Get a Grip on Better Cold Storage Material Handling
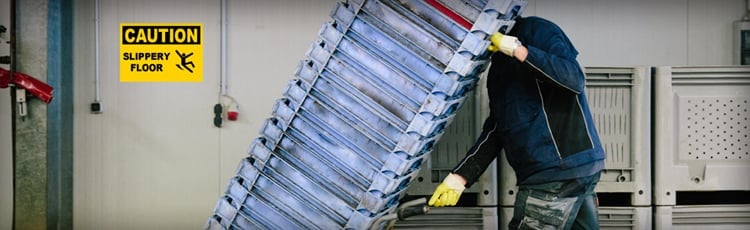
It may be warm and springlike on the outside, but on the inside, freezer warehouses throughout the world can be comparable to Antarctica. Though it is a fast-paced environment, staff work in unrelenting subzero temperatures. Even with the best gear, the cold pierces through, which means efficiency and safety must be meticulous. Quicker does not mean better in cold storage warehousing. The threshold of efficiency is built on thorough communication and precision, according to industry experts.
Demand is Hot
Cold storage material handling is one of the most demanding applications. Food and chemical companies use cold storage, and it even is seeing more demand as it is being utilized for the coronavirus pandemic vaccines. Cold storage demand is hot. Newer, grander, and more connected facilities are rising, and there seems to be no room for traditional warehouse operation methods. Lot tracking and communication need real-time visibility for inventory planning and management that only enterprise resource planning (ERP) can handle. ERP and automation are helping to move products in cold environments more efficiently by putting human power where it is needed most.
Food and chemical manufacturing companies require lot tracing to ensure they maintain forward and backward traceability for product recalls. This is crucial for routine quality checks as well.
"While cold storage facilities provide great value in economies of scale, it could be challenging to work with them if they don't have processes streamlined to support their customers' lot traceability and HACCP compliance goals," said Sam Gupta, a consultant with ElevatIQ, a company that provides business system procurement and implementation assistance. "The precision requirements and operational processes of cold storage facilities are of paramount importance. The training also plays a huge role. Suppose the facilities don't train their workers on the implications of mixing the lots. The results could be catastrophic, not only for the consumers but also for the manufacturing company's brand."
Modern refrigerated warehouse facilities have sleek engine rooms, advanced computer control systems, sophisticated warehouse management programs, new energy management systems, and efficient materials handling equipment. Yet, hazards still abound, and safety programs need to be routinely evaluated.
Mitigating Cold Storage Hazards
"It's negative 40 in the box and minus 10 on the dock," said Vince Blaine, an outbound shipping worker in a cold storage facility in California. Using forklifts and other material handling machines, he loads hundreds of pallets in a day. "As long as you have the right gear, you are good."
While the cold is likely the most serious discomfort for workers in freezer warehouse management, safety goes beyond cold stress. Other hazards include:
- Slips and Falls: Water and ice can create packs on the floor, which can pose slip, trip, and fall hazards.
- Chemical Storage and Leaks: Store and label chemicals following HazCom protocol. Keep the workplace SDS up to date and where workers can access the info. Immediately clean up spills. Leaks can cause asphyxiation hazards, especially in confined spaces.
- Fire and Emergency Plans: Anti-freeze doors and release mechanisms, fire ax, emergency exit plans. Ensure employees are monitored and that no one is trapped. Provide training to workers on emergency plans, policies, and exits.
- Forklift Traffic: Keep aisleways clear and clutter-free. Mark pallet storage areas as well as walking and working paths. Create machinery and equipment boundaries following OSHA's walking and working surfaces.
- Ergonomics: Contorting the body when stocking pallets, wrapping plastic, cleaning up glass, and more can cause sprains and strains. Use proper lifting and loading techniques.
- Personal Protective Equipment: Make sure freezer suits, high-vis, gloves, beanies, and other PPE items are adequate for the environment. Keep PPE in good condition and well organized.
Solutions and Communication
Although technologies have come a long way to help with end-to-end automation, business use cases such as lot tracking require precise alignment of physical and digital processes. Implementing physical strategies requires cold storage and freezer warehouses to select appropriate markers and visual cues. This helps both trained and untrained workers get enough feedback to operate without making catastrophic mistakes.
"Facilities need to maintain a proper level of control, which will help with audits and win contracts with larger customers who may require documented processes and SOPs around lot control, material tracking, and recall management," said Gupta.
Visual cues go beyond labels for inventory and tracking. Signs and floor marking that are durable in extreme environments, like DuraLabel, hold up and are effective for thorough facility communication. Use them for pallet jack parking areas and to direct workers to put equipment where it belongs for 5S and safety. Visual communication such as markings and signs helps keep establishing and enforcing any safety and lean management program. Re-examine and modify environmental health and safety solutions for employee safety management to raise the overall safety standard, while improving cold storage and freezer supply chain performance.
Related Resources
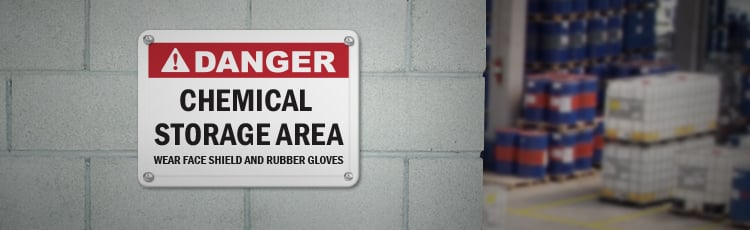
The Importance of Chemical Risk Assessments
Chemicals are in use in workplaces every day. It is important to follow and maintain chemical safety for ...
Read
GHS-Compliance: Safe and Effective Storage of Hazardous Chemicals
The Importance of the GHS When working with and storing hazardous chemicals, steps must be taken to ensure ...
Read
Tips for Better Chemical Safety Management
Workplace chemical safety is all about understanding the risks and following proper protocol. Train and ...
Read