Explosive Hazard

A ranch worker was grinding a 300-pound gasoline tank late Wednesday when the tank exploded, killing the worker and seriously injuring two other workers, a state health and safety official said
Three people were hurt after an explosion and fire inside a building in Kansas City, Kansas. Firefighters said there was some sort of dust explosion, possibly caused by static electricity. Nineteen people were inside at the time
An underground explosion in Providence sends eight manhole covers into the air. Two people sustained minor injuries in what authorities said could have been caused by a buildup of carbon monoxide from an underground electrical fire.
What comes to mind when you hear the phrase "explosive hazard?" Probably fireworks or maybe a dynamite factory. The majority of explosive hazards are not caused by recognized explosives, but by common materials with which we work every day. When it comes to explosive hazards, these are accidents we don't expect ? and that makes explosive hazards even more dangerous.
Hot Work Explosive Hazard
Hot work is any work that involves burning, welding, or using tools that produce fire or sparks. It is essentially any work that produces a source of ignition energy. Explosions happen when hot work is done in a location where flammable vapors exist. For example, as described in the above news report, cutting or welding on a tank that had been used to store a flammable liquid such as gasoline, is a frequent cause of explosions.
A tank or other storage vessel may appear to be clean, or access to the interior of an old tank may not be easily possible. Then someone decides it's time to cut up the tank and sell the scrap, and the result is an explosion. Here are a few guidelines to follow before doing any hot work on a tank or other type of storage vessel:
- Conduct a hazard assessment before starting the work.
- Ensure all fuel sources are isolated before starting work.
- When appropriate, use gas monitoring systems with automatic shut-offs and alarms.
- Never assume a tank or vessel is free from explosive vapors, even if that tank has an opening.
- Test for flammable gases in the work area before starting any hot work.
- Use ventilation to reduce flammable gas concentrations.
- Never enter a tank or vessel without first testing the atmosphere inside that tank or vessel.
Dust : The Explosive Hazard
The most deadly explosive hazards have been dust explosions.
A combustible material will burn much more rapidly when it is finely divided. If broken down into dust that is suspended in air, combustible materials become explosive under certain conditions. Even materials that normally do not burn, such as aluminum or iron, become explosive hazards when they are in the form of dust suspended in the air.
Dust is a serious explosive hazard. For example, three people were killed in a 2010 titanium dust explosion in West Virginia. In a 2008 sugar dust explosion in Georgia resulted in 14 deaths. The explosion hazard from dust can equal that of a chemical explosive.
In many dust explosions, workers and managers were not aware there was an explosive hazard. In a 2006 study conducted by the Chemical Safety Board (CSB) it was found that the Material Safety Data Sheets (MSDS) for 140 substances that are known to produce combustible dust had inadequate information about the explosive hazard of dust.
The OSHA Hazard Communication Standard (HCS) covers dust and other hazardous particulates. Under these OSHA standards, a hazard evaluation must be conducted, and that evaluation must take into consideration all discernible hazards ? including explosive hazards. This means that manufacturers and importers of chemicals, and other materials, must provide information on the potential for explosive hazards, as well as information about the control of combustible dust.
September 23, 2004 - The U.S. Chemical Safety and Hazard Investigation Board (CSB) today released its final report on the investigation of last year's fatal dust explosion and fire at West Pharmaceutical Services Inc. ... The accident killed six workers and injured 38 others, including two firefighters. The blast could be felt 25 miles away, and burning debris ignited fires in wooded areas as far as two miles away. A large fire at the plant burned for two days.
Combustible Dust : Understanding the Explosive Hazard
Combustible dusts are fine particles that present an explosion hazard, under certain conditions, when suspended in air. Five conditions are needed for there to be a dust explosion. These five conditions are referred to as the "Dust Explosion Pentagon". The first three conditions are the same as those needed for a fire:
- Combustible dust (fuel)
- An ignition source
- Oxygen (in air for example)
An additional two conditions must be exist in order to have an explosive dust hazard:
- A sufficient quantity and concentration of dust particles
- Confinement of the dust cloud
If one of these five conditions does not exist, there is no explosive hazard.
A dust explosion frequently happens in two stages. There will be an initial (primary) dust explosion in processing equipment. The smaller explosion shakes lose dust that has accumulated on top of equipment, ducts, piping, etc. Or it may damage a containment system such as a duct, collector, or storage bin. This causes the accumulated dust to become airborne, creating an explosive hazard that is much gr
Combustible dust is fine particles that present an explosion hazard, under certain conditions, when suspended in the air. Five conditions are needed for there to be a dust explosion. These five conditions are referred to as the "Dust Explosion Pentagon". The first three conditions are the same as those needed for a fire:
- Combustible dust (fuel)
- An ignition source
- Oxygen (in the air for example)
- An additional two conditions must exist to have an explosive dust hazard
- A sufficient quantity and concentration of dust particles
- Confinement of the dust cloud
If one of these five conditions does not exist, there is no explosive hazard.
