Hazard Analysis Risk Assessment
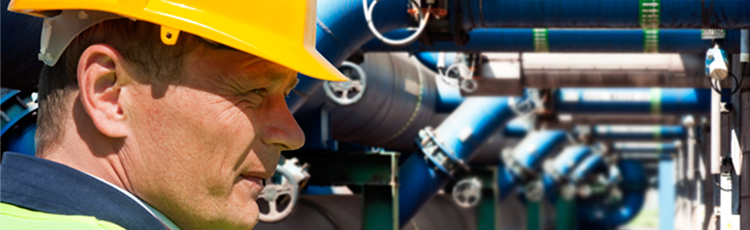
What is a Hazard Analysis?
A hazard analysis is a systematic approach to identifying and assessing hazards in the workplace and a critical first step in Safety Risk Management for your facility. In some cases, such as for processes that involve highly hazardous chemicals, OSHA standards require a hazard analysis and specify the methods that must be used. In other situations, the employer may select the method to be used. We'll use the OSHA requirements for "Process Safety Management of Highly Hazardous Chemicals" as our guidelines for an overview of hazard analysis.
The OSHA 1926 standard requires that "the process hazard analysis methodology selected must be appropriate to the complexity of the process and must identify, evaluate, and control the hazards involved in the process." OSHA provides a list of acceptable methods for evaluating hazards:
- What-if analysis
- Checklist analysis
- What-if/Checklist assessment
- Hazard and operability study (HAZOP)
- Failure mode and effects analysis (FMEA)
- Fault tree analysis
- An appropriate equivalent methodology
OSHA states that whichever method(s) are used for hazard analysis they must address the following:
- The hazards of the process
- The identification of any previous incident that had a potential for catastrophic consequences in the workplace
- Engineering and administrative controls applicable to the hazards and their interrelationships, such as appropriate application of detection methodologies to provide early warning of releases. Acceptable detection methods might include process monitoring and control instrumentation with alarms, and detection hardware such as hydrocarbon sensors
- Consequences of failure of engineering and administrative controls
- Facility siting
- Human factors
- A qualitative evaluation of a range of the possible safety and health effects on employees in the workplace if there is a failure of controls
The hazard analysis must be updated and revalidated on a regular basis. A good rule of thumb is following the OSHA standard, which requires a review at least every five years. A new hazard analysis should be conducted any time there is a change to the process, the process equipment, or to the process operating methods.
The hazard analysis should result in a written report documenting the hazards found, and provide recommendations for controlling those hazards, along with a schedule for when controls will be implemented. The report should include documentation of any actions that were taken, and how the changes will be communicated to various stakeholders such as the operations, maintenance, and safety departments.
Read more about Conducting A Job Hazard Analysis
What-if/Checklist Analysis
OSHA has a list of hazard analysis methods they deem acceptable. The What-if/Checklist is a combination of two methods-"What if" and "Checklist" into one. The "What-if" method is employed through a team of people with a variety of backgrounds-typically operations, maintenance, engineering, and safety. This team uses critical thinking to examine a given process and create "What if" questions. The basic information this team is provided with includes:
- P&IDs
- Equipment and control system designs
- A description of the process technology
- Identification of known hazards associated with
the materials and processes being used - Past accident and incident experience
- Overall industry experience with the process
- The results of previous hazard reviews
Applying the principles of gemba the team goes to the field and walks down the process, and talks with the people who are involved in operating and maintaining the process equipment.
The team then brainstorms possible hazards by posing the question "what if?" What if a certain valve failed open? What if fluid viscosity should exceed the specification? What if the bearing cooling water pump fails?
They look at the entire process from the receipt of raw materials through the delivery of the finished product to the customer. The result is a list of possible hazard conditions along with recommended actions that can be taken to protect against undesirable outcomes.
A checklist hazard analysis begins with an existing safety checklist. It may have been created by an individual, or be the result of a previous hazardous analysis. A typical checklist includes items such as:
- Are work areas clean?
- Are the right tools provided and being used?
- Is the correct PPE provided?
- Are all major components, pipes, and valves clearly labeled?
- Are operators trained and able to diagnose alarms?
- As Safety Data Sheet readily available?
- Are flammable materials properly stored?
The team goes through the checklist item by item, to stimulate questions about the process and possible hazards.
The final result is a set of questions about possible hazards. The team discusses these, reaching agreement on what is truly hazardous. They develop a list of recommendations for eliminating or protecting against those hazards and may recommend extended research of some of the questions.
