4 Ways to Eliminate Noise Hazards in the Workplace
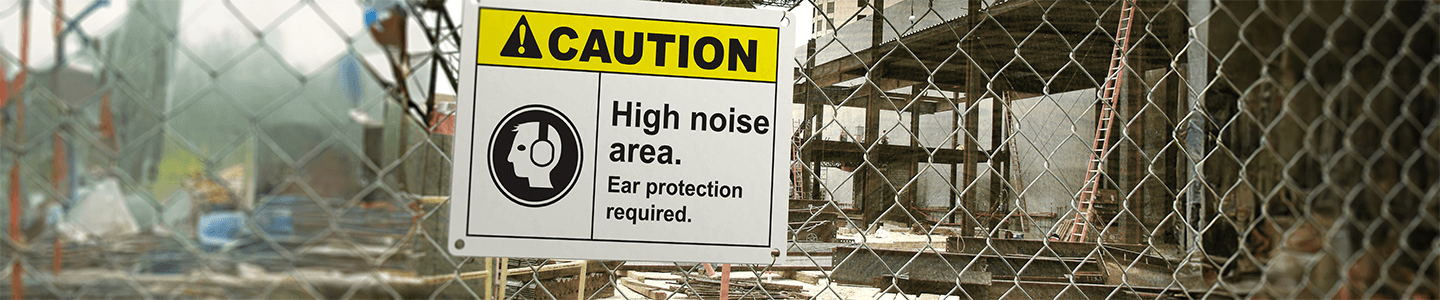
Occupational noise hazards rank among the most common workplace safety concerns. Our hearing is sensitive, and even moderate noise levels can lead to temporary or permanent impairment. Whether in an airport terminal or on a demolition site, it’s essential to implement measures that protect worker's hearing. Identifying potential noise hazards begins with understanding when noise becomes a threat.
When is Noise a Hazard?
Noise becomes hazardous when it interferes with communication, masks warning signals, or leads to chronic health problems. Hazardous noise levels are those exceeding 85 decibels (dB) over an eight-hour shift. For context, consider the following examples:
- 10dB: Rustling leaves
- 50-60 dB: Normal conversation
- 110 dB: a chainsaw or drill
- 140 dB: while a jet engine
How to Identify Noise Hazards
1. Observe existing signage: Check for safety signs indicating known noise hazards and required personal protective equipment ( PPE). Ensure that signage reflects current conditions, especially if machinery has been relocated.
2. Conduct arm's length test: The fastest and easiest way to test if there is a potential noise hazard in a specific area of a job site is to have workers stand at an arm’s length from each other and have a conversation. If one worker must raise their voice or the other has a difficult time hearing, the noise level likely exceeds safe limits.
3. Monitor for post-shift symptoms: Ringing in the ears, difficulty hearing, or a sensation of lingering machine noise after leaving work may indicate temporary hearing damage. You should report this to your supervisor immediately.
4. Assess related health issues: Overexposure to occupational noise hazards can cause serious health issues. These include decreased coordination and concentration, sleep disturbances, fatigue, increased stress, and nervousness. Workers experiencing these symptoms due to noisy working conditions should report these health conditions to your supervisor.
To manage occupational noise hazard effectively, workplaces implement two primary control methods: administrative and engineering controls. These strategies either limit worker exposure or reduce noise at the source, improving overall safety and compliance.
Administrative controls: Changes that reduce or eliminate worker exposure, such as:
- Adjusting work schedules to limit exposure time
- Rotating job assignments
- Implementing quiet zones in high-noise areas
Engineering controls: Modifications to the facility that lower sound levels, including:
- Installing sound barriers or enclosures
- Upgrading machinery to quieter models
- Using vibration-dampening materials
How to Eliminate Noise Hazards
- Lubricating machinery with metal-on-metal contact to minimize friction and noise
- Conducting preventive maintenance to extend equipment life and reduce downtime
- Inspecting machinery regularly to identify potential noise sources before they
escalate
2. Limit exposure time: Restricting worker exposure to noise hazards is an administrative control that reduces the risk of hearing damage, according to the American Industrial Hygiene Association (AIHA). This strategy may serve as an alternative to implementing a formal hearing conservation program. Limiting shift durations in high-noise environments, rotating job assignments, and scheduling mandatory breaks away from noisy areas are ways to manage noise exposure. will tell you, the costs associated with the time spent managing noise hazards will always outweigh the costs of attempting to fix worker's hearing.
