3 Ways to Reinforce Training and Improve Safety
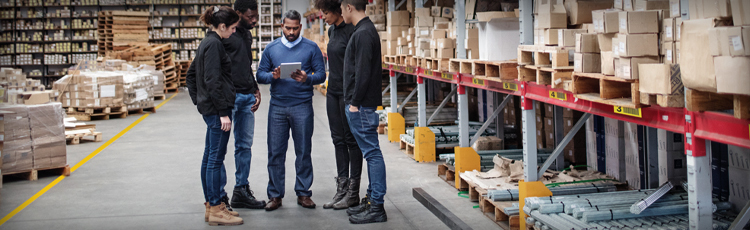
A construction worker in San Francisco died after being struck by a steel beam that fell 13 feet from a crane. OSHA investigators found that workers had no training to safely operate crane equipment, and no training on safety procedures for when the crane was in operation. Effectively evaluating and communicating jobsite hazards to workers and the measures they can take to prevent injuries is a challenge in many workplaces. There is a wider array of safety technologies and accessible training materials than ever before. As workplaces must be nimbler amid changes, training is important to keep workers a step ahead of hazards, safe, and efficient.
"Employers must identify and evaluate the particular hazards in their workplace and train employees on safe work practices to avoid injury, illness, or even death," said former Cal/OSHA Chief Juliann Sum after the struck-by death in San Francisco.
Effective Resources
Training employees should not be a one-time procedure. It should be a fundamental part of the organizational development process. Over time, employees may forget certain safety measures that they need to follow, which is why workplaces must implement periodic re-training sessions to keep employees up to speed. To prevent accidents and injuries, workers may need industry-specific training.
"During the hands-on part of the training, we work with equipment and explain what each label means. In the future, it will help avoid risk and can save a life," said Tom Whitehead, a spokesperson for Able Safety, a consulting and training service provider in New York. "Workplaces can satisfy the requirement for general and specialized courses for site safety training through a variety of online training courses."
Online training courses are one option for safety training and education, as are webinars and free resource downloads in the form of guides, infographics, and easy to share articles. Workplaces can find training requirements and resources through OSHA. The federal agency encourages a proactive, preventative approach toward safety, which can be difficult and time-consuming to manage without technology such as safety management software. This software allows for efficient tracking and standardization of safety activities.
When training seems like it is no longer having an impact, it is easy to switch up materials and methods. Researchers from the Center for Disease Control and Prevention (CDC) recently examined the impact of toolbox talks (10-15 minute instructional sessions) on workers' knowledge gain. The study found that including a narrative with discussion questions was better at increasing the overall knowledge gain than non-narrative toolbox talks.
Reinforce Training
Continuously educating workers is only part of the training process. Solid training will include a thorough workplace approach that starts from the top to secure workplace culture and an understanding of expectations. Here are three ways to hold worker attention, support, and sustain training regularly.
- Screen Workers: Take the time to interview candidates and talk about safety. Ensure they have what it takes to deliver quality work that will benefit the company.
- Signs and Labels: Place signs and labels throughout the office and workspace. This provides a simple solution to ensuring everyone who steps foot in there is safe. There are safety signs for almost every hazard, such as authorized personnel signs, caution signs, high voltage signs, and gas storage labels. Custom create messages that are unique to the facility.
- Invest in Tools: Keep employees safe by being fully equipped with the necessary tools, including personal protective equipment. For example, an electrical line crew in Arizona uses a video camera on its bucket lift for extra safety so that the supervisor down below can view the work from his phone. Put in place emergency equipment and call lines. Additionally, make sure tools, equipment, and vehicles receive regular maintenance, cleaning, and inspections.
Part of putting safety first in the workplace is ensuring preventative measures are set. Securing safety from the start increases productivity, improves satisfaction, and can help prevent any legal or compliance complications. Continuous training is a cost-effective and excellent preventative measure that pairs well with support systems such as 5S and total productive maintenance. Use signs, labels, and floor marking as part of safety upkeep and to remind workers of the steps they need to take to maintain their part of safety. These habits will decrease risks and improve the workplace overall.
Use checklists to maintain essential signage for facility safety and efficiency in our free Facility Visual Communication Checklist guide.
Related Resources
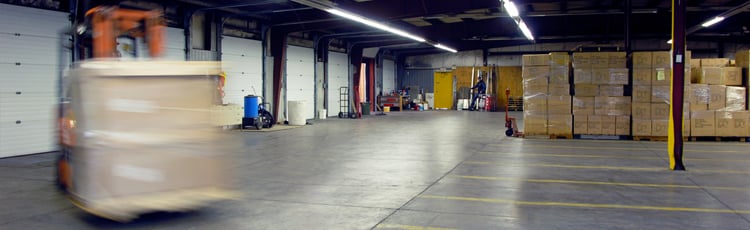
Easy Ways to Enhance Loading Dock Safety
Warehouses are busy work environments. Keep loading dock workers moving efficiently and safely using these ...
Read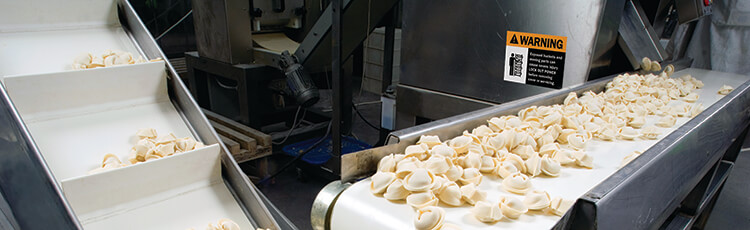
Efficiency and Safety Improvements in Food Manufacturing
Food manufacturing is continuously improving after a huge nudge from a year of disruption. How is food ...
Read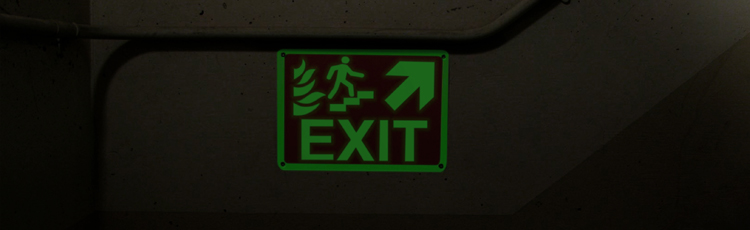
Your Safety Preparedness Can Help Others
When a disaster strikes, sometimes our failure to properly label even the simplest piece of equipment or ...
Read