Cleanroom Safety Tools: Floor Tape, Signs, and 5S Systems

Why Floor Tape Is Essential in Cleanrooms
Cleanrooms require significant investment—often between $250 and $1,500 per square foot—making every detail of safety and efficiency mission-critical. The cost of contamination, error, or downtime can escalate quickly, which is why facilities depend on cleanroom safety tools like labeling systems, signs, and floor tape for cleanrooms to stay compliant and productive.
By applying 5S in cleanroom safety, teams can reduce clutter, enhance visibility, and create reliable systems that minimize human error. These visual tools for safety support ISO and ESD standards while reinforcing critical zones, workflows, and hazard awareness throughout controlled environments.
Evaluate Worker Training
Prevent costly mistakes and ensure your facility has a comprehensive training program in place for all personnel who enter a cleanroom. Deficient safety awareness training causes employees to misunderstand protocol, make mistakes, ignore 5S floor tape, and cause potential problems. Make sure workers know why they need to follow specific procedures and how they connect to the overall goal of the operation. Consider these best practices to help aid worker training:
- Determine a consistent method of employee evaluation and testing.
- Discuss scenarios including corrective action when mistakes happen.
- Regularly assess gowning processes.
- Consider implementing various training tools that resonate with workers of different learning styles.
- Supply visual guides—like floor tape—near work areas, color-code important machine instructions and post easy-to-read graphics and checklists.
- Encourage employees to share suggestions for improvements.
- Offer refresher training when necessary.
Avoid Electrostatic Discharge with Tools like Floor Tape
The level of surface cleanliness and low humidity in a cleanroom encourages static charge generation. Static electricity can attract contaminants in cleanrooms and impact workplace safety, which is why electrostatic discharge (ESD) control is a big concern, especially in medical device manufacturing and microelectronics. Personnel are the main sources of static electricity from simply walking around, and this static charge can easily be discharged into an ESD-sensitive device. Equipment like carts and trolleys moving through the facility can also produce a static charge that can transfer to the products that are being transported on the equipment.
To identify problem areas, establish how ESD-sensitive the parts and assemblies you're manufacturing or handling are to determine the best control solution. Check with the manufacturer or supplier of the equipment or refer to the part data sheet to determine the ESD classification or voltage.
You can reduce electrostatic attraction (ESA) and control static discharge in sensitive areas like cleanrooms using the ESD floor marking tape. ESD floor tape won't absorb static, making it ideal for labeling electronic components and marking in cleanrooms. Post signs to identify ESD-sensitive items produce barcodes, hazard labels, general facility labels and signs, and more. Note: implementing a static-control program will be the best way to ensure the most effective static control.
Implement a 5S System
A 5S system can help correct inefficiencies and ensure operations run smoothly by keeping all items within the cleanroom clean, functional, and where they belong. Here are suggestions for how to implement each step of 5S in cleanrooms and other controlled environments:
Step 1: Sort
Remove all unnecessary items from the cleanroom. This will help eliminate clutter in the workspace, eliminating hazards that may have been lurking before.
Step 2: Set in Order
Make things easy to find using 5S floor tape. Assign equipment to specific locations so personnel know where to find and return items each time.
Step 3: Shine
Conduct basic maintenance duties. Make it a part of the daily routine to inspect, clean, and disinfect all surfaces—including floor marking tape—and instruments in the cleanroom to protect against contamination.
Step 4: Standardize
Consistently enforce the rules. Ensure all personnel understand the goals and steps of the 5S system to experience the true benefits within the facility.
Step 5: Sustain
Repeat all steps of 5S daily will ensure the workplace remains clean, safe, and efficient.
Install Thoughtful & Compliant Floor Tape
Installing floor tape makes it easier for personnel to navigate in the clean room. Designate workstations, safe aisles and pathways, storage areas, and more to enhance visibility, safety awareness, and organization in any facility. Ensure the 5S tape complies with the ISO cleanroom classification you need. It's also perfect for implementing a 5S system. Create a standardized color-coding system to differentiate between hazards and organizational areas and alert personnel to areas of various tools and equipment.