A dust explosion frequently happens in two stages. There will be an initial (primary) dust explosion in processing equipment. The smaller explosion shakes loose dust that has accumulated on top of equipment, ducts, piping, etc. Or it may damage a containment system such as a duct, collector, or storage bin. This causes the accumulated dust to become airborne, creating an explosive hazard that is much greater than the initial dust explosion.
Combustible Dust : The Severity of the Explosive Hazard
The severity of a combustible dust explosion, as well as the ease of ignition, are dependent on the dust particle size. Dust particles smaller than 420 microns (particles that can pass through a U.S. No. 40 standard sieve) are most likely to be an explosive hazard. However, larger particles still pose a hazard. For example, large particles can abrade each other, creating smaller particles. Or particles can stick together as a result of electrostatic charges or moisture. They then become an explosive hazard when the force holding them together no longer exists.
Other factors that have a secondary influence on the explosiveness of dust include:
- moisture content
- ambient humidity
- oxygen available for combustion
- the shape of dust particles
- the concentration of dust in the air
Variations in these characteristics can change the severity or likelihood of an explosive hazard.
The types of dust that can result in an explosive hazard include:
- metal dust, such as aluminum and magnesium
- wood dust
- plastic dust
- rubber dust
- bio-solids
- coal dust
- organic dust, such as flour, sugar, paper, soap, and dried blood
- textile dust
Combustible Dust - Preventing an Explosive Hazard
The first step in preventing a combustible dust explosive hazard is good housekeeping. This involves preventing dust from accumulating on horizontal surfaces, including floors, ducts, pipes, etc., and cleaning up any dust that does accumulate.
Equipment such as bins, vessels, ducts, dust collectors, and processing equipment that contain combustible dust must be designed so as to prevent leaks and minimize the escape of dust into work areas. Equipment or storage locations where there is an explosive hazard should be designed to relieve pressure in a safe manner, such as having "zippered" corners or "explosion hatches."
A good place to turn for explosion hazard prevention practices is the National Fire Prevention Association (NFPA). They have developed more than 300 consensus codes and standards. The standards related combustible dust explosive hazards are:
- 61 - Standard for the Prevention of Fires and Dust Explosions in Agricultural and Food Processing Facilities
- 484 - Standard for Combustible Metals
- 654 - Standard for the Prevention of Fires and Dust Explosions from the Manufacturing, Processing, and Handling of Combustible Particulate Solids
- 655 - Standard for Prevention of Sulfur Fires and Explosions
- 664 - Standard for the Prevention of Fires and Explosions in Wood Processing and Woodworking Facilities
Labels and signs have an important role in preventing explosive hazards. They are used to remind people about housekeeping and the importance of good housekeeping. They provide instructions for the proper start-up, operation, and shutdown of equipment. They identify the locations of fire extinguishers and other firefighting equipment. However, if labels and signs fail, or if they were never used in the first place, important information employees need is not available. DuraLabel custom label printers and tough-tested supplies solve that problem. They create tough, durable labels and signs that are quick and easy to make. Call 888.695.5670 today and ask about the special money-saving DuraLabel kits.
Don't Wait Until it's too Late
Whether you need safety signs, pipe markers, or equipment labels—Toro Max is ready to transport anywhere you are. Get help crafting a system that will provide the safety communication you need. Call 1-888-695-5670 and one of our experts will guide you through the process.
Learn more about establishing an emergency response plan for your facility or workplace. Our free Emergency Preparation Chart provides the industry best practices for labeling and marking your facility so when an emergency hits, your staff is prepared. Download your copy below.
Read Next:
Related Resources
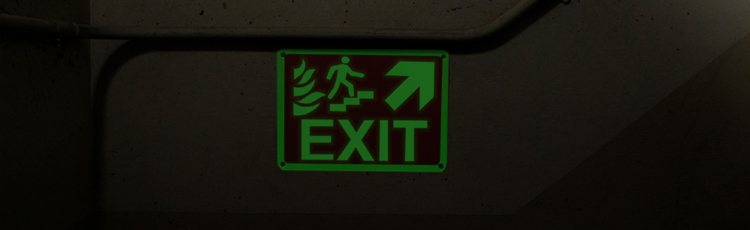
Five Ways You Can Prevent Fires at Your Office
National Fire Prevention Week is October 9-16 and gives good cause for pause for many of us who work in ...
Read
Fire won't wait. Plan your escape during National Fire Prevention Week October 9-15th
In 2021, local fire departments responded to 1,353,500 fires in the US. That averages out to one every 23 ...
Read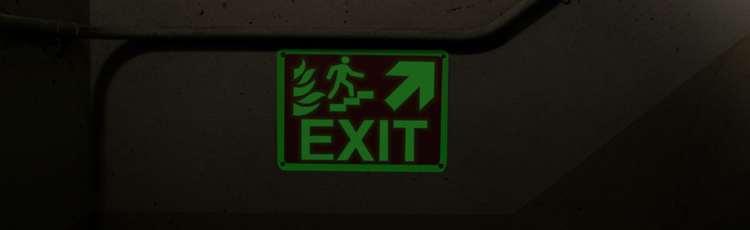
International Fire Code: Fire Prevention and Safety Standards
The International Fire Code (IFC) provides fire prevention and safety standards for existing buildings. It ...
Read