Core Elements of Successful EHS Management
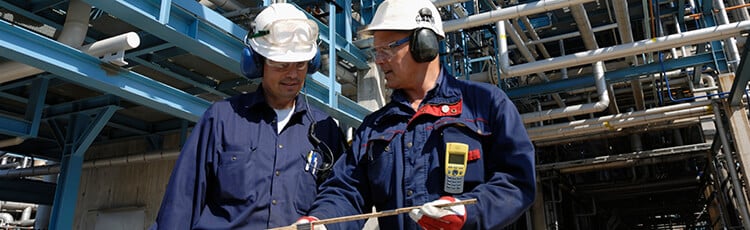
Workplaces know they need safety, and perhaps take it for granted that everyone will work safely, while workers assume management will protect them. How do workplaces know their safety management system is working to the full potential?
In the past year, compliance has been a top priority in navigating through the coronavirus pandemic and the various disruptions its created in industry. Safety professionals have been successful in following core elements of a basic program and crafting it to address their facility's unique challenges.
Changing Challenges
According to a recent poll of more than 200 industry professionals by safety expert Allen Woffard, most respondents said the top safety issues they focus on the most lately are personal protective equipment, permits or other documents, and upper management support.
"The response from that small group of hands was surprising," Woffard said. He addresses these findings in his popular podcast, "Dragging Up 6.0."
Priorities can pivot at any time, for any workplace, based on the unique needs of a facility or worksite. While workplace changes and challenges are common, there are core behaviors every safety program needs.
"I went from construction to labor to safety coordinator to safety engineer to safety manager over 40 years," said Jack Dayley of Spokane, Washington. "One of the reasons I became a safety manager is because I see things. [For example,] the guy with no safety glasses standing on an elevated platform next to a flimsy-looking barrier fence. I had to investigate five fatalities during my career, one in which I witnessed a good friend who was burned to death in a molten metal explosion. Each one of those fatalities strengthened my resolve to do everything I can to prevent another one from occurring. I'm 72 now and am still at it, still learning."
Strengthening Safety Programs
Each August, the Occupational Safety and Health Administration (OSHA) conducts its national Safe + Sound Week to encourage workplace health and safety program success. Some of the event's key focuses are:
- Proactive safety and health programs
- Ongoing finding and fixing of hazards
- Strengthening management leadership
- Boosting worker participation
Here are a few actionable items safety leaders can use to support and strengthen workplace safety programs from top to bottom.
- Be Productive: Following rules is great, but safety should extend beyond compliance. Meet workers' needs to ensure safety. The combination of safety and compliance is excellent for overall workplace efficiency.
- Boost Safety Culture: Create a positive work environment where workers feel comfortable speaking up about their well-being and work environment. Be constructive in addressing failures.
- Establish a Firm Foundation: Is safety everyone's job, or are there key people to go to? Keep a consistent process and make sure everyone knows their roles and expectations. Safety has to be supported by top-level management and on down the chain.
- Train Frequently: New employees are not the only ones who need training. Keep safety a fresh, daily topic for all workers. Use multiple media forms and safety best practice resources. Processes and protocol changes should be communicated.
Support all activities with consistent and clear communication, from training materials all the way down to floor marking and signs and labels. This ensures that everyone in the workplace knows what to do to maintain an expected level of safety and efficiency.
Related Resources

5 Easy Ways to Strengthen Bloodborne and Airborne Safety Management
Workplace exposure control plans are encompassing much more than in the past. How are workplaces mitigating ...
Read
5 Ways to Avert Common Bio Waste Violations
There are clear guidelines that health care and lab workers must follow when handling biohazardous waste. ...
Read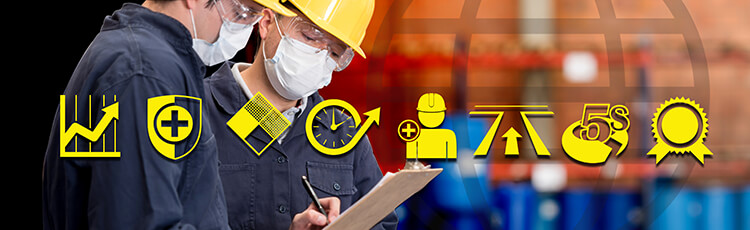
Safety and Health Program Management Guidelines
The Safety and Health Program Management Guidelines provide employers and workers with a sound, flexible ...
Read