Electrical Safety with Lockout/Tagout
Webinar | Electrical Safety with Lockout/Tagout
Electrical Safety with Lockout/Tagout
Protect against electrical hazards with LO/TO
- Create lockout/tagout procedures for your specific equipment
- Reduce risks using the Hierarchy of Controls approach
- Understand essential OSHA and NFPA safety training requirements
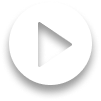
Presented By
Brian McFadden
Technical Writer
Compliance Specialist
Related Resources
Transcript
Webinar Preview
Contents of the Electrical Safety with Lockout/Tagout Webinar:
- Hazards of Electrical Work
- The Hierarchy of Controls
- Using the Hierarchy
- Lockout/Tagout for Safe Electrical Work
- Creating LO/TO Procedures
- LO/TO Training
- Equipment Requirements
- Periodic Review
- Administrative Controls for Hot Work
- Protective Boundaries
- Permits for Oversight and Accountability
- Additional Controls
- Moving Forward
Excerpt from the Electrical Safety with Lockout/Tagout Webinar transcript:
Safety is Key
Where the installation, service, or maintenance of electrical equipment poses a hazard to the worker, steps must be taken to ensure safety. It's required by law, it's recommended by experts, and it's the right thing to do.
But these situations can be complex. Multiple systems may be interconnected, and several different hazards may be involved.
Hazards of Electrical Work
Direct exposure to current - that is, electricity moving through a person's body - causes injury as electric shock, typically resulting in nerve damage. Worse cases can even end in death (that is, electrocution). If an object carries a stronger current than it was designed for, the object can become dangerously hot; this can result in burns for the worker who touches the object, and is especially bad when the worker's body is the object carrying the current.
If current can jump through the air in an arc, this can ionize the air along that path. Ionized air offers less resistance, so the arc can draw more and more power, "running away" to become an arc flash in a fraction of a second. An arc flash releases a sudden, powerful burst of heat and light, acting almost like an electrical explosion. Burns are the most typical injuries, but the blast of pressure can also result in impact injuries, and the extreme heat can vaporize components, creating a toxic cloud.
Electrical hazards aren't the only ones that can be involved in work on electrical equipment. Motors and MCCs directly affect the movement of parts, and those moving parts can pose hazards of their own. Pumps and compressors will be connected to pneumatic or hydraulic systems, which in turn can pose hazards through stored pressure. While electrical injuries can be serious, they're not the only hazards to consider.
Experts Weigh In
With the variety of hazards, and the unpredictability of accidents, planning for safe electrical work can be a complicated issue.
OSHA has a variety of mandatory safety procedures for electrical work, mostly found in 29 CFR 1910.333. There are also separate rules for dealing with hazardous energy in general, which are in 1910.147. More detailed, but non-mandatory, recommendations come from industry experts at the National Fire Protection Association (NFPA), in the NFPA 70E standard for electrical safety in the workplace.
The NFPA 70E standard is not intended to replace OSHA's regulations, but to provide a framework for safety that can be clearly detailed and easily updated.
Approaches for Safety
While these requirements and recommendations can get confusing, both OSHA's rules and the NFPA's standard use a single, simple idea as the core of their safety systems: Lockout/tagout.
In a survey of arc flash injury victims, 94% of those interviewed believed that the incident could have been prevented. Of all the different ways of preventing those incidents, the most frequently-mentioned method was simply to "turn the power off."
That may seem simplistic, and it is, but that's the idea at the heart of lockout/tagout: turn the power off, and keep it off until the work is done. It's also the core of what the NFPA calls an "electrically safe work condition."
Generally speaking, NFPA 70E requires an electrically safe work condition in either of these situations:
. An employee works within the Limited Approach Boundary, a clearance area around equipment designed to prevent unqualified workers from being exposed to a hazard of electric shock
. A worker faces an increased risk of injury from arc flash, as a result of the nature of their work or the equipment being worked on
In these cases, work generally should be done with the equipment in a de-energized state: shut down and locked out. Where lockout/tagout and an electrically safe work condition are not feasible, the OSHA rules and NFPA standard describe alternative practices for working on energized equipment. This "hot" work requires other safety precautions.
In almost all cases, leaving the equipment powered during work is faster and more convenient, while working on de-energized equipment is safer. Since both OSHA and the NFPA focus on safety, the safer approach (using lockout/tagout) is the default choice. Today, we'll cover that approach in detail, and then discuss the alternative rules for hot work.
Lockout/Tagout Done Right
Essentially, lockout/tagout means turning off equipment, disconnecting its power supply, and locking the power supply in a disconnected state so it can't be re-connected until work is done. In practice, though, it's much more involved than that.
Lockout/tagout done wrong can be dangerous and expensive. Failure to follow OSHA's locout/tagout requirements is one of the top ten most cited violations each year. OSHA also estimates that failure to implement lockout/tagout effectively causes "nearly 10 percent of the serious accidents in many industries."
Making lockout/tagout work for you will involve creating a lockout/tagout program for your facility. There are four basic steps to creating an effective lockout/tagout program:
. Create a step-by-step plan for each piece of equipment,
. Train your workers to understand those plans,
. Provide the tools to get the job done,
. And follow up with routine check-ups and revisions.
To learn the Hierarchy of Controls to address electrical hazards, and practical advice on safety with an effective lockout tagout program, watch the full webinar on demand now!
Related Resources
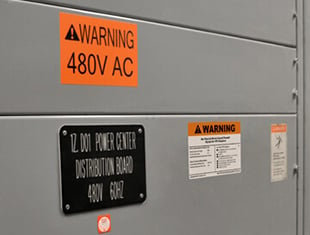
Labeling for Arc Flash Hazards
Presented By Brian McFadden Technical Writer Compliance Specialist Related Resources Arc Flash Labels Arc ...
Watch Now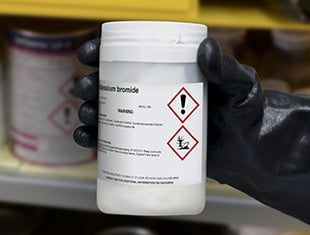
Chemical Risk Assessments
Presented By Brian McFadden Technical Writer Compliance Specialist Related Resources Risk Management ...
Watch Now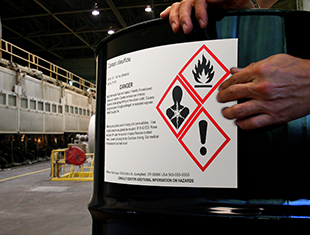
GHS & HazCom for Chemical Safety
Presented By Brian McFadden Technical Writer Compliance Specialist Related Resources GHS Labeling Changes ...
Watch Now