The Five Whys: Root Cause Analysis Made Simple
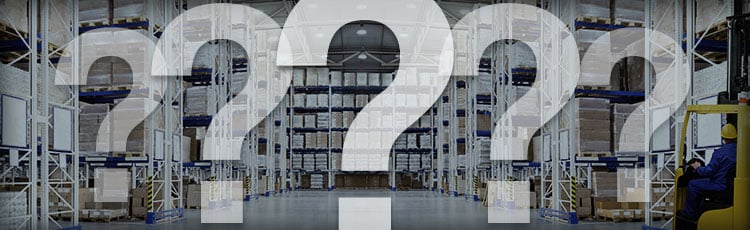
The five whys analysis is also known as the why-why chart and root cause analysis. As these names imply, the purpose is to find the true root cause of a problem (Andersen and Petersen, 1996). The technique can very well be used in connection with a cause-and-effect chart to analyze each identified cause to ensure that it really is the root cause of the problem and not only a symptom of another and more deeply rooted cause. This can in fact be compared to peeling an onion, where each layer is removed to reveal another layer, until the center of the onion is reached.
The Five Whys is a question asking technique for identifying the root cause of a problem. It involves asking the question "why" as many times as necessary to identify the root cause. It's called "Five Whys" because it typically requires asking "why?" at least five or more times.
The answer to the last "why" question normally points out where the main problem is. For example, many times the root cause investigation will stop when an answer such as, "it was out of my control," or "there were not enough hours available," is heard. But, this is not the root cause. The Five Whys process needs to continue with a question such as, "Why were there insufficient hours available?"
Five Whys? An Example
Taking a famous example from Benjamin Franklin's Poor Richard's Almanac we could ask the following series of why questions:
- Why was the kingdom lost? Because the battle was lost.
- Why was the battle lost? For want of an army.
- Why was the army lost? For want of a rider.
- Why was the rider lost? For want of a horse.
- Why was the horse lost? For want of a horse shoe.
- Why was the shoe lost? For want of a nail.
The point Benjamin Franklin made was that, because a small item such as a nail was missing, an entire kingdom was lost. However, this is not a good Five Whys analysis, as it has not identified the root cause. At least one additional "why" question needs to be asked, "why was there no nail available?"
When doing a root cause analysis using Five Whys, keep in mind that it is almost always a process that has failed. Keep asking "why?" until a process has been identified, and the reason for the failure of the process has been identified.
The Five Whys Process
A problem has been identified and you want to find the root cause. How is Five Whys applied?
- Start by going to the location where the problem exists. In Lean terms this is called gemba. By physically going to the location of the problem you can observe the situation yourself, and talk directly with those who know the most about what is happening.
- Write the definition of the problem at the top of a sheet of paper. Then ask the question, "Why is this problem taking place?"
- Write down the answer(s) you get. For each answer ask "why" again, until the answer identifies a root cause. If you get multiple answers to a "why" question, treat each one as a separate branch to follow, asking "Why?" until a root cause is identified for each one.
- There may be multiple root causes, or cascading root causes. Be sure to ask "why" a sufficient number of times to identify all potential root causes.
Five Whys - Cause-and-Effect Chart
A Cause-and-Effect Chart, sometimes called a fishbone diagram, is used to identify all potential factors that contribute to an outcome. It is a tool that is often used to analyze the results from Five Whys to verify the actual root cause has been identified.
To make a Cause-and-Effect Chart begin by writing a definition of the problem in the middle of the right side of a sheet of paper. Draw a horizontal line from that definition across the page.
Bring together a team to use the results from Five Whys, combined with brainstorming additional ideas, to identify potential causes of the problem. These are added as smaller lines connected to the horizontal line, creating a fishbone pattern. For each potential cause that was identified, continue brainstorming to identify possible contributing factors. These further ideas are added as lines drawn off of each individual cause line. This may be done a number of times, resulting in a diagram that is three or four layers deep.
Once the team has finished brainstorming, each cause can be investigated and analyzed. This will help to identify the cause, or causes that are actually the source of the problem.
Benefits of the Five Whys
- The Five Whys provides a simple, practical, easy to learn, and quick method for identifying the root cause of a problem. The key is to ask "why" a sufficient number of times such that the real root cause is identified. Anyone can learn to do this.
- The Five Whys can identify multiple potential root causes allowing the relationship between different potential root causes to be identified and analyzed.
- It is easy to do.
- The Five Whys provide a quick method for identifying root causes, which can be applied with little up-front preparation time. The problem can be quickly identified and fixed at a minimal cost in downtime and resources.
The Five Whys method for identifying root causes is very simple, yet incredibly powerful. Persistently asking "why" until the root cause is identified is a tool that should be in everyone's lean toolbox.
Ready to Get Started?
Download our Kaizen & PDCA Best Practice Guide for detailed expert tips on how to implement Kaizen and the Five Whys at your organization.
Related Resources
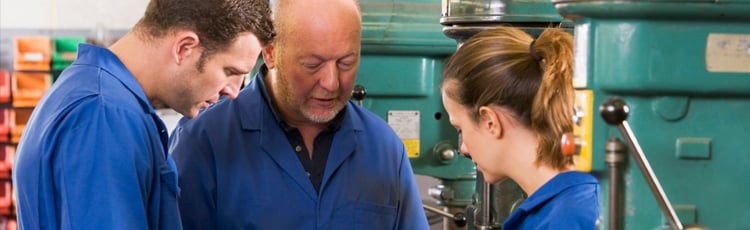
8D Methodology
The 8D methodology (8D=eight disciplines) was developed in Ford Motor Company in the mid-1980s to be used by ...
Read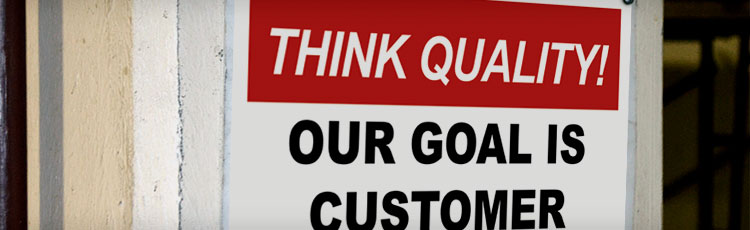
What Is ISO 9001
The International Organization for Standardization (ISO) is the world's largest developer and publisher of ...
Read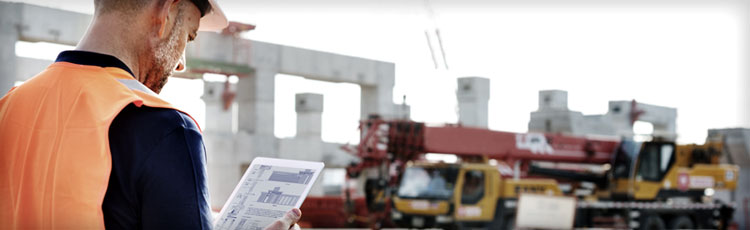
Lean Construction
What is Lean Construction? A term that is coming into common use is "lean construction." Lean construction ...
Read