Job Safety Analysis
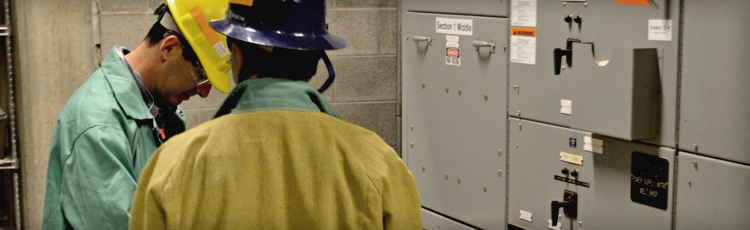
A Job Safety Analysis (JSA) is a risk assessment tool used to identify job-related hazards. The Job Safety Analysis is also known as a Job Hazard Analysis (JHA) or Task Hazard Analysis (THA).
A Job Safety Analysis uses a structured approach to look at each step required to complete a job. The object is to reveal potential hazards, as well as to identify possible ways to eliminate those hazards.
What is a Job Safety Analysis?
There are two common approaches to performing a Job Safety Analysis.
One approach is to go to where the work is being done and observe a worker performing their job as they normally do it. As the work is observed, the steps required to get the job done are noted. The observer also notes any potential hazards that might be encountered during each step. In many cases, it is worthwhile to observe the job once to record all the steps involved in doing the job, and then observe the job again to note potential hazards.
The second approach is to assemble a team of workers and supervisors who have experience doing the job to be analyzed. That team meets to identify the steps needed to complete the job; then they brainstorm possible hazards, as well as solutions to those hazards.
The Job Safety Analysis Process
There are four steps involved in conducting a Job Safety Analysis:
- Select the job(s) to be studied.
- Identify the steps required to do the job.
- Identify the hazards that may exist during each step.
- Identify corrective actions to eliminate or mitigate the hazard.
Job Safety Analysis ? Selecting the Job
The safety of just about any job can be improved using a Job Safety Analysis. However, the best approach is to study those jobs where the JSA will do the most good. The types of jobs that should be targeted for a Job Safety Analysis include:
- Those with the highest injury or illness rates.
- Those that have the greatest potential to cause the most harm.
- Those that can easily lead to a serious accident or injury
- Those jobs that are new or have recently changed.
- Those jobs that are not done frequently.
- Any job that is complex enough to require written instructions.
When selecting jobs for a Job Safety Analysis, involve the people who do the work. They are the ones who can best identify those jobs with the greatest risk. For example, there may be a task for which no accidents have been reported for over a decade. That would appear to be a low-risk task! However, the reason for the good safety record is that the same people have been doing that job for several decades. They know the work inside-out. They know the hazards of the job, and how to be safe. When they retire, though, they'll take that experience with them ? unless it is captured using a Job Safety Analysis.
Job Safety Analysis ? Identify the Steps Required for the Job
Someone familiar with the work being done, such as a supervisor, should observe the job as the work is being done in a normal manner and take note of each step. However, it is important that those doing the work understand what is going on. This is not a performance evaluation, or a productivity study; the information collected as a part of a Job Safety Analysis should never be used for those purposes. The sole purpose is to identify potential safety or health hazards. It is important that the person doing the work do it as they normally would, using the tools and equipment they normally use.
When observing, make a note of each step required to get the job done. In particular, note worker movements. Each movement will typically be related to a step.
The list of steps should not be too generic. Leaving out steps that may seem insignificant can also result in associated hazards being missed. However, the list of steps should also not be too detailed; the result would then be too many steps, which will make analysis difficult. A good rule of thumb is that most jobs can be described in roughly ten steps. If there are more than ten steps, divide the job into two parts and treat each part as a separate job.
To keep the information organized, a standardized form is typically used. A simple three column form is common. The left column identifies the step; the center column describes the motion and identifies the person performing that motion; and the right column is used to note potential hazards.
Job Safety Analysis ? Identify the Hazards
Some hazards may be obvious, and can be noted at the same time as the job steps are being identified. However, it is often helpful to watch the job being performed a second time, after the list of steps has been created. This makes it easier to focus on identifying the hazards.
