Want to Save Money? Invest in Workplace Safety
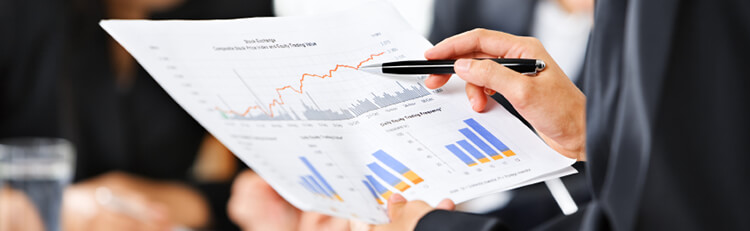
Tons of businesses are looking for ways to run lean and cut costs amid an uncertain and disruptive coronavirus pandemic. A key element in good, lean business management is safety. It's the 6th S in the popular and ever-relevant 5S method. Cutting safety can cost billions, and saving money doesn't mean cutting quality. By making safety a priority, workplaces can save money and strengthen overall efficiency.
Essential Expenses
Safety isn't a frivolous expense or a "nice to have." Lax safety creates opportunities for serious workplace accidents. Each year, the number of workplace injuries and deaths increases. In 2019, there were 5,333 work-related deaths, an increase of 2 percent, according to the Bureau of Labor Statistics. In its 2021 report based on 2018 data, insurance giant Liberty Mutual found that the 10 causes of work accidents cost employers about $58 billion in medical costs and lost wages. This does not include the indirect costs to the company in the form of disruption, attorney fees, insurance costs, and other negative financial impacts.
"Understanding the top risks in the workplace is the first step in better-protecting employees and the bottom line," said risk control services manager Jamie Merendino of Liberty Mutual. "The Liberty Mutual Workplace Safety Index gives companies a critical starting point, letting them partner with insurers, brokers, and agents to understand what causes their most serious injuries and what can be done to improve workplace safety."
Identifying the causes of workplace accidents is one way to prevent them. That way, employers can evaluate their facility, workers, and tasks to see where to improve. According to the Liberty Mutual report, the top affected industries are construction, manufacturing, healthcare, and retail, and the top five causes of costly workplace accidents in those industries are:
- Overexertion while handling objects, costing about $13 billion
- Falls onto the same level, $10.5B
- Falls to a lower level, $6B
- Struck by objects or equipment, $5.5
- Body exertion/poor ergonomics, $4.5
Necessary Next Steps
Safety and health managers can take these top five causes for accidents and evaluate how and when they could happen in the workplace. Identifying problems and not having a plan with adequate solutions is a sure way to fail employees and the business. The efficient approach to problem-solving is through a job hazard analysis. Once the JHA is complete, discuss the findings with workers so they can understand new safe work procedures or new equipment, including PPE.
Training workers on potential hazards on a routine basis can help prevent accidents and strengthen workplace culture. Reinforce safety and a diligent workplace culture with visual communication that stands out and relays vital messages. For example, post signs for weight limits and PPE information on raised equipment and platforms where workers might conduct maintenance. Highlight ledges and edges to help workers watch their steps when working from heights.
Workers that feel like they are making a difference and work where they are generally feel cared for are more likely to stay and help recruit future workers. The easiest ways to help ensure safety are frequent evaluations, important visual communication, and routine training.
Related Resources
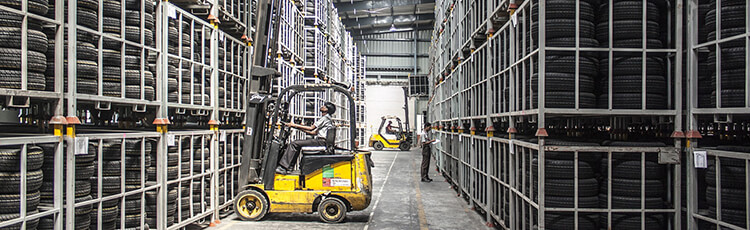
Safety Tips to Drive Down Work Traffic Injuries
The Drive Safely Work Week and Distracted Driving Awareness Month campaigns serve as reminders for workplaces ...
Read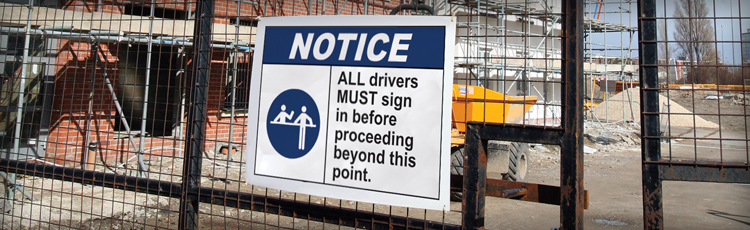
Improve Falling Objects, Struck-Bys in Construction
Falling objects and struck-bys are some of the most common job hazards that lead to injury or death in ...
Read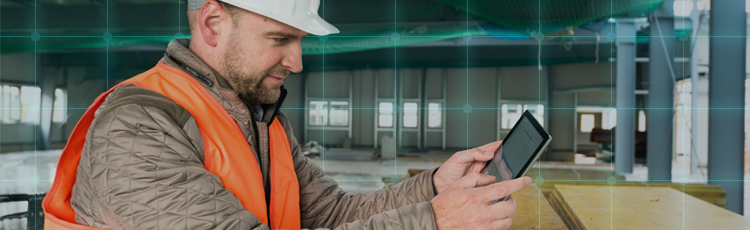
Ways to Improve Construction Site Safety
The term "time is money" is quite literal in the construction industry. The constant pressure project ...
Read