Kanban Benefits
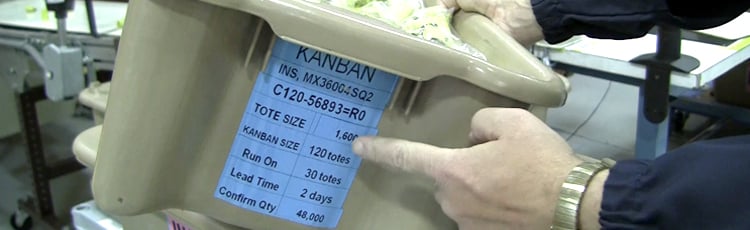
Kanban Provides a Number of Benefits.
Kanban was developed as a method for controlling the flow of materials within a supply chain to reduce waste. Kanban simply means "billboard" or "visual signal." Using visual signals (cards), Kanban controls inventory by pulling supplies to the production floor based on customer demand. So Kanban, the pull inventory system, provides a number of benefits for your production line.
Reduce Inventory & Product Obsolescence
Since component parts are not delivered until just before they are needed, there is a reduced need for storage space. Should a product or component design be upgraded, that upgrade can be included in the final product ASAP. There is no inventory of products or components that become obsolete.
This fits well with the Kaizen system of continual improvement. Product designs can be upgraded in small increments on a continual basis, and those upgrades are immediately incorporated into the product with no waste from obsolete components or parts.
Reduces Waste and Scrap
With Kanban, products and components are only manufactured when they are needed. This eliminates overproduction. Raw materials are not delivered until they are needed, reducing waste and cutting storage costs.
Provides Flexibility in Production
If there is a sudden drop in demand for a product, Kanban ensures you are not stuck with excess inventory. This gives you the flexibility to rapidly respond to a changing demand.
Kanban also provides flexibility in how your production lines are used. Production areas are not locked in by their supply chain. They can quickly be switched to different products as demand for various products changes. Yes, there are still limits imposed by the types of machines and equipment as well as employee skills. However the supply of raw materials and components is eliminated as a bottleneck.
Increases Output
The flow of Kanban (cards, bins, pallets, etc.) will stop if there is a production problem. This makes problems visible quickly, allowing them to be corrected ASAP.
Kanban reduces wait times by making supplies more accessible and breaking down administrative barriers. This results in an increase in production using the same resources.
Reduces Total Cost
The Kanban system reduces your total costs by:
- Preventing overproduction
- Developing flexible workstations
- Reducing waste and scrap
- Minimizing wait times and logistics costs
- Reducing stock levels and overhead costs
- Saving resources by streamlining production
- Reducing inventory costs
Related Resources
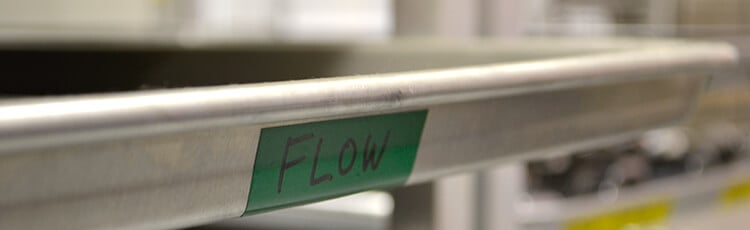
Pull System
What Is a Pull System? A pull system is a lean manufacturing strategy used to reduce waste in the production ...
Read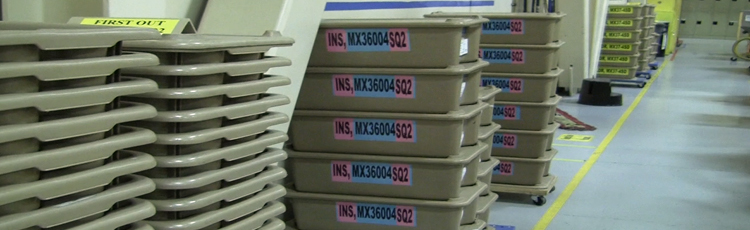
Start a Workplace Kanban Board
Efficiency is a necessity in business and life. Increasing efficiency saves time and money, which in turn ...
Read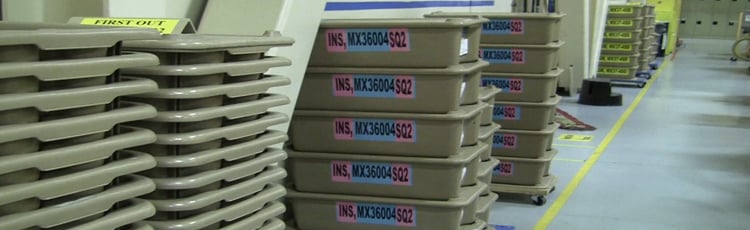
What Is Kanban?
In the face of declining sales and profits during the 1950s, Eiji Toyoda began looking for ways to improve ...
Read