To identify hazards, look for potential sources of energy and watch for worker motion that might bring part of their body near that source of energy. Observe the complete environment where the job is taking place. What are other workers in the same area doing? Could their activities contribute to an accident? Also, observe how workers need to move. When a worker reaches for something, for example, do they need to twist their body or lean over in order to reach the object?
The Canadian Centre for Occupational Health & Safety recommends asking questions such as:
- Can any body part get caught in or between objects?
- Do tools, machines, or equipment present any hazards?
- Can the worker make harmful contact with moving objects?
- Can the worker slip, trip, or fall?
- Can the worker suffer strain from lifting, pushing, or pulling?
- Is the worker exposed to extreme heat or cold?
- Is excessive noise or vibration a problem?
- Is there a danger from falling objects?
- Is lighting a problem?
- Can weather conditions affect safety?
- Is harmful radiation a possibility?
- Can contact be made with hot, toxic, or caustic substances?
- Are there dusts, fumes, mists, or vapors in the air? (CCOHS)
Job Safety Analysis ? Importance of Labels and Signs
When conducting a Job Safety Analysis, be aware of the impact that the work environment can have on safety and health. For example, be sure that the required safety signs and labels are in place, and in good condition. This includes both workplace signs and labels, as well as labels on equipment and tools. Replace any missing, damaged, or unreadable labels and signs.
Do workers have the tools they need to make LO/TO tags, temporary safety signs, and the needed replacement labels and signs? If they have a DuraLabel printer handy, the answer is "yes." DuraLabel custom label printers easily handle all required safety labeling and signage needs, and more. With tough-tested supplies, DuraLabel printers get the job done right. Call us for more information about DuraLabel printers and supplies. Ask about the special money-saving DuraLabel kits.
Related Resources
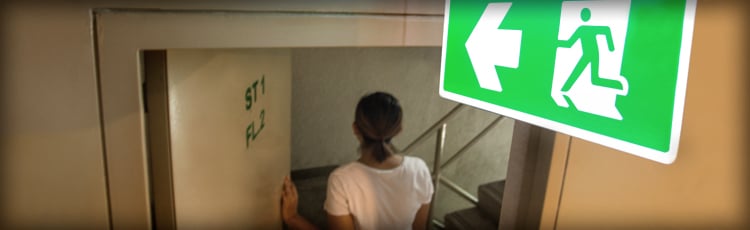
Fire Exits
If your building starts filling with smoke, how will you quickly get out? Do you know where the closest exits ...
Read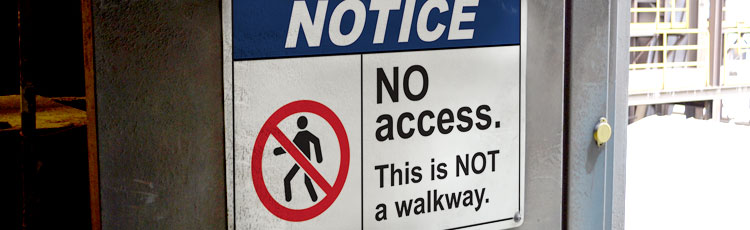
Five Hidden Benefits of Safety Signage
Workplace safety has improved dramatically in recent decades-worker injuries and illnesses have decreased ...
Read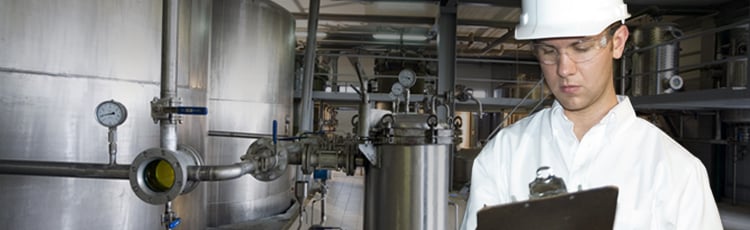
Understanding OSHA Citations: Common Violations and Penalties
OSHA citations are routinely given to companies throughout the United States. Organizations large and small ...
Read