Lockout/Tagout (LO/TO) Procedures
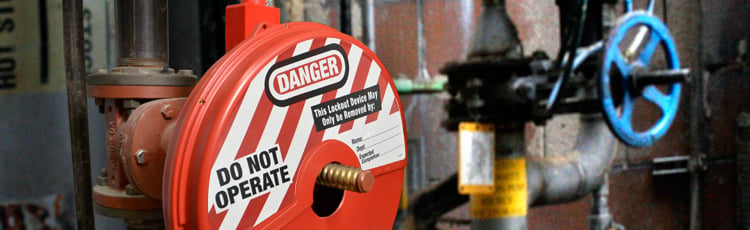
OSHA's requirements for the control of hazardous energy (typically called lockout/tagout, or LO/TO) are found in 29 CFR 1910.147. These rules require specific written lockout tagout procedures to be created for a facility, providing detailed, step-by-step instructions that can be followed and reviewed.
When Energy Control Procedures are Required
OSHA requires that specific procedures for the control of potentially hazardous energy be developed, documented, and used. The requirement comes into play whenever the unexpected startup of the equipment being serviced, or the unexpected release of energy from it, could harm employees. In general, new written lockout tagout procedures need to be developed for each type of machine or equipment.
However, some situations are simple enough that specialized, written lockout/tagout procedures aren't necessary. For example, the LO/TO rules do not apply to work on "cord and plug connected electric equipment," such as handheld power tools, as long as the person performing the work can unplug the equipment, retain control of the plug for the duration of the work, and be effectively protected by those steps.
For larger equipment, OSHA allows an exception to the procedural requirements when all of the following conditions are met:
- There is no danger to people from stored, residual, or re-accumulated energy after the equipment is shut down.
- The equipment has only a single energy source, which can be readily identified and isolated.
- The isolation and locking out of that energy source will completely de-energize and deactivate the equipment.
- A single lockout device will achieve a locked-out condition.
- The equipment is isolated from the energy source and locked out during servicing or maintenance.
- The lockout device remains under the exclusive control of the authorized employee who is performing the servicing or maintenance.
- Servicing or maintenance does not create hazards for other employees.
- The employer, in utilizing this exception, has had no accidents in the past involving the unexpected activation or re-energization of the equipment during servicing or maintenance.
If any of those conditions are not met, the exception does not apply, and a LO/TO procedure needs to be created for the equipment.
Lockout/Tagout Procedure Template
Let's say you need a LO/TO procedure, and you don't already have one to work from. Where do you start? The easiest way is to use a template that includes the basics and fill in the details. You can also grab our free lockout tagout guide to help explain what is needed or see a visual presentation of this basic procedure.
This template is based on OSHA's example in 29 CFR 1910.147, Appendix A. It describes a basic lockout procedure, and can be modified and filled in for use as a lockout procedure in your facility.
Lockout/Tagout Procedure for (Company Name/Equipment)
A. Purpose
This procedure establishes the minimum requirements for lockout/tagout (LO/TO) on equipment that is being serviced or maintained. This procedure must be followed in order to properly stop equipment, disconnect it from any sources of potentially hazardous energy, and prevent those sources from being reconnected during the work. Where service or maintenance work could expose employees to a risk of injury from the unexpected start-up or energization of equipment, or the release of stored energy, this procedure must be followed.
B. Compliance with this Program
Each employee is required to comply with the restrictions placed on them by this procedure. Specifically:
Authorized employees are required to perform the lockout or tagout in accordance with this procedure, and to remove their lock(s) or tag(s) at the end of the service or maintenance, as required by the procedure.
Affected and other employees, upon observing that a machine or piece of equipment is locked out, must not attempt to start, energize, or use that machine or equipment, or attempt to defeat or remove the lock(s) or tag(s).
Violation of these rules will result in disciplinary action, which may include immediate termination of employment.
C. Sequence for Applying Lockout/Tagout
These steps must be followed by authorized employees to create a locked-out or tagged-out condition.
- Notify all affected employees that service or maintenance is required on the equipment and that the equipment must be shut down and locked out to perform the necessary operations.
- Identify the type(s) and magnitude(s) of the energy that the machine or equipment uses, understand the hazard(s) of that energy, and identify the method(s) that will be used to control that energy.
- If the machine or equipment is operating, shut it down by the normal stopping procedure (press the "stop" button, etc.).
- Operate the energy-isolating device(s) so that the machine or equipment is isolated from its energy source(s) (move the electrical power switch to its "open" position, close the supply valve, etc.).
