HazCom Basics: Chemical Labeling 101

In the regulatory-driven healthcare environment, proper chemical labeling is required to ensure safety and compliance. The complexities involved in following the Globally Harmonized System of Classification and Labelling of Chemicals (GHS), particularly within a medical office and lab, present significant challenges. Here are some of the specific challenges and visual communication solutions to enhance GHS compliance and safety.
The Compliance Landscape: GHS and HazCom
GHS is a worldwide initiative aimed at standardizing chemical hazard communication. In the United States, the Occupational Safety and Health Administration (OSHA) has adopted GHS principles within its Hazard Communication Standard (HazCom).
According to OSHA, hazardous chemicals encompass a wide range, from household cleaners to lethal gases, with effects varying from mild skin irritation to severe conditions like cancer and organ damage. These hazardous chemicals are prevalent in virtually every industry, including manufacturing plants, healthcare labs, and construction sites.
Workers must understand what qualifies as hazardous materials and how to safely handle toxic substances, regardless of the specific hazards involved.
What Defines a Hazardous Chemical?
OSHA's regulation 29 CFR 1910.1200, commonly known as HazCom 2012, provides a comprehensive definition of "hazardous chemicals." These are defined as:
"Any chemical which is classified as a physical hazard or a health hazard, a simple asphyxiant, combustible dust, pyrophoric gas, or hazard not otherwise classified."
These hazards are generally broken down into two main categories: physical hazards and health hazards. The "physical hazard" and "health hazard" categories are included in the GHS. The other hazard types listed in that definition were added by OSHA, to fill the gaps in the international standard.
Physical hazards include fire hazards (including combustible liquids and flammable materials), explosion hazards (including compressed gas and explosives), and reactive hazards (including organic peroxide and unstable materials).
Health hazards fall into two categories: systemic effects (including carcinogens, corrosive materials, and irritants) and target organ effects (including neurotoxins and respiratory toxins). In order to pose a health hazard, significant evidence (such as at least one study) must indicate that exposure may have acute or chronic health effects.
The severity of these hazardous chemicals is reflected in a numbered category. Category 1 contains the most severe hazards (such as propane, a flammable gas), and the category numbers increase as the severity of each hazard decreases. Different hazard classes have different numbers of categories.
These hazards, ingredient information, and more details about a given chemical are communicated on a Safety Data Sheet (SDS), required in the HazCom 2012 standard. Some of those details are also required to appear on industrial safety labels placed on the chemical's container.
OSHA has also issued an advisory guide for hazard determination to help employers understand and comply with HazCom 2012 regulations. The guide assists employers with determining hazards, selecting chemicals, and analyzing data.
Dangerous Chemical Consequences
It's vital to wear proper personal protective equipment (PPE) while working around hazardous chemicals. OSHA's general PPE requirements for most workplaces can be found in 29 CFR 1910.132. Employees who don't comply with these regulations may face severe consequences when working with dangerous chemicals.
- Skin irritation: If employees aren't wearing the appropriate PPE and come in contact with hazardous materials, they may experience rashes, burns, skin irritation, and more.
- Respiratory damage: When employees work in areas that lack proper ventilation or don't wear respirators, they may be exposed to fumes from hazardous chemicals. This can result in immediate illness or even death, and in the long term, may lead to lung cancer or other respiratory illnesses.
- Burns: Workers may be severely burned when they don't wear proper PPE. Explosive chemicals may trigger blasts in a facility, and flammable chemicals may catch fire if not properly handled or stored.
Key GHS Compliance Requirements:
- Permanent Container Safety Labels: These labels must withstand various environmental conditions, maintaining legibility and adhesion.
- Secondary Container Industry Safety Labels: Often transferred to smaller containers, these lab labels require the same level of detail and durability as primary hazard communication labels.
- Replacement Container Safety Labels: In the event of label damage or deterioration, replacements must be immediately available and compliant.
- Lab Safety Label Regulations: A medical lab must adhere to stringent labeling practices to prevent accidents and ensure quick identification of hazardous substances.
GHS Compliance Challenges in Medical Facilities
- Diverse Chemical Usage: A medical office and lab uses a broad range of chemicals, each requiring specific handling and HazCom labeling.
- Dynamic Environments: Constant movement of materials and personnel increases the risk of label damage and misplacement.
- Education and Training: Ensuring all staff are adequately trained on GHS and HazCom standards can be resource-intensive.
- Regulatory Updates: Staying current with evolving regulations necessitates continuous monitoring and adaptability.
Working with Hazardous Chemicals
Employers and employees should do all they can to prevent catastrophic events around dangerous chemicals. This can be done through a combination of education, proper PPE, and signage that alerts workers to nearby hazards.
Proper PPE is often necessary when working around dangerous chemicals. You may need to protect your workers from head to toe with protective gear, including respiratory protection, as well as protection for the hands, feet, face, and more. Let employees know when PPE is required with clear warning labels and signs.
