8D Methodology
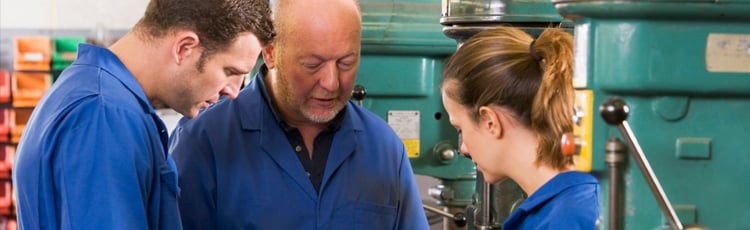
The 8D methodology (8D=eight disciplines) was developed in Ford Motor Company in the mid-1980s to be used by their suppliers to improve the resolution of problems. It appears in a variety of forms used to define eight disciplines. Sometimes it is defined as a nine-step problem-solving process.
Because the 8D model is designed to solve specific problems that arise, more emphasis is placed on containing the problem (discipline 3) than in most other frameworks. The idea is to implement intermediate actions that will protect the customer from the problem until a permanent solution can be developed and implemented.
The Eight Steps of the 8D Methodology
The 8D Methodology was originally composed of eight "disciplines" or steps. In the 1980's Ford added a ninth discipline, planning, but the name "8D" was retained. The disciplines are:
- D0 Plan
- D1 Put Together A Team
- D2 Define the Problem
- D3 Implement a Temporary Fix
- D4 Identify Root Causes and Chose a Solution
- D5 Confirm The Solution Resolves The Problem
- D6 Fully Implement the Solution
- D7 Prevent Recurrence
- D8 Recognize the Team
The 8D Methodology is based on the PDCA Cycle (Plan, Do, Check, Act). Each step in PDCA roughly corresponds to two steps in 8D Methodology:
- Plan Define a problem and hypothesize possible causes and solutions (8D steps D0-D2).
- Do Implement a solution (8D steps D3-D4).
- Check Evaluate the results (8D steps D5-D6).
- Act Either return to the planning step, or standardize the solution, depending on the results (8D steps D7-D8).
How Does the 8D Methodology Work?
The strength of the 8D Methodology is its ability to identify, correct, and permanently eliminate recurring problems in an ongoing system, by applying a quick fix and then addressing the root cause of the problem.
D0 Plan
The 8D Methodology often starts with a customer complaint about a problem with a product. In some cases a problem may be identified by management, or production workers. However the problem is first identified, the first step is to establish an initial plan. The plan includes a report on the problem, with an initial evaluation of its scope. This plan forms the basis for defining a team, identifying needed resources, and establishing a schedule for resolution.
D1 Put Together a Team
The team should be multidisciplinary, and include expertise in the product, process, or equipment being investigated. In the case of a problem with a product, understanding the customer's needs is critical, and having a representative from marketing or even a customer on the team is helpful. When processes and staff need to shift, it may be helpful to have an HR representative on the team.
The team's first task will be to write a purpose statement. This written document defines why the team exists, and what it is supposed to do. Having the team discuss this and create the document in their first meeting helps to get everyone on the same page.
D2 Define the Problem
What, specifically, is going wrong? The problem needs to be defined using quantifiable terms. The customer's complaint may be, "This product doesn't work!" How is it not working? Defining the problem may require establishing test methods and collecting data, interviewing customers, or talking with the workers who are involved with making the product.
"Gemba" is an important principle to apply when defining the problem. Gemba means to go to the physical location where the problem is - the real place - and look for yourself. The objective is to get first-hand information.
At this point, the team is not looking for the cause of the problem, or "where it comes from;" instead, they are collecting as much information as possible to determine the characteristics of the problem, or "what it is."
D3 Implement a Temporary Fix
If the problem is affecting customers, impacting productivity or costs, or is creating an injury, health, or environmental hazard, it needs to be addressed immediately. A temporary fix should be identified, evaluated, and implemented. These fixes may involve reworking the product, adding additional quality checks, or inspecting and sorting incoming parts from your suppliers.
