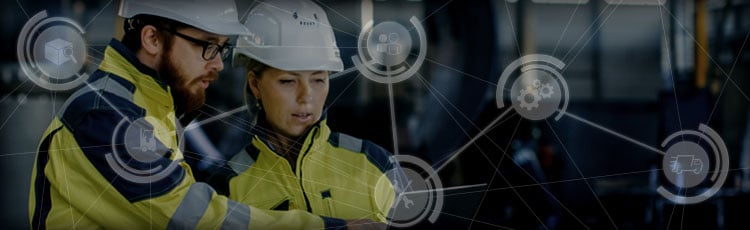
Logistics Tracking
Logistics involves managing the movement of resources. This not only includes products, but the movement and ...
Read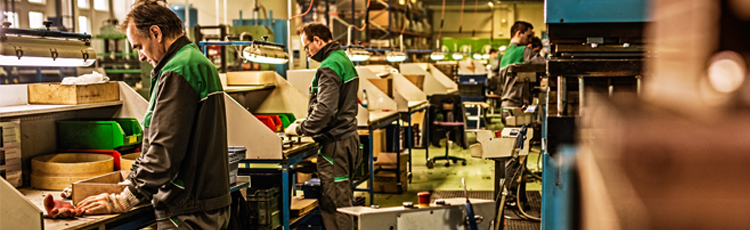
House of Lean: Building the Lean Manufacturing Framework
What Is the House of Lean? The House of Lean is a useful tool that can help you understand Lean Manufacturing ...
Read