BS5609 Compliance and GHS
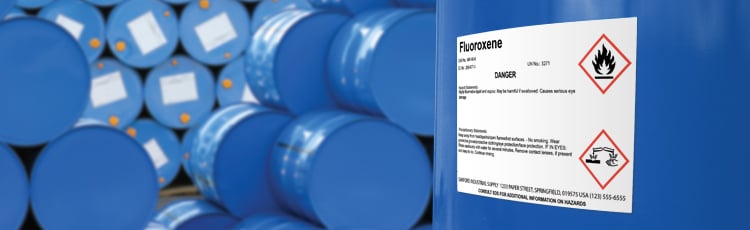
BS5609 is the British Standard for pressure-sensitive adhesive labels used for marine applications. Also known as the Marine Immersion Label Testing Standard, BS5609 is recognized internationally as the standard labels must meet when they are used on hazardous chemical containers shipped by sea. The purpose of BS5609 is to ensure that labels remain effective, even after months floating in the sea. With proper labeling the potential for negative environmental and health effects, resulting from chemical containers lost at sea, is reduced.
Why is BS5609 Compliance Important?
Drums, as well as other types of containers, are used to transport hazardous materials such as solvents, paint, petroleum products, chemicals, and hazardous wastes. Each of these containers must have a GHS label providing information about the contents and their associated hazards. When these containers are being shipped by sea, the GHS label must be able to survive exposure to salt water spray for extended periods of time. Because containers can be swept off ships during storms, or as the result of an accident, the GHS labels must also be able to survive immersion in salt water for up to three months, as well as abrasion resulting from contact with sand and rocks.
BS5609 compliance means that a GHS label has been tested and proven to be able to survive in salt water for up to three months.
Regulations such as the Merchant Shipping Act in the U.K. and the International Maritime Dangerous Goods (IMDG) shipping regulations require dangerous and hazardous material containers to be marked with durable labels. The term "durable" is interpreted to mean BS5609. In addition, sometimes BS5609 compliance is specified when extra durable GHS labels are needed, even though the shipment is not going by sea. Because BS5609 compliance assures general long-term durability in high moisture, bright sunlight, and extreme weather conditions, it is the standard most often referenced when extra durability is needed.
BS5609 Compliance and GHS
The Globally Harmonized System of Classification (GHS) provides standardized criteria for classifying the health, physical, and environmental hazards associated with a substance. It also has specific requirements for labels that must be on all shipments of hazardous or dangerous materials, including those shipped by sea. The information that must be on GHS labels includes:
- GHS Hazard Pictograms
- Signal Words: Either Danger or Warning.
- Hazard Statements
- Precautionary Statements
- Product Identifier
- Supplier Identification and Contact Information
The GHS label provides sufficient information such that anyone, who finds a container that was lost from a ship, will know the contents are hazardous and be able to contact the appropriate organization for more information.
If the GHS labels on containers shipped by sea could not survive an extended stay in seawater, when the container was found the contents of the container would be unknown. That could result in harm to people and the environment.
What Does BS5609 Compliance Testing Involve?
The BS5609 standard has three parts.
- Part 1: Provides an introduction to BS5609, definitions, and a description of the general requirements and responsibilities.
- Part 2: Provides the methods and requirements for testing the label's base material.
- Part 3: Provides the test methods and requirements for testing the printing on the label. The basic requirement is that the label survives at least three months immersed in seawater.
Part three testing must be done using the specific printer and ribbon that will be used for making labels and it must be done using a base material that has already passed the part two tests. Both tests must be passed successfully before a label can called BS5609 compliant.
BS5609: Part Two Compliance Testing
Part two testing is done using blank labeling material. This is the adhesive backed, pressure sensitive base material used for making labels. Testing involves accelerated artificial weathering tests (salt pray and sunlight), dimensional stability tests, and adhesion tests. If the material passes all of the tests, it is BS5609 Part Two compliant-but, it still may not be used for making labels.
When labels are printed there is an interaction between the base material and the ink used for printing. Some inks work better with some types of base materials than they do with others. Some ink and base material combinations are more durable than others under certain environmental conditions. That's why once a base material passes BS5609 Part Two testing, it moves on to Part Three testing.
BS5609: Part Three Compliance Testing
The basic requirement is that labels must be able to survive three months in salt water.
The labels to be tested are made by printing on a base material that has already passed the Part Two compliance testing. Both the label base material and printing must pass BS5609 tests involving exposure to salt water, sunlight, and abrasion. Some of these tests are conducted by putting labeled test blocks into the ocean, near the shore, for three months.
Since GHS labels include a red diamond as a part of the pictograms, some label base materials come with the red diamond pre-printed. In these cases, the BS5609 Part Three testing must be done on label base material that has the pre-printed red diamonds. All of the printing on the label must be subjected to the Part Three tests.
Passing BS5609 Part Three testing means that the specific printer used to print the label, the specific ink (ribbon) used for printing, and the specific base material, when used together, are BS5609 compliant. If a different printer or ribbon is used, the resulting label may not be compliant.
Related Resources
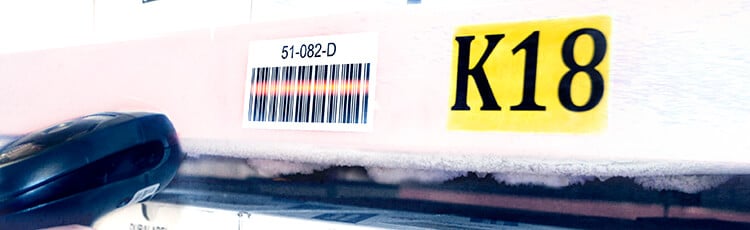
Growing Market Calls for Bigger Cold Storage Facilities
The food warehousing industry is booming and companies are expanding their cold storage warehouses. These ...
Read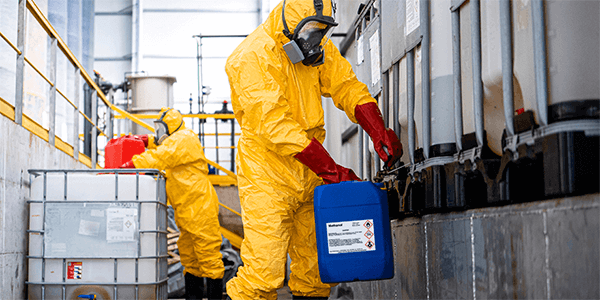
Choosing Outdoor Labels That Withstand Harsh Environments
How to Label for Extreme Environments and Maintain OSHA Compliance Labeling for extreme environments while ...
Read
Ensuring Lab Safety with Proper Labeling
A Comprehensive Guide for Pharmaceutical Companies In the realm of pharmaceutical research and development, ...
Read