Employers should be up-to-date and in compliance with OSHA's HazCom 2012 regulations. The rules help employees understand the hazards posed by the chemicals they work with, including handling and storage guidelines, firefighting measures, exposure controls, and more. Request DuraLabel’s free Best Practice Guide to HazCom 2012 Labeling for detailed information.
Visual Communication HazCom Solutions
Effective visual communication is crucial in overcoming these compliance challenges. The following solutions can enhance HazCom labeling practices in medical facilities:
- Durable HazCom Label Materials: Utilizing high-quality, durable materials for HazCom labels ensures they remain intact and legible under various conditions. Laminated or UV-coated industrial safety labels can resist chemicals, moisture, and abrasion.
- Clear and Consistent Icons: Standardized GHS pictograms and icons provide immediate hazard recognition, reducing the risk of mishandling. Incorporating color coding can further enhance visibility and comprehension.
- Integrated GHS Labeling System: Adopting electronic labeling systems that generate and print compliant lab labels on demand can streamline the HazCom labeling process. These systems can be integrated with inventory management software to ensure accurate and up-to-date information.
- Customizable Templates: Offering customizable label templates that align with GHS and HazCom standards allows for easy adaptation to specific needs. This flexibility ensures HazCom labels meet all regulatory requirements while accommodating facility-specific nuances.
- Training and Resources: Providing comprehensive training programs and readily accessible resources on GHS and HazCom standards is essential. Visual aids, such as instructional videos and interactive modules, can enhance understanding and retention.
- Regular Audits and Inspections: Implementing routine audits and inspections to assess label condition and compliance can proactively identify and address potential issues. Utilizing checklists and mobile inspection tools can streamline this process.
HazCom Solutions from DuraLabel
Navigating the complexities of HazCom labeling compliance in medical facilities requires a strategic approach that emphasizes durability, clarity, and consistency. By leveraging advanced visual communication solutions, healthcare providers can not only meet regulatory requirements but also enhance overall safety and efficiency.
As the regulatory landscape continues to evolve, staying informed and proactive is key. Embracing innovative HazCom labeling technologies and practices will position medical facilities at the forefront of compliance and safety, ultimately contributing to better patient care and operational excellence.
Custom chemical hazard labels such as those made by DuraLabel industrial sign and label print systems can help you develop effective visual communication. DuraLabel carries more than 50 specialty supplies suited to application and industry-specific uses. Download our free Safety Data Sheets Guide for a comprehensive resource.
Read Next:
Related Resources

Hazardous Chemicals Overview
In the eyes of OSHA, hazardous materials run the gamut from household cleaners to deadly gasses. Effects can ...
Read
HazCom Plans Crucial in Preventing Employee Exposure
Several workplace chemical exposures have prompted OSHA to remind companies of proper respirator and ...
Read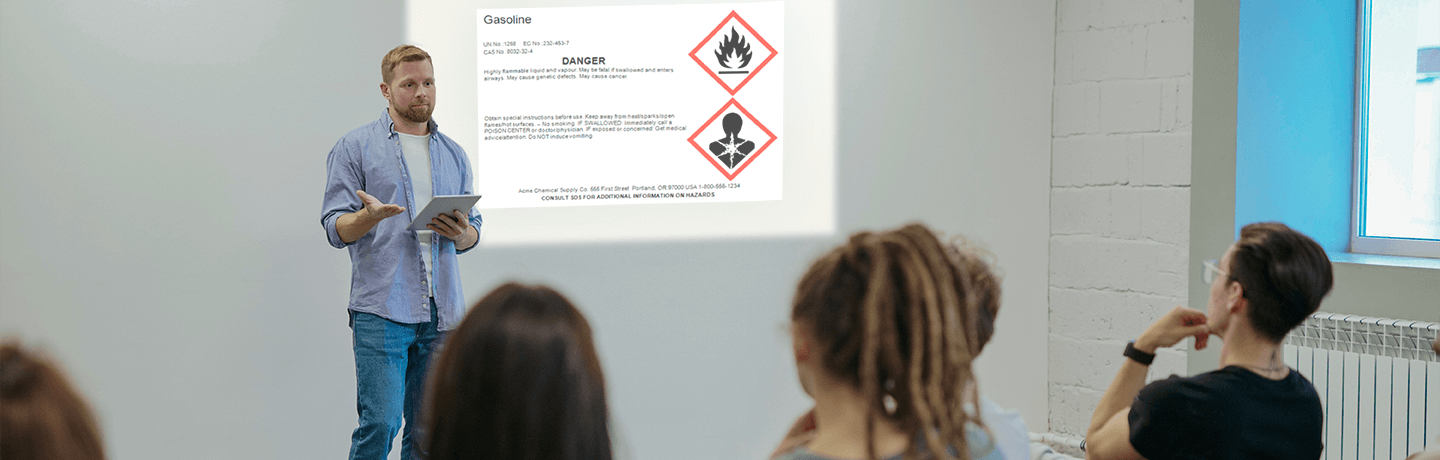
HazCom Training
OSHA's HazCom rules, sometimes called the Hazard Communication Standard or HazCom 2012, cover requirements ...
Read