How to Build a 5S Implementation Team for Lean Success
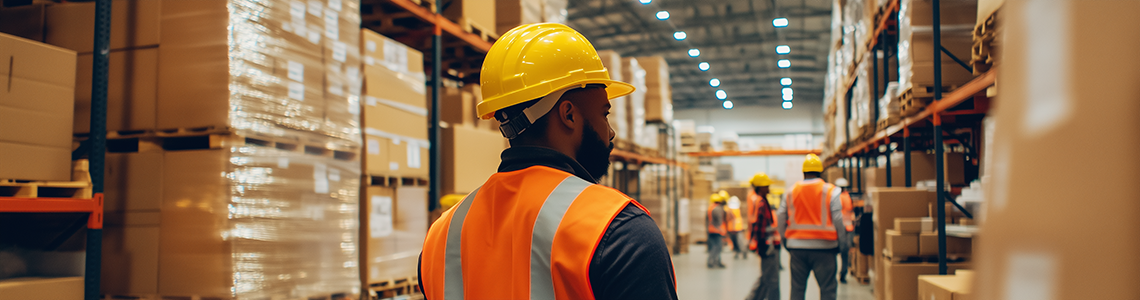
What is a 5S Implementation Team?
A 5S implementation team is a group of individuals empowered to make quick decisions and take actions that benefit their company. These teams drive process improvement by applying lean manufacturing principles.
Lean manufacturing has changed the shape of businesses, improving processes for the better. 5S implementation teams, or lean teams, enable companies to facilitate positive change in the workplace and respond to problems in a timely manner. Strictly speaking, a 5S implementation team is a group of individuals empowered to make quick decisions and take actions that benefit their company.
Benefits of a 5S Team
Implementing a 5S team in your facility offers countless benefits that can enhance your workplace's efficiency, safety, and productivity. Forming a 5S team allows you to focus on key strategies for workplace organization and improvement. Here are some advantages to consider:
- Increased Efficiency: A 5S implementation team organizes the workplace to reduce unnecessary clutter and streamline processes. This results in a more efficient lean manufacturing workflow where employees can easily find tools and materials, reducing downtime and increasing productivity.
- Improved Safety: By organizing and maintaining a clean work environment, team dynamics in 5S play a crucial role in identifying and removing potential hazards. Clearly labeled and well-organized workspaces while adhering to OSHA signage requirements minimize the risk of accidents and injuries, promoting a safer visual factory for all employees.
- Reduced Waste: The 5S methodology, supported by strong leadership in 5S implementation, emphasizes waste elimination through better organization and standardization. This reduces excess inventory, unnecessary motion, and overproduction, resulting in cost savings and a stronger bottom line.
- Consistent Quality: Standardized processes and organized workstations allow a 5S implementation team to maintain high levels of consistency in production. This approach ensures fewer errors and higher quality in products and services.
- Sustained Discipline: Building a successful 5S process requires a team that instills continuous improvement and discipline. Regular audits and adherence to lean principles encourage employees to uphold these standards, driving long-term organizational success.
- Better Utilization of Space: A 5S team’s roles and responsibilities often include optimizing the workspace layout. This frees up valuable floor space, enabling better movement, storage, and overall utilization of the facility.
By forming a 5S team, your organization can improve efficiency, safety, and overall employee satisfaction. A well-executed 5S system contributes significantly to the long-term success of your workplace.
For instance, Toyota famously improved their operational efficiency by forming dedicated 5S teams, resulting in approximately 10% reduction in overall assembly time (Harvard Business Review, 1999).
Developing a 5S Implementation Team
Creating an effective lean team organization requires businesses to define and form teams around their current processes. For these teams to be effective, they must be comprised of workers from each relevant department and be empowered to make 5S process improvements.
Forming the Team
Once the various processes have been defined, it's time to create teams that focus on improving individual processes through the 5S methodology. This involves forming a 5S team that does not solely consist of workers from the same department. Consider, for example, an engineering, procurement, and construction (EPC) company. The EPC's current proposal process frequently results in bids that are overpriced (causing the company to lose the bid) or underpriced (reducing the company's revenue).
The current problems may stem from poor communication among the stakeholders involved in the proposal process. A properly developed 5S implementation team could improve communication and foster positive change by including individuals from each department involved in the proposal process. This approach supports team dynamics in 5S, creating a smoother process that drives better results. Instead of making changes based on a single perspective (that of the proposal group), changes would address the "entire" proposal process, which could involve:
- Purchasing
- Engineering
- Project management
- Logistics
- The field service team
By forming a 5S team with members from each relevant department, the team can effectively identify problems and develop targeted solutions that improve their assigned 5S process and visual factory.