- Apply your assigned individual lockout/tagout device(s) to each energy-isolating device, holding the isolating device(s) in the disconnected, inactive, or safe position.
- Dissipate ("bleed off") or restraint ("block") any stored or residual energy (such as that in capacitors, springs, elevated machine parts, rotating flywheels, hydraulic or pneumatic systems, etc.) by appropriate methods (such as grounding, repositioning, opening release valves, etc.).
- Confirm that the equipment is completely disconnected from its energy source(s). First, check that no employees are exposed; then, verify the isolation of the equipment by operating the normal operating control(s), or by testing to make certain the equipment will not operate. Return all operating control(s) to their neutral or "off" positions after verifying the isolation of the equipment.
- The machine or equipment is now locked out. Service or maintenance may begin.
D. Sequence for Removing Lockout/Tagout
These steps must be followed by authorized employees when the servicing or maintenance is completed, and the equipment is ready to return to normal operation.
- Check the equipment and its immediate area to ensure that nonessential items, tools, and parts have been removed and that the equipment components are operationally intact.
- Check the work area to ensure that all employees have been safely positioned or removed from the area.
- Verify that all controls are in their neutral or "off" positions.
- Remove your assigned individual lockout or tagout device(s), and reenergize the equipment. Some forms of blocking may require reenergization of the equipment before safe removal.
- Notify affected employees that the servicing or maintenance is completed and the machine or equipment is ready for use.
Using Tagout for a Lockable Device
When locks can be applied as part of a lockout/tagout process, they offer a degree of security that an informative tag simply can't provide. LO/TO best practices is to use locks whenever possible. However, some situations may call for the use of tags instead of locks even when a lock could be applied. Because this could lead to confusion and increased danger, OSHA has specific rules for these situations.
If an energy isolating device is lockable, but tagout is used instead, the tags must be attached at the same place where a lock would have been attached. Employees also need to receive additional training about the limitations of a tagout program, as opposed to the more secure lockout approach, and the procedure for using those tags needs to have more rigorous periodic inspections.
The employer is responsible for demonstrating that the chosen tagout approach provides equivalent safety, in comparison to a more secure lockout approach. This may include adding more steps to the LO/TO process, such as removing circuit elements, blocking control switches, and removing valve handles, to prevent unintended or unauthorized startup. Any such steps need to be noted in the written procedures.
Tools for Lockout/Tagout
For a lockout/tagout program to succeed, all of the tools required by a procedure need to be provided. These typically include standardized locks and tags, and may include more specialized equipment like valve covers or multi-lock hasps.
Signs and labels can also contribute to a LO/TO program. For example, lockout points and controls can be identified with a custom label. The complete procedure for locking out a machine can even be posted right on the equipment, ensuring that no steps are forgotten. The DuraLabel line of industrial label and sign printers can offer an easy way to create these labels on-site and on-demand.
Related Resources
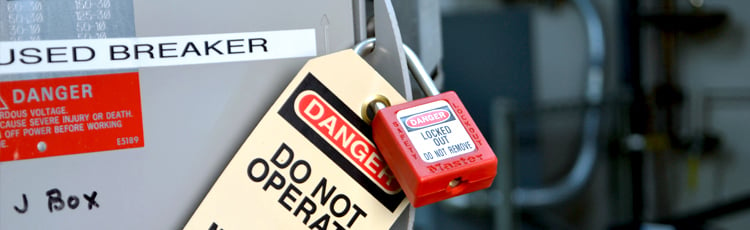
Lockout Tagout (LO/TO) Program
The numbers are staggering: Lockout-Tagout (LOTO) violations are consistently among OSHA's 10 most common ...
Read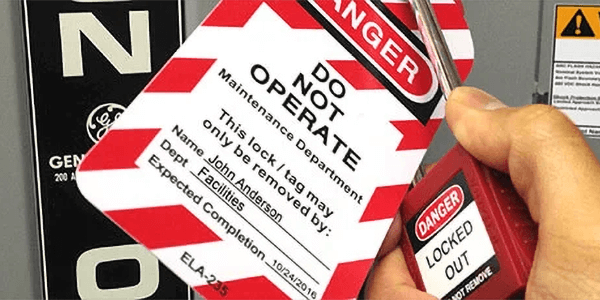
How to Prevent Arc Flash with Lockout Tagout Signs and Safety Labels
What Are the First Steps to Preventing Arc Flash in the Workplace? In the realm of electrical safety, the ...
Read
Arc Flash Accident Reports
An arc flash is dangerous and has the potential for causing serious injuries. It typically occurs suddenly ...
Read