3. Enclose or isolate the noise: A combination of engineering solutions and strategic workplace design can reduce or eliminate noise hazards. When possible, relocating non-human-operated machines to less populated areas can help reduce worker exposure. If moving the machinery is not an option, constructing enclosure around noisy machines can contain sound. For machines requiring human operators, an enclosure with an entrance can be constructed and proper PPE provided. Working in these enclosures may require a shorter shift, if the sound produced inside the enclosure becomes unsafe.
4. Use PPE properly: PPE serves as a last line of defense when noise cannot be eliminated at the source. It does not address the problem at the source but acts as a last line of defense for your ears. Proper PPE to protect hearing includes earplugs and earmuffs, often worn together. PPE should be used either in response to low level noise hazards or as a temporary solution until the source of the noise can be controlled or modified.
DuraLabel Hazardous Noise Solutions
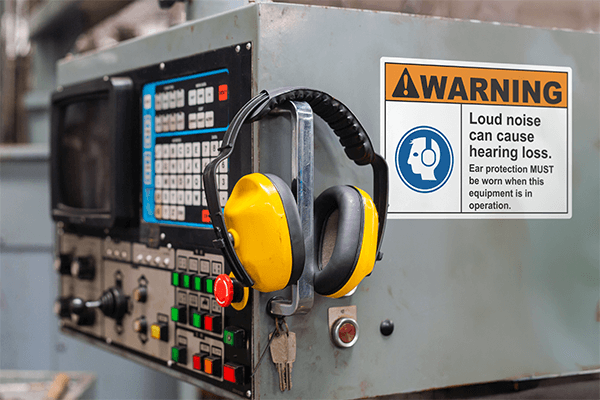
Effective noise hazard management reduces workplace risks and ensures regulatory compliance. Maintaining equipment, controlling exposure, and implementing engineering solutions create a safer work environment. Managing noise hazards requires a combination of maintenance, administrative controls, and engineering solutions to reduce exposure and maintain compliance.
Clear signage enhances these efforts by reinforcing noise hazard awareness and compliance. DuraLabel’s OSHA-compliant labels and signs mark high-noise areas, designate hearing protection zones, and communicate essential safety measures.
Need a handy reference? Understanding and implementing noise hazard controls is essential for workplace safety. DuraLabel’s free OSHA Signage Quick Start Guide provides the knowledge needed to create clear, compliant signage that improves hazard communication and reinforces safety protocols. Download your free guide today.
Want to learn more what areas of your facility could use some labeling? Download our free Facility Signage Handbook to help identify potential hazards and improve workflow.
Read Next:
Boosting Workplace Efficiency with Clear, Strategic Labeling
Visual Communication: Critical for Safety and Efficiency in Manufacturing
Related Resources
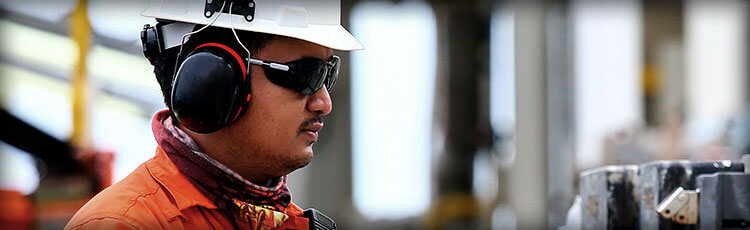
OSHA Sound Levels
What is noise? Is all noise bad? Where does noise come from? Vibrations detected by the human ear are called ...
Read
October is National Protect Your Hearing Month
Hearing loss happens slowly through years of exposure to loud noises. Here are some ways to help prevent ...
Read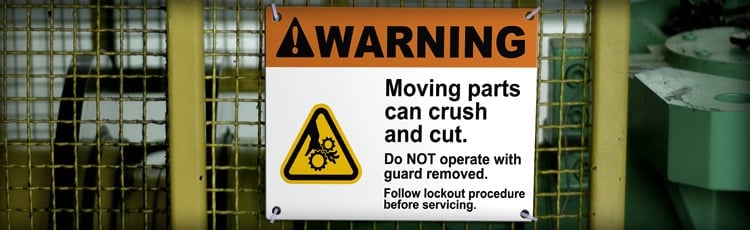
Hierarchy of Hazard Control
The hierarchy of hazard control has five levels, with those at the top of the list being the most effective. ...
Read