What Is the Continuous Improvement Model?
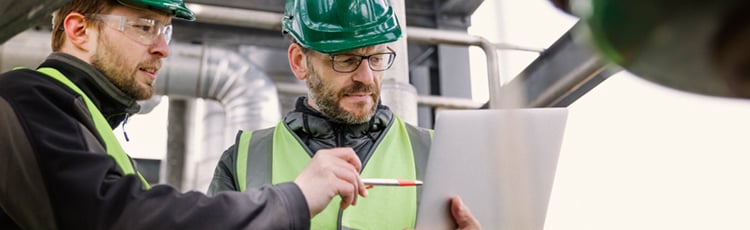
What is Continuous Improvement?
Continuous improvement is a philosophy of looking to improve products and processes. The greatest effort is spent on small, incremental changes. Over time, these changes add up to major improvements that increase efficiency, improve productivity, provide better quality, and reduce costs.
Continuous Improvement Model
Numerous continuous improvement methodologies are out there, including Kaizen, Plan-Do-Check-Act (PDCA), and others. Each methodology, in turn, relies on four underlying concepts:
- Employee engagement: Ideas for improvement come from employees, which they will also implement. This enables organizations to develop solutions that eliminate the root cause of the problem. Employee involvement allows them to feel like they are investing in the business by developing and implementing improvements.
- Incremental change: Many improvements are relatively minor in scope. They involve eliminating overly complex steps or processes, making it easier to implement future changes.
- Continuous feedback: Once improvements are put into action, monitor them, and improve upon them as necessary. Nothing is set and left alone forever.
- Measurable results: Goals are generally measurable, and when improvements are clear, those changes can apply to other areas of the business.
Each concept supports the other and helps create a sustainable model for continuous improvement.
Continuous Improvement Using the PDCA Cycle
Among the most widely used tools for continuous improvement is the PDCA cycle, also known as the Deming Cycle. PDCA is an organized approach to continuous improvement that guides the problem-solving process through four easy steps:
- Plan: The first step requires workers to identify an area that needs improvement, involve important stakeholders who may be impacted, and develop a plan as a team. When developing the plan, try to identify the root cause of a problem and develop a solution that will eliminate it.
- Do: Taking the plan, implement the change in a pilot area where it can be applied. Ideally, the improvement should only impact a small area, so it doesn't disrupt the workplace. Once implemented, keep track of what has been done and the results of the change.
- Check: Analyze the data and determine if the action had the expected impact. Did the change unexpectedly impact any areas or processes? Were there any negative effects brought about by the change? Did the change accomplish its overall goal?
- Act: If the change worked as expected, begin incorporating it throughout the business. Begin slowly at first, because the change may affect other parts of the business in a slightly different way than the first area. If the improvement didn't work, use what you've learned and restart the process at the "Plan" step.
Improvements shouldn't stop once implemented. Processes should continue to run through the PDCA cycle to address inefficiencies and other potential issues that arise over time, ensuring that work processes continuously improve.
Benefits of Continuous Improvement
Because most continuous improvement programs focus on small changes, businesses will see significant time and resource savings compared to large, capital intensive improvement projects. Benefits, however, are not limited to the initial cost savings.
Improved productivity: Problems are solved by the employees who perform the work. Workers will more readily notice issues that reduce productivity and develop solutions accordingly.
Simplified processes: Continuous improvement can eliminate arduous work. Workers should be directed to seek current processes that require excessive time or effort to complete. Once found, employees can run these tasks through PDCA and develop simpler processes.
Increased quality: Continuous improvement programs encourage employees to look for ways to improve the workplace. This includes looking for issues that impact quality. When found, employees work as a team to create a solution that eliminates defects and increases quality.
Improved communication and cooperation: If properly implemented, continuous improvement will result in better communication and excellent teamwork. At its very core, continuous improvement relies on worker engagement and building strong cross-departmental teams that work together to solve problems.
Who Should Use Continuous Improvement?
Many continuous improvement processes were created to improve manufacturing and production processes. However, continuous improvement can benefit many other sectors as well, including education, finance, IT, software development, and healthcare.
If your organization is looking to streamline processes or improve business practices, a variety of continuous improvement programs may fit your business' needs:
Visual Communication and Continuous Improvement
Support your continuous improvement program with clear, effective communication. DuraLabel industrial label and sign printers by Duralabel can help you communicate changes as procedures are improved, post essential safety information, and mark changes in workflow.
Need help getting started? Duralabel offers a free Kaizen & PDCA Best Practice Guide. You can also download our free TPM guide below, which can help jump start your continuous improvement program.
Related Resources
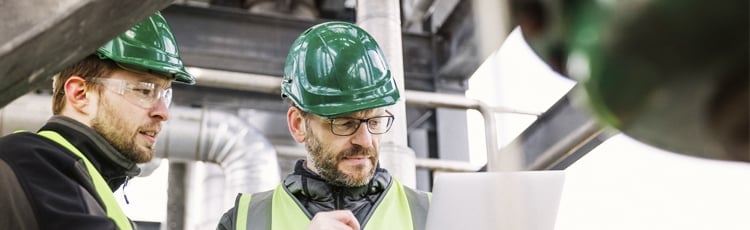
The Advantages of Lean Manufacturing: 5S, Kaizen, and TPM in Action
What Are the Advantages of Lean Manufacturing? Womack and Jones, in their book Lean Thinking, define lean ...
Read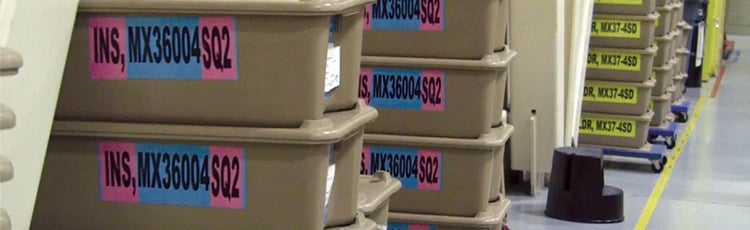
Lean Manufacturing Principles and The 5S System
What Are Lean Manufacturing Principles and Why Do They Matter? Lean manufacturing principlesare core ...
Read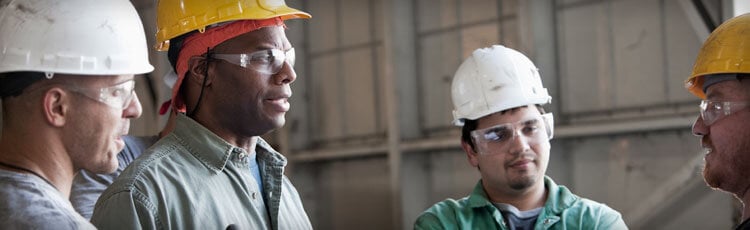
Quality Circles
The quality circle originated in Japan in the early 1960's. The objective was to give the responsibility for ...
Read