Lean Construction
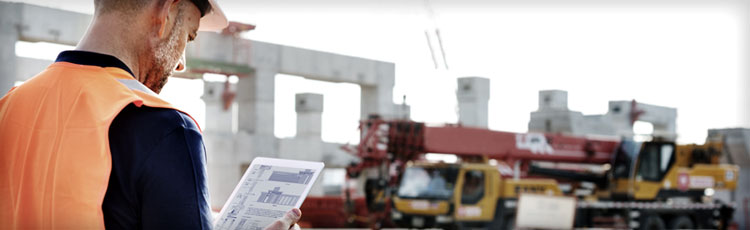
What is Lean Construction?
A term that is coming into common use is "lean construction." Lean construction takes the principles of lean manufacturing and applies them to construction projects.
Lean construction applies the principles of lean manufacturing to building projects, helping teams improve workflows, reduce waste, and deliver value efficiently. Unlike manufacturing, construction is complex and variable—requiring lean tools like Kanban, continuous improvement, and visual communication to optimize both planning and execution across job sites
How Lean Construction Differs from Manufacturing
Lean construction and lean manufacturing are not the same. Manufacturing typically involves designing, building and delivering a standardized product. Construction involves designing, building, and delivering unique, customized projects. Will lean manufacturing focuses on creating standards for a repetitive process, lean construction needs to get the waste out of a process that is interactive and unique for each situation.
Construction projects typically are managed by breaking the project into smaller tasks, monitoring those against their schedule and budget, and managing the critical path tasks such that they do not fall behind schedule. The focus is on individual activities.
Although lean construction has the same goal as lean manufacturing, that of eliminating waste, the approach is different. With construction projects activities are unique and dependent on other activities. In a paper titled "What Is Lean Construction", Gregory A. Howell describes what needs to be done in lean construction:
Managing the interaction between activities, the combined effects of dependence and
variation, is essential if we are to deliver projects in the shortest time. Minimizing the combined effects of dependence and variation becomes a central issue for the planning and control system as project duration is reduced and the complexity increases. (Complexity is defined by the number of pieces or activities that can interact.) The need to improve reliability in complex and quick circumstances is obvious. New forms of planning and control are required.
Lean construction is a different way of thinking that needs to exist throughout an organization. It involves not only project execution, but the total end-to-end project design and project process, including proposals, managing subcontractors, and cleanup (salvaging and recycling). The objective is to design and manage a project so as to reduce variation in work flow, with the ultimate goal of increasing value to the customer and reducing waste.
Lean Construction Planning & Workflow Design
Lean construction starts with the design process. The project and the construction process are designed together, with the goal of optimizing customer value. In addition to designing to meet the specification for the facility or equipment being constructed, the design takes into account maximizing the performance of construction based on having identified what the customer values.
A key to success is planning. Planning for lean construction begins during the project design. Then as the work progresses, the performance of planning is crucial to having reliable work flow, minimizing variations, and reducing waste.
An example of planning is the timing and size of deliveries from fabricators. The principles of Kanban are applied to "pull" work and materials through the project. The objective is to:
- Manage the interfaces between the various steps in the project.
- Don't have materials or components delivered until they are needed.
- Don't make anything until it is needed.
- Minimize the movement and handling of materials and components.
Example: Direct Delivery vs Laydown Area
Let's say that large components are delivered by truck. If delivered to the site when needed, the truck drivers end up waiting about 60 minutes for their load to be hoisted into place on the project. On the other hand, if they had delivered their load to a lay-down area the previous week, the components are on-site and ready to be hoisted into place when needed. The driver waiting time is eliminated.
However, consider the cost involved with using a lay-down area. The truck delivers the component to a lay-down area. They lay-down area requires a crane and a crew to unload the truck. It also may require protecting the components from weather, providing a structure to support the components (so they are not directly on the ground), and possibly even building the lay-down area. If it takes 20 minutes to unload the truck, then when the component is needed another 20 minutes to load it on another truck to move it into position, the man-hours and costs of using the lay-down area will exceed those of directly delivering the component when it is needed, even if the truck driver must wait for an hour for the component to be hoisted into position.
Quality Work in Lean Construction
Quality work, getting it right the first time, is key to lean construction success. Having to do re-work is obvious waste. It is essential to have quality in all areas of the project. This means:
- Designing and operating the right processes.
- Having the right equipment and resources, when they are needed.
- Delivering things right the first time.
- Working in the proper sequence.
- Having people with the right skills and doing work properly.
Identifying Waste in Construction Projects
Eliminating waste is what lean is all about. In traditional lean there are seven types of wastes that are identified:
- Transport (moving materials and objects that are not required to perform the current work)
- Inventory (anything that is not required for the current work)
- Motion (people or equipment moving more than required)
- Waiting (waiting or interruptions)
- During shift changes
- Waiting for tools
- As a result of broken equipment
- Waiting for materials
- Overproduction (doing work before it needs to be done)
- Over Processing (doing more work than is required for a task ? this can result from poor design)
- Defects (eliminate the possibility of defects, and that also eliminates the need for inspections and for rework)
A common difficulty with lean construction is that needed changes cannot easily be identified. That's because lean construction requires a new way of thinking. For example, take the last item on the above list, "defects." If the need for inspections can be eliminated, then we have eliminated some waste. But, inspections are need to catch defects and ensure the customer receives the expected quality. That means inspections are essential. But, that's not always true.
Some inspections are always going to be necessary. For example, welds on pressure vessels need to be x-rayed to check for defects. However, in other areas the construction process could be designed such that quality inspections are not required, because the work methods assures the work is done correctly. An example of this is a lean technique called poke-yoke.