Hazard and Operability Studies
A Hazard and Operability Study (HAZOP) systematically identifies all of the ways in which operating conditions can deviate from the intended design, with the result being a safety hazard or an operating problem.
HAZOP typically starts with the P&IDs, a plant model, or an overall facility map. A team of experienced people, who are familiar with the process brainstorm potentially hazardous situations. They look at each section of pipe, valve, flange, pump, vessel, and other components in the system to identify potentially hazardous conditions.
Read about Hazard and Operability Studies.
Failure Mode and Effect Analysis
Failure Mode and Effect Analysis (FMEA) is an approach to hazard analysis that involves intense study of individual machines and components to identify failure modes and the consequences.
A FMEA begins with reviewing process diagrams such as the P&IDs to identify components that if failed, might affect the safety of the process. Each component identified as a potential source of a safety hazard is listed on a tabulation sheet, and questions are asked:
- What are the potential failure modes? (Open, closed, partially open, leaking, on, off, etc.)
- What is the consequence of the failure?
- What effect will failure have on other components?
- Is there the possibility of cascading failures?
- What effect will failure have on the overall process?
- What is the effect of concurrent multiple failures?
- What effect will failure have on the surroundings and environment?
- At what level should this hazard be classified? (High, moderate, low, etc.)
- What is the probability of failure?
- How can failure be detected?
- How can pre-failure conditions be detected?
- What can be done to mitigate the consequences of failure?
Based on answers to these types of questions, the risk associated with the potential failure of each component is evaluated, and appropriate recommendations are made.
Fault Tree Analysis:
A fault tree analysis uses a diagram that shows the relationship of contributing causes to a specific undesirable outcome. This may be found by reviewing incident records, and in particular near-miss records, or simply brainstorming.
The undesirable outcome is identified in a box at the top of the page. All possible sequences of events that could lead to the undesirable outcome are placed on the diagram, using logical OR and AND symbols to connect outcomes with causes. The result is a chart that looks like a tree, with each main branch representing an independent path to the top (the undesirable event). A probability, based on failure rate data, is assigned to each event and used to calculate the probability of occurrence of the undesired event.
Learn more about mitigating hazards and improving safety with OSHA-related articles, guides, videos, and more.
Free OSHA Safety Signs Guides
Download our free OSHA Safety Signs Guide to learn how visual communication can help to minimize facility accident risks. Get your copy below.
Related Resources
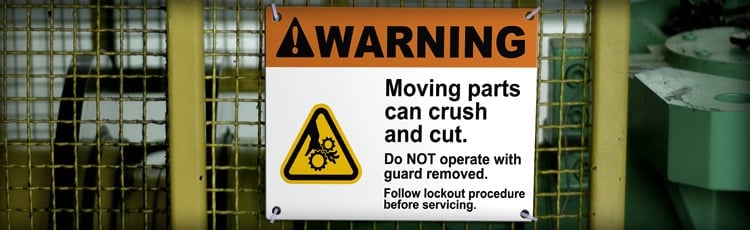
Hierarchy of Hazard Control
The hierarchy of hazard control has five levels, with those at the top of the list being the most effective. ...
Read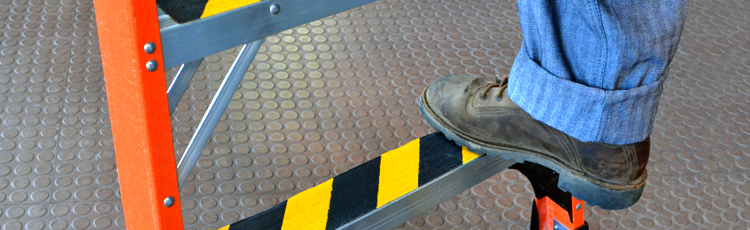
Beware of Introducing New Hazards
Risk assessments need to be thorough and regular for all changes in the workplace, even when those changes ...
Read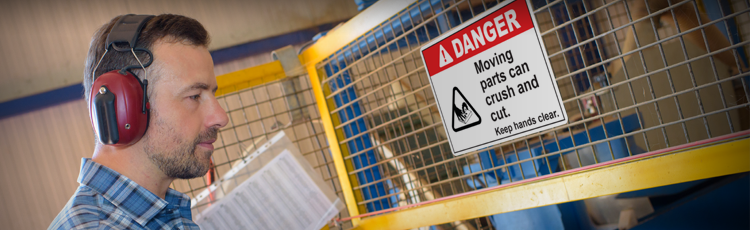
Elevate Your Safety Plan: Hierarchy of Hazard Control
There are five levels to the hierarchy of hazard control: Eliminate the hazard. Substitute a less hazardous ...
Read