HazCom Training
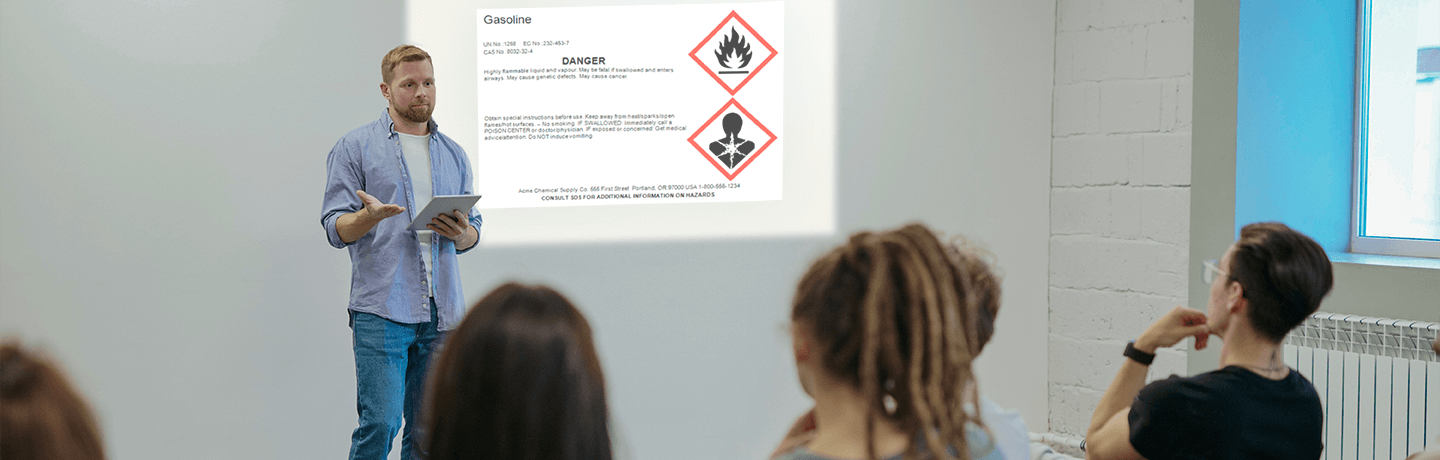
OSHA's HazCom rules, sometimes called the Hazard Communication Standard or HazCom 2012, cover requirements for providing workers with information about the hazardous chemicals in their workplace. When these rules were published in 2012, they were based on the United Nations' Globally Harmonized System, or GHS. While older systems often collapsed into contradictions and confusion, the new system is meant to clear up those problems with a coherent, consistent approach.
Without training, though, the new system can end up just as confusing. As a result, OSHA has included specific requirements for HazCom training in 29 CFR 1910.1200(h). The deadline for HazCom training was the first deadline in the transition period; since December 1, 2013, employers have been responsible for ensuring that their workers have this training.
What Is Needed for HazCom Training?
What do those requirements actually mean? The key is in the first section of those requirements, where 1910.1200(h)(1) requires that employees receive "effective information and training on hazardous chemicals in their work area." For chemical safety training to be effective, it needs to include at least four elements:
- How employees can recognize when a hazardous chemical is present in their work area, including accidental releases or spills
- The hazards posed by those chemicals
- How employees can protect themselves from these hazards, including safe work practices, emergency response steps, and Personal Protective Equipment (PPE)
- A full understanding of the facility's hazard communication program, including the container labels and Safety Data Sheet (SDS) for each chemical
1. Recognizing Hazardous Chemicals
When workers use hazardous chemicals as part of their ordinary work, the recognition that those chemicals are hazardous should be part of the workers' initial training, or "job orientation." Similarly, when hazardous chemicals will be present in an employee's work area, the worker should know. Most effective job training will already cover these basic requirements.
Extending this idea a little further will help protect employees in the case of an accident or spill. How can a worker identify the different hazardous chemicals in their area, and how can a worker know which chemical is which? If employees spot a puddle, can they tell what chemical is there? When these questions are resolved, you've covered the first element of HazCom training.
2. Understanding the Hazards
The next part of HazCom training is making sure that workers understand what hazards are posed by the chemicals in their work area. If a chemical is a "skin irritant," what does that mean for the workers' day-to-day work practices? What kind of results could be expected if that material splashed onto an employee's arm?
Each worker needs to be able to describe the hazards of the chemicals that they could be exposed to. Memorizing a list of vocabulary words isn't enough; workers need to understand what those phrases mean, and how serious each hazard is. When workers understand the hazards posed by the chemicals in their area, you've satisfied the second requirement for training.
3. Protecting Yourself from Hazards
Now that each worker can identify the hazardous chemicals in their work area, and understands what those chemicals' hazards are, it's time to protect the worker from those hazards. Is there a specific work practice that offers effective protection? Often, employees need personal protective equipment (PPE) for protection from chemical exposures. If workers need PPE, do they have easy access to that equipment, and have they been trained to appropriately use and maintain that equipment?
A major part of chemical safety is being prepared for accidents. Do your workers know how to respond to a spill, fire, or other accident that could cause a sudden spike of danger in the workplace? If workers can identify a chemical and understand its hazards, but don't know how to handle the chemical safely or respond to an emergency, they aren't prepared for their jobs-and your HazCom training isn't effective.
4. Knowing the Program
Each facility is slightly different, so every workplace needs its own approach for handling chemical information and ensuring that every employee has the training they need. OSHA has some broad requirements for these components of chemical safety, but requires each facility to have its own hazard communication program to answer the detailed questions.
While it can sound intimidating, the hazard communication program is really just a written plan for complying with OSHA's requirements.
- How will your facility manage SDSs, container labels, and employee training?
- What hazardous chemicals will be present in your facility?
- Are there any additional chemical hazards that your employees need to know about, and if so, how will you ensure that workers understand those hazards?
If you can answer these questions in writing, you've built the foundation of your facility's HazCom program.
In order for the program to work, employees need to know what the plan is. Give your workers that information, and document the training so you can show what's been done.
Get the Details with the SDS
It can be daunting to put together chemical recognition, hazard description, and appropriate protection details for every chemical in your facility. Fortunately, a chemical's SDS can do much of the "heavy lifting" in building your facility's HazCom training system; all of that information is already included in the sixteen sections of an SDS for each hazardous chemical.
Workers need to be trained to understand an SDS as part of your HazCom program already, so they can benefit from the wealth of information in these documents. Workers can't read an SDS if they can't find it, though, so another part of your HazCom training is to ensure that workers know where to look for these detailed documents.
Where Can I Find HazCom Training Materials?
Get help crafting a system that will provide the safety communication you need. Call 1-888-788-9855 and one of our experts will guide you through the process.
Learn more about the legal requirements that OSHA has created for American workplaces. Download our free Best Practice Guide to HazCom 2012
Read Next:
Related Resources

Hazardous Chemicals Overview
In the eyes of OSHA, hazardous materials run the gamut from household cleaners to deadly gasses. Effects can ...
Read
HazCom Basics: Chemical Labeling 101
In the regulatory-driven healthcare environment, proper chemical labeling is required to ensure safety and ...
Read
HazCom Plans Crucial in Preventing Employee Exposure
Several workplace chemical exposures have prompted OSHA to remind companies of proper respirator and ...
Read