Poke-yoke means to mistake-proof. For example, a three-prong electrical plug will only go into the socket one way. This means a mistake cannot be made: the electrical plug will always be inserted correctly into the socket. In their research paper "Potential Of Poka-Yoke Devices To Reduce Variability In Construction", Santos and Powel list the main types of mistakes, and present some alternatives that could mitigate them:
- Forgetfulness: alerting operator in advance or checking at regular intervals
- Errors due to misunderstanding: training, checking in advance, standardizing work procedures
- Errors in identification: training, attentiveness, vigilance
- Error made by amateurs: skill building work standardization
- Willful errors: basic education and experience
- Inadvertent errors: attentiveness, discipline, work standardization
- Errors due to slowness: skill building, work standardization
- Errors due to lack of standards: work standardization, work instruction
- Surprise errors: total productive maintenance, work standardization
- Intentional errors: fundamental education, discipline
Visual Communication in Lean Construction
Lean tools use visual communication. This means using color, shapes, symbols, pictograms, and text to deliver needed information. Visual communication includes an OSHA required safety sign, traffic control signs, or magnetic labels used on a Kanban board in an office. Whatever is needed, DuraLabel can deliver. By having a DuraLabel® Industrial Sign and Label Systems on-site you'll be able to make needed signs, labels, and tags any time and any where they are needed.
Take Action Today
Want to learn how to apply Lean construction in your facility? Call us today at 1-888-788-9936. One of our experts will help you integrate Lean construction into your workflow using proven Lean strategies and DuraLabel printers and tough-tested supplies. Be sure to ask about the special money-saving DuraLabel kits.
Related Resources
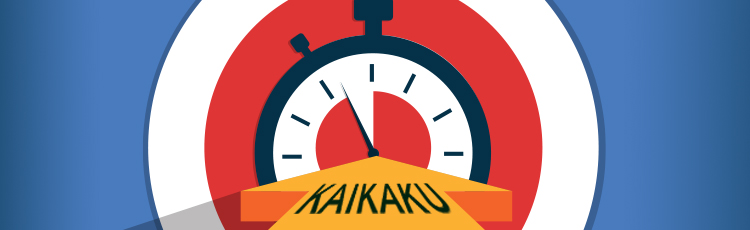
Kaikaku: Driving Radical Change in Lean Systems
What Is Kaikaku and How Does It Support Lean Transformation? Kaikaku is the Japanese word for "radical ...
Read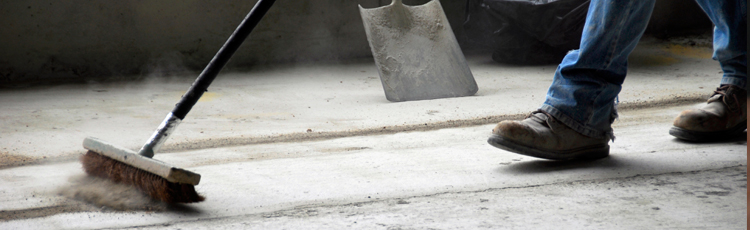
Lean on Maintenance
What is Lean Maintenance? Lean manufacturing is arguably the single greatest advance in plant efficiency ...
Read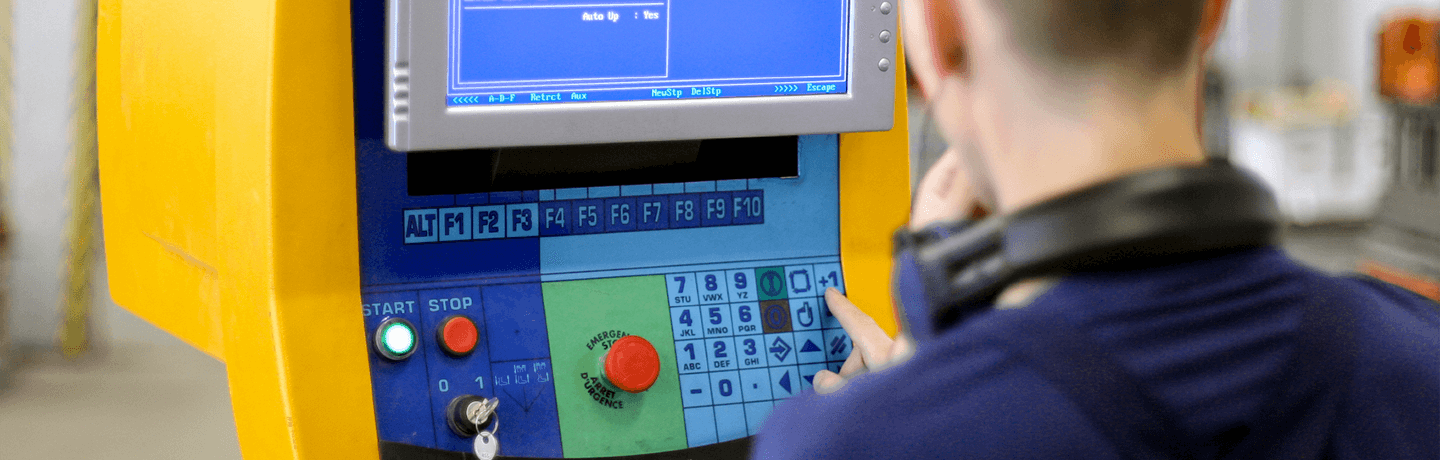
Six Sigma Principles: Exploring Six Sigma, Lean, and The 5S System
What is Six Sigma? Six Sigma is a systematic approach to eliminating errors that harmonizes with 5S and 5S ...
Read