Tools for 5S Lean Manufacturing
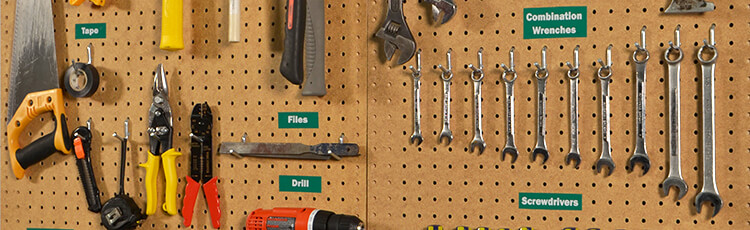
The 5S system is a lean manufacturing tool that helps to clean and organize the workplace, as well as improve how things are done through standardization. This can be accomplished with the five following steps:
- Sort: Remove unneeded and obsolete items from the workplace.
- Set in Order: Organize each area in the workplace based on how work is done.
- Shine: Clean your workplace, tools, and equipment to restore them to their original condition.
- Standardize: Improve how work is done by creating procedures that ensure work is done consistently and efficiently.
- Sustain: Make 5S part of your daily routine by repeating each step on a daily basis.
While these steps are clear and can be implemented without major upfront costs, there are some helpful tools for 5S lean manufacturing that can make the process easier. These include both physical and digital resources, such as productivity tools for 5S, lean tools for workplace organization, and visual factory tools, in addition to 5S checklists, and visual communication tools like labeling and floor marking supplies.
Process Tools
There are numerous process tools that can help make implementing 5S successful, including Plan-Do-Check-Act (PDCA) and 5 Whys. These 5S Lean Manufacturing tools are essential components for 5S implementation, driving continuous process improvement. and allowing any facility to make sure they are meeting Occupational Safety and Health Administration (OSHA) requirements for signs and labels throughout the area.
Plan-Do-Check-Act
PDCA is an organized approach to problem-solving. This helpful tool can help make your 5S implementation more meaningful by ensuring improvements, from Sort to Standardize, address issues in your workplace. PDCA includes four important steps:
Plan: In this first step, workers identify an area that needs improvement then they develop a plan with workers from other areas that may be affected by any change.
Do: Implement the plan in a pilot area so it does not disrupt the workplace. Keep track of what has been done and its impact.
Check: Review the change and its impact. Did the change yield the expected results? Did it impact any areas or processes that were not supposed to be affected?
Act: If the change yields an improvement, begin incorporating it throughout the business-one area at a time. If the improvement does not work in other areas, restart at the Plan phase for those areas.
PDCA is a powerful counterpart of the 5S system because it ensures that each step in the 5S process is applied to address specific problems. Workers won't simply begin removing tools and organizing equipment without first creating a plan to ensure the change will be positive. Each change will help make work easier, reduce costs, and improve quality throughout the workplace.
The 5 Whys
The Five Whys analysis is also known as the why-why chart and root cause analysis. As these names imply, the purpose is to find the true root cause of a problem. The technique can very well be used in connection with a cause-and-effect chart to analyze each identified cause to ensure that it really is the root cause of the problem and not only a symptom of another and more deeply rooted cause. This can in fact be compared to peeling an onion, where each layer is removed to reveal another layer, until the center of the onion is reached.
The Five Whys is a question asking technique for identifying the root cause of a problem. It involves asking the question "why" as many times as necessary to identify the root cause. It's called "Five Whys" because it typically requires asking "why?" at least five or more times.
The answer to the last "why" question normally points out where the main problem is. For example, many times the root cause investigation will stop when an answer such as, "it was out of my control," or "there were not enough hours available," is heard. But, this is not the root cause. The Five Whys process needs to continue with a question such as, "Why were there insufficient hours available?"
The 5 Whys Process
A problem has been identified and you want to find the root cause. How is Five Whys applied?
- Start by going to the location where the problem exists. In lean terms this is called Gemba. By physically going to the location of the problem you can observe the situation yourself, and talk directly with those who know the most about what is happening.
- Write the definition of the problem at the top of a sheet of paper. Then ask the question, "Why is this problem taking place?"
- Write down the answer(s) you get. For each answer ask "why" again, until the answer identifies a root cause. If you get multiple answers to a "why" question, treat each one as a separate branch to follow, asking "Why?" until a root cause is identified for each one.
- There may be multiple root causes, or cascading root causes. Be sure to ask "why" a sufficient number of times to identify all potential root causes.