If no temporary fix is feasible, it will be necessary to stop shipping the project or to shut down the process that has the problem.
Do not implement a temporary fix without an evaluation. The team needs to be sure the temporary fix is safe, will truly address the current problem, and is easy and cost effective to implement - without causing new problems of its own.
D4 Identify Root Causes
With the temporary fix in place, the next step is to identify the root cause of the problem. The overall goal of the 8D Methodology is to permanently eliminate the problem. That can only be done if the root cause is identified and eliminated.
Techniques such as the "Five Whys" can be used to identify the root cause. This approach involves asking the question "Why?" over and over (often five times) until the root cause is revealed. Other methods, such as fish-bone diagrams, Parento Analysis, or Fault Tree Analysis are also available to help identify the root cause. However the root cause is identified, the team should then decide how to eliminate it.
D5 Confirm the Solution Resolves The Problem
One of the best ways to test a solution is to implement it in a small way, and monitor what happens. For example, if a manufacturing process involves a number of cells, the solution can be implemented in one cell and the results monitored. If it is successful in the one cell, it can then be implemented in all cells. If the solution cannot be tested in a small way, then techniques such as Failure Mode and Effect Analysis can be used to analyze proposed changes to a system or product.
The team needs to be careful to ensure they have not missed something. Conducting a Blind Spot Analysis can be useful for identifying things that have been overlooked. Look for unintended consequences and negative side-effects that may result from implementing the solution.
D6 Fully Implement the Solution
Once the solution has been verified - it will eliminate the root cause without starting new problems - it can be fully implemented by making permanent changes.
D7 Prevent Recurrence
Once changes have been made, steps need to be taken to ensure those changes remain in effect, and that any new procedures continue to be followed. This usually involves incorporating the changes in written standards. Training may be required to bring people up to speed on new methods, procedures, and standards.
D8 Recognize the Team
Recognizing the accomplishments of the team is the final step. It can be a simple "thank you," but it should be done in a way such that others in your organization hear about what has been done. A common way to say thank you is with an article in the company newsletter, or with a poster placed on bulletin boards throughout the facility. Be sure that everyone on the team is named so that everyone is recognized for being a part of the team.
Related Resources
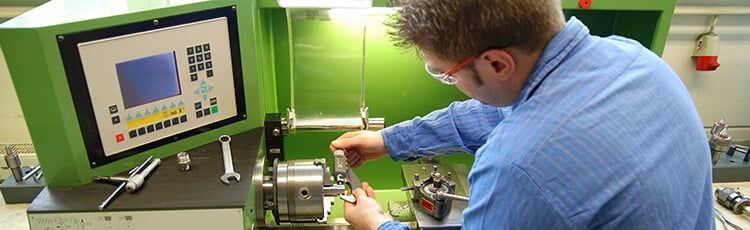
DMADV Methodology: Design for Six Sigma Explained
What Is DMADV and How Does It Guide Process Design in Six Sigma? TheDMADV methodologyis a structured approach ...
Read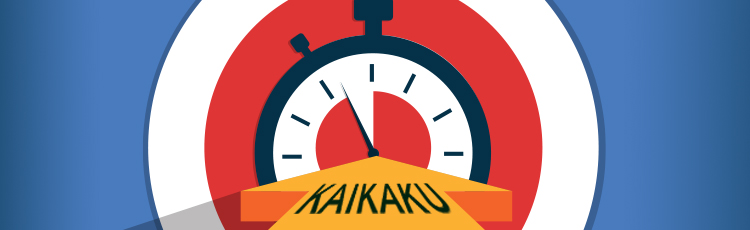
Kaikaku: Driving Radical Change in Lean Systems
What Is Kaikaku and How Does It Support Lean Transformation? Kaikaku is the Japanese word for "radical ...
ReadSix Sigma Methodology
As the name implies, a Lean Six Sigma methodology combines the principles of lean manufacturing ("Lean") with ...
Read