Empowering the Team Based on Lean Principles
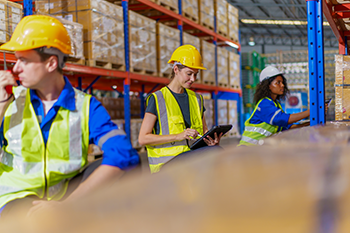
Traditional business structure often results in a vertical power dynamic that limits input from employees, making timely process improvements challenging. Forming a 5S team addresses this issue by empowering each group to make decisions and facilitate change. Clearly defining 5S roles and responsibilities, as well as outlining methods for improving processes, is essential. Each team must have the authority to implement reasonable changes without navigating the entire command structure.
Ravenswood Family Health Center, guided by effective leadership in 5S implementation, significantly improved team collaboration and reduced patient wait times through cross-departmental 5S teams (California Health Care Foundation, 2015).
5S Team Hierarchy
Lean teams function in a hierarchy that involves all levels of the organization. A group leader facilitates communication and improvements in lean and sustainable manufacturing across multiple teams. Each team has a leader responsible for implementing improvements aligned with lean principles and gaining approval from the group leader. Individual team members focus on identifying and solving problems in their assigned areas. Solutions aligned with 5S principles are collaboratively developed by team members and their leader before implementation.
A critical aspect of a 5S implementation team is that each group is empowered to make improvements within its scope of responsibility. For changes affecting multiple groups, group leaders escalate the idea to upper management for approval and support. This structure ensures that teams have the autonomy to drive change, giving the lean program the momentum needed to succeed.
Implementing a 5S Team
Creating a successful 5S process requires full commitment across the organization, from executives to workers. Everyone must embrace positive change, with management providing support to enable improvements. Managers must shift from traditional roles to become leaders and facilitators of change, while team members focus on continuous process improvement based on lean principles.
Though changing workplace culture can be challenging, lean manufacturing tools like Kaizen, 5 Whys, and Plan-Do-Check-Act (PDCA) support this transition. These tools, combined with a well-structured 5S team, help organizations achieve long-lasting improvements.
DuraLabel 5S Implementation Team Solutions
Having a 5S implementation team create a visual factory with durable signs and labels is one step a facility can take to take advantage of the 5S methodology. DuraLabel offers premade and custom signage solutions to create an organized and safe visual factory. Enhance your worksite with the DuraLabel Kodiak Max 5S Kit. The kit includes the DuraLabel Kodiak Max Industrial Sign and Label Print System and premium vinyl and ribbons, making it the ideal solution for implementing a 5S system in your facility.
Developing a lean team requires a lot of preparation and training. Use our free 5S Quick Start Guide to educate your staff on the 5S methodology.
Read Next:
Related Resources
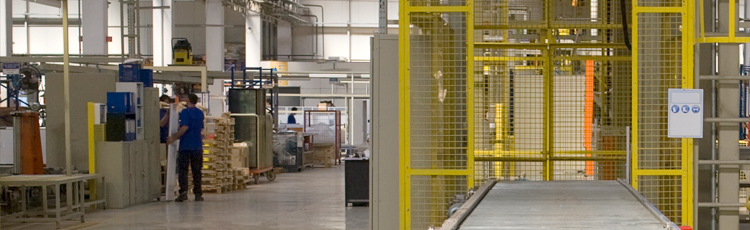
Understanding the 5 Lean Tools: Kaizen, 5S, and More
Five of the Most Helpful Lean Tools from 5S to Focus PDCA Lean manufacturing uses many lean management tools ...
Read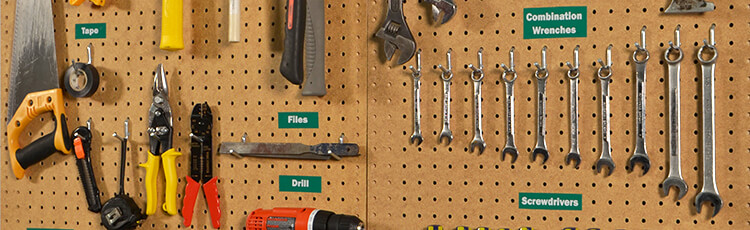
Tools for 5S Lean Manufacturing
The 5S systemis a lean manufacturing tool that helps to clean and organize the workplace, as well as improve ...
Read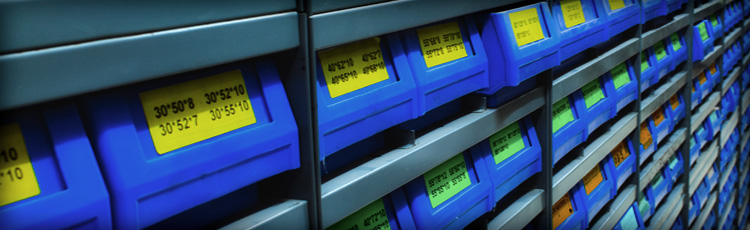
Creating a Visual Factory with the 5S System
What Is a Visual Factory with the 5S System? The term "visual factory" refers to an approach to lean ...
Read