5S Checklists
In addition to process tools, you will need other lean management tools to help support your 5S system. These tools include checklists and charts. Some common checklists that can help keep your program focused include:
5S Audit Checklists: An audit checklist can help keep your program on task by making it easy to track improvements and areas that can use additional improvements. Each department should make its own checklist to best meet its needs.
Trend Charts: These charts show trends in data over time. Trend charts help managers keep track of changes in processes, outputs, and much more. These charts can help you quickly identify areas or processes that need to be improved, as well as processes that will need to be improved in the future.
Preventive Maintenance Checklists: Preventive maintenance is what keeps operations running smoothly without excessive downtime. Using a preventive maintenance checklist ensures that maintenance is done on time and new maintenance requirements are addressed.
DuraLabel 5S Solutions
A successful 5S program requires effective visual communication, which includes the following:
- Labels for storage bins, shelving, and tools will help workers identify items and put them back where they belong.
- Procedure labels can communicate procedural changes and help workers complete tasks correctly, every time.
Support your 5S program with clear, effective visual communication. Make sure your facility is properly implementing the 5S system with the DuraLabel Kodiak Max 5S Kit. This kit comes with all the supplies you need to closely follow 5S. The DuraLabel Kodiak Max Industrial Sign and Label Print System, included in the kit, creates high-quality 5S signs and labels that keep a business operating efficiently.
Not sure how to apply 5S to your facility? Download the in-depth, free 5S Quick Start Guide. This quick guide is designed to help you build a 5S system that works for your environment. You can also call one of our specialists at 1-888-342-3164 and they can help you get started.
Read Next:
Understanding the 5 Lean Tools: Kaizen, 5S, and More
Creating a Visual Factory with the 5S System
Related Resources
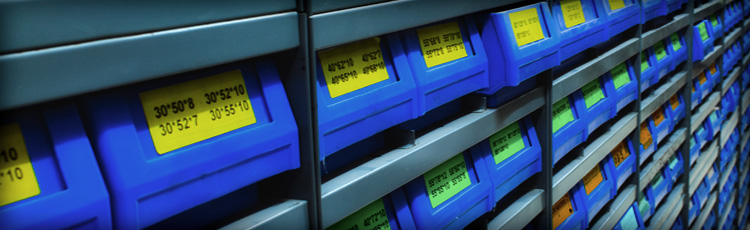
Creating a Visual Factory with the 5S System
What Is a Visual Factory with the 5S System? The term "visual factory" refers to an approach to lean ...
Read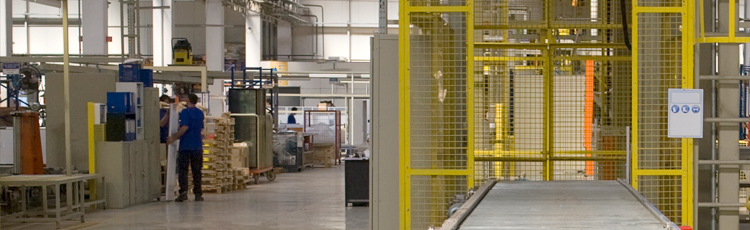
Understanding the 5 Lean Tools: Kaizen, 5S, and More
Five of the Most Helpful Lean Tools from 5S to Focus PDCA Lean manufacturing uses many lean management tools ...
Read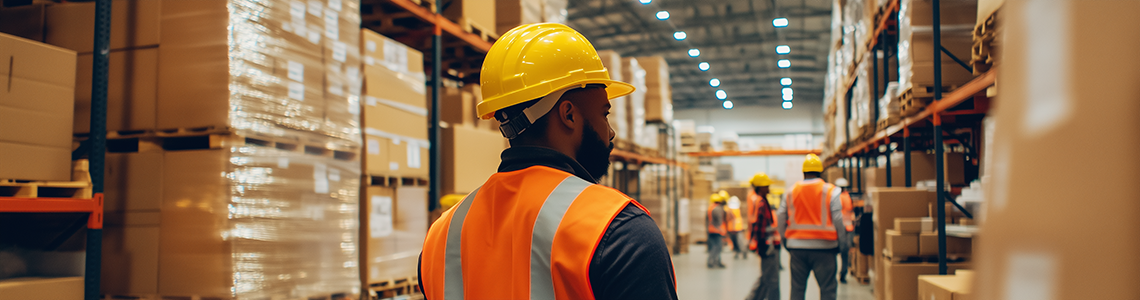
How to Build a 5S Implementation Team for Lean Success
What is a 5S Implementation Team? A 5S implementation team is a group of individuals empowered to make quick ...
Read