Pull System
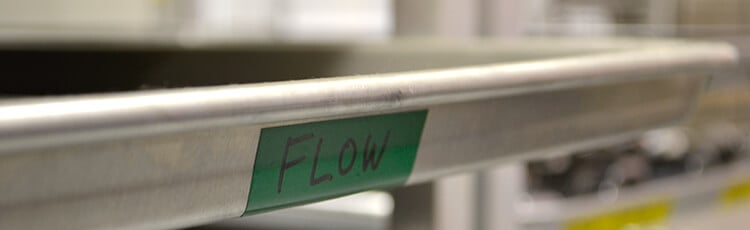
What Is a Pull System?
A pull system is a lean manufacturing strategy used to reduce waste in the production process. In this type of system, components used in the manufacturing process are only replaced once they have been consumed so companies only make enough products to meet customer demand. This means all of the company's resources are used for producing goods that will immediately be sold and return a profit.
Essentially, a pull system works backwards, starting with the customer's order then using visual signals to prompt action in each previous step in the process. The product is pulled through the manufacturing process by the consumer's demand.
Pull System vs. Push System
Another system used in supply chains is a push system, which sharply contrasts with a pull system. In a push system, units are produced based on forecasted demand and then pushed into the market, whereas a pull system uses actual demand. Companies using a push system must predict what the customer will want to purchase and in what quantity, which is difficult as sales can be unpredictable and vary from previous years.
In a pull system, the quantity produced is just enough to meet current demand. However, in a push system, products are mass produced for estimated future demand. These products must remain in inventory until they are needed, which could take months, years or may not happen at all.
Advantages of Using a Pull System
Manufacturing facilities greatly benefit from switching from a push system to a pull system. Using a pull system reduces waste within a company since no overproduction occurs. This also frees up space in the workplace and reduces the cost of storing excess inventory.
Businesses that use a pull system experience increased customer satisfaction as products are manufactured specifically to fulfill their requests. Since products are made in small quantities, quality issues will be identified faster than with a push system and, if an error is found, less defective products would require disposal.
A pull system allows manufacturing facilities to save time that would be spent planning for future demand and producing goods that may never be sold. They also experience increased flexibility, as they can rapidly respond to changes in demand. Each of these advantages of using a pull system reduces total costs for the business, whether directly or indirectly, resulting in increased profit.
Using Kanban In a Pull System
The signals which permit production materials to be replaced or refilled are called Kanbans. Meaning "signal" in Japanese, these cues use visual communication to put a pull system into practice. A Kanban will be placed where products or manufacturing components are stored and will signal when these need to be replenished. With this process, items needed are always available and will not be replenished without a signal from further down the production process.
Kanban signals can come in many forms. Kanban cards are the most common type of signal. These cards are sent to a previous step in the manufacturing process to indicate that more products or parts are needed. However, a Kanban can be as simple as an empty container that a worker can see needs to be refilled. The Kanban will provide the worker with information for replenishing the items such as the reorder quantity and part numbers.
Kanban signals provide an effective way to implement a pull system, which will lead to an overall more organized, efficient and profitable business. Manufacturing facilities currently using a push system should evaluate their supply chain for waste and consider switching to a pull system to experience a leaner manufacturing process.
Related Resources
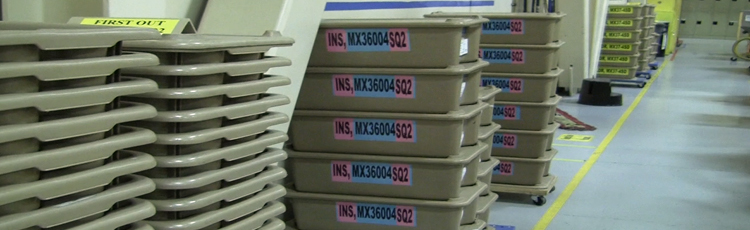
Start a Workplace Kanban Board
Efficiency is a necessity in business and life. Increasing efficiency saves time and money, which in turn ...
Read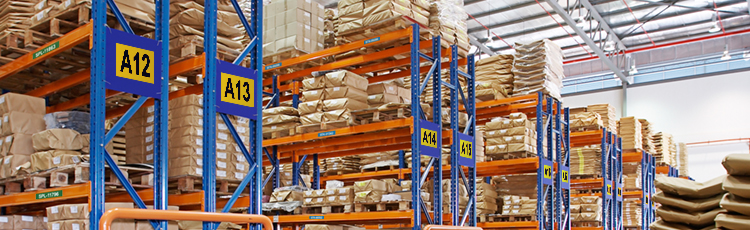
Warehouse Management
The global market is increasingly pressuring businesses to improve the efficiency of their operations. ...
Read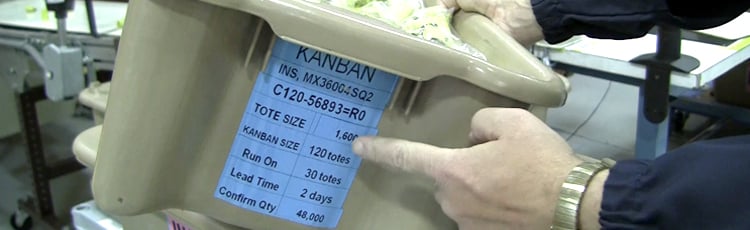
Kanban Benefits
Kanban Provides a Number of Benefits. Kanban was developed as a method for controlling the flow of materials ...
Read