Elevate Your Safety Plan: Hierarchy of Hazard Control
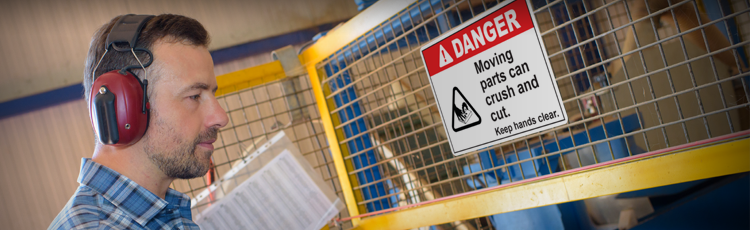
There are five levels to the hierarchy of hazard control:
- Eliminate the hazard.
- Substitute a less hazardous material or process.
- Engineering controls.
- Administration controls.
- Personal protective equipment.
To understand the five levels of the hierarchy of hazard control will result in a safer workplace. Always use the highest method on the list when possible.
Eliminate the Hazard
There is no better solution than eliminating hazards. Hazards can be eliminated by changing where or how work is done such as:
- Avoid the use of hazardous equipment.
- Machines
- Tools
- Materials
Substitution
Substitution is a form of hazard elimination and the two can be combined. Substitution involves switching out hazards for something non-hazardous. A typical example is replacing an oil-based paint with a water-based paint. This eliminates the harmful fumes and flammable vapors that result from using this product.
Engineering Controls
Engineering controls are used when a hazard cannot be avoided through elimination or substitution. This level does not eliminate the hazard but provides means to protect workers. Guarding moving parts is often referred to as "enclosure and isolation." Other examples of enclosure and isolation include:
- Motor Control Centers placed in a separate room protect workers from arc flash hazards.
- Curtains protect workers from the intense light from welding work.
- Barriers placed around fans and other noisy equipment reduce sound levels.
- Fences around electrical switch gear prevent access to high voltage equipment.
Engineering controls are also used to remove hazards. A common example is using a fume hood to contain and remove airborne hazards.
Administrative Controls
Administrative controls are used to direct people to work in a safe manner. They restrict access to hazards through procedures, warning signs, and training.
Administrative controls include:
- Limiting the amount of time someone is exposed to hazards.
- Written operating procedures.
- Standards for safe work practices.
- Safety and health rules for employees.
- Alarms, signs, and labels.
- Buddy system.
- Training (and refresher training).
- Stretching and warm-up exercises
- Break policies.
Using signs and labels to warn about hazards is a common administrative control and is required by OSHA. You can learn more about OSHA compliance with our OSHA Safety Signs Guide.
Personal Protective Equipment
PPE is considered the least effective method of protecting workers and often the last line of defense. Workers will be exposed to hazards if the PPE fails or is damaged.
Common PPE includes:
- Gloves
- Hard hats
- Safety shoes and boots
- Safety glasses/face shields
- High visibility clothing
- Respirators
Labeling for Safety
Take advantage of our free OSHA Safety Signs Guide to learn about OSHA and ANSI labeling compliance to optimize your location. Download your copy below!
Related Resources
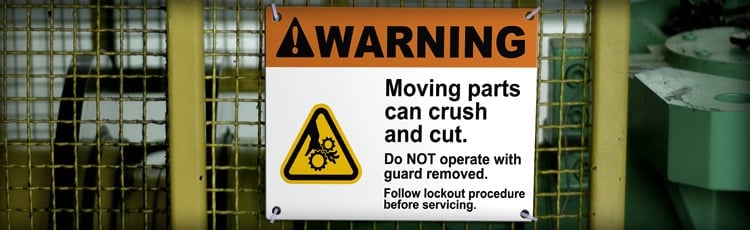
Hierarchy of Hazard Control
The hierarchy of hazard control has five levels, with those at the top of the list being the most effective. ...
Read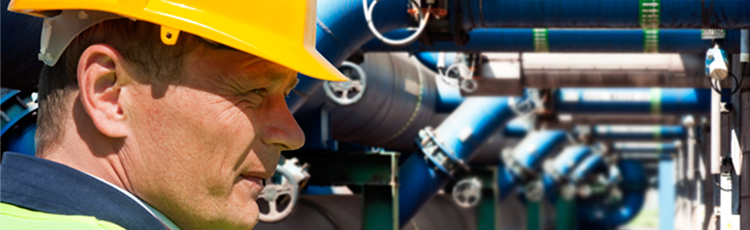
Hazard Analysis Risk Assessment
What is a Hazard Analysis? A hazard analysis is a systematic approach to identifying and assessing hazards in ...
Read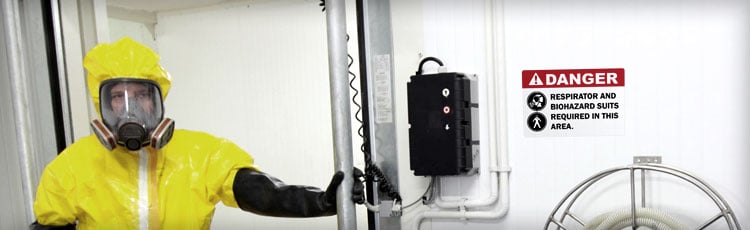
Short Term Exposure Limit
People have long recognized that no substance is absolutely safe. The Swiss physician Paracelsus, who lived ...
Read