Outline and highlight areas to prevent damage to expensive equipment, such as ceiling-mounted HEPA filters. Alert personnel conducting maintenance activities to keep clear to avoid punctures and other damage. Mark the facility floor and other areas and surfaces such as walls, carts, shelves, and cabinets with durable floor marking tape. DuraLabel PathFinder LITE 5S Floor Marking Tape is rated for ISO 4 and below and meets federal specifications PPP-T-66E and CID A-A 1689.
These two federal specifications outline requirements for pressure-sensitive adhesive floor tape made for sealing out moisture, sealing interior packaging, and for use of identification, marking, or printing. You can ensure your labels are valid and remain durable using high-quality material. This 5S floor tape is ideal for floor marking applications in manufacturing facilities, laboratories, and other cleanroom-controlled environments.
Evaluate Safety Floor Signs and Labels
Floor signs and labels are essential to any workplace safety program. They help prevent unsafe behavior, draw attention to important information, and communicate hazards. Reduce chances of human error and ensure workplace safety by making sure labels and floor signs are in good condition by conducting a walk-through of the facility. Evaluate and replace worn, outdated, inaccurate, and damaged labels and signs.
Cleanroom Safety Floor Tape Solutions
5S floor marking is an important element for facility organization that provides workers with helpful visual aids. When creating a safe cleanroom, it's essential to use high-quality products. DuraLabel offers a wide selection of floor signs, tapes, and industrial label printers that are specifically designed to meet the demands of any cleanroom.
Take Action Today
DuraLabel® PathFinder® Floor Marking solutions not only enhance safety but also contribute to the overall efficiency and organization of your workspace. Take the next step in elevating your workplace safety standards, call us today at 1-888-695-5670. One of our safety experts will help you integrate 5S in cleanroom safety into your workflow using proven Lean strategies and DuraLabel industrial labeling tools.
Additionally, enjoy DuraLabel’s free Floor Marking Quick Start Guide. Create safe pathways for pedestrians and vehicular traffic and guide workers to the tools they need.
Read Next:
Related Resources
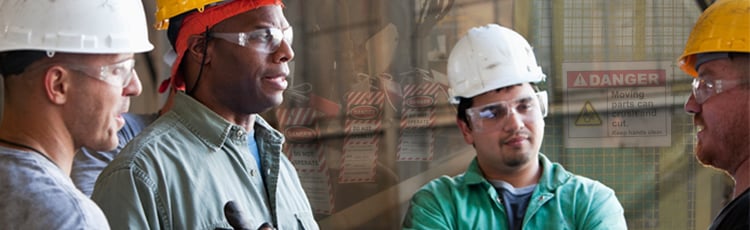
ALARP (As Low As Reasonably Possible)
What is ALARP? ALARP is the acronym for "As Low As Reasonably Possible," a principle primarily used in the ...
Read
5 Floor Marking Solutions That Improve OSHA Safety and 5S Organization
What is Floor Marking? Floor marking solutions use visual cues like tape or signs to enhance safety, ...
Read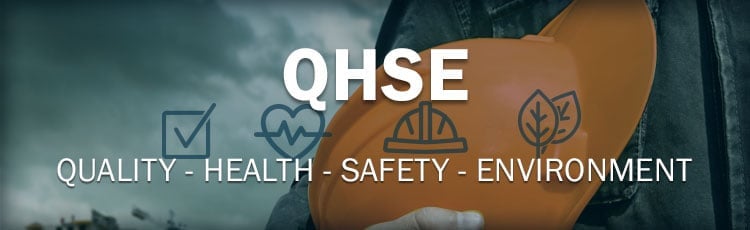
QHSE
Quality, Health, Safety and Environment Management (QHSE) generally refers to a management operation mode ...
Read