How to Prevent Arc Flash with Lockout Tagout Signs and Safety Labels
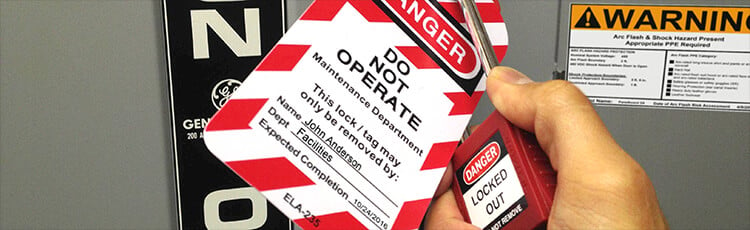
What Are the First Steps to Preventing Arc Flash in the Workplace?
In the realm of electrical safety, the risks posed by arc flash incidents loom large, presenting potentially catastrophic consequences for both workers and facilities. However, with the implementation of robust safety measures—like Lockout/Tagout (LOTO) procedures and clear lockout tagout signs—organizations can significantly reduce the chance of injury or death. Learning how to prevent arc flash starts with proper hazard communication and strict energy control practices.
Recognizing Electrical Hazards That Lead to Arc Flash Incidents
An arc flash can release a deadly blast of energy without warning, making it one of the most dangerous hazards in electrical work. The resulting arc blast can cause devastating injuries and extensive damage to equipment, facilities, and electrical panels, emphasizing the need for proactive safety programs.
Arc flashes can be trigged by dropping a tool, opening a panel on degraded equipment, or even pest infestations. There is one controllable factor that unites all arc flash incidents, and that is electrical power. According to the latest data from the Electrical Safety Foundation International (ESFI), exposure to electricity continues to pose a significant risk across multiple industries. From 2011 to 2023, the numbers show a consistent—and alarming—trend::
- 1,940 electrical fatalities; 1,432 were in non-electrical roles.
- Electricians (212) and laborers (273) saw the highest death counts.
- 3,260 non-fatal electrical injuries involving days away from work in 2021 and 2022 (combined).
The industry standard for safe electrical work (NFPA 70E) recommends eliminating the risk of arc flash when working on electrical equipment: shut it off and lock it out.
Using Lockout Tagout Signs to Support an Electrically Safe Work Condition
That’s the core principle behind the National Fire Protection Association's (NFPA’s concept of an “electrically safe work condition.” This status is required under either of these scenarios:
- A worker is inside the Limited Approach Boundary of live equipment.
- There is any risk of injury due to arc flash
In both situations, de-energizing the equipment is key. Once that’s done, clear lockout tagout signs and safety labels must be applied to communicate that the system is out of service and must not be restarted.
De-energizing is only one part of the solution, though. To prevent re-energization and ensure worker safety, an effective lockout/tagout system must be implemented.
Why De-Energizing Isn't Enough
Establishing an electrically safe work condition starts with powering down equipment—but that alone doesn't eliminate the risk. Without proper safeguards, machinery can be unintentionally re-energized by another worker, leading to a serious arc flash incident. That’s why visual communication plays a critical role.
Lockout tagout signs and safety labels serve as immediate, visible warnings to anyone near the equipment. These tools are essential for alerting others that maintenance is in progress and the equipment must remain off. When used in tandem with a verified lockout/tagout procedure, these signs help enforce the electrically safe state and prevent dangerous missteps.
LOTO Steps for Electrical Work
Lockout/tagout procedures for electrical systems follow the same four key steps:
- Identify all sources of energy
- Shut down the equipment and disconnect those power sources
- Apply locks and LOTO labels
- Verify full de-energization
In electrical work, this process includes additional precautions:
-
Notify affected employees before shutdown
-
Use testing tools to confirm absence of power
-
Apply grounding where necessary
-
Use compliant OSHA lockout tagout signs and labels
-
Verify locks and tags are correctly applied
The NFPA 70E standard outlines this process in detail, including an example LOTO procedure in Informative Annex G. When customized for your facility, these steps can prevent most arc flash incidents.
Rules for Arc Flash Safety and Labeling Compliance
While NFPA 70E offers detailed guidance, OSHA sets the enforceable legal baseline. Electrical work rules appear in 29 CFR 1910.333, with detailed lockout/tagout provisions in 29 CFR 1910.147.
OSHA also requires clear labeling of hazards on or near electrical panels. This includes both safety labels and signage, which must be durable, visible, and formatted according to OSHA standards.
Using the right industrial label system makes compliance easy. Labels that communicate voltage, PPE requirements, and equipment status help prevent unintentional energization. For long-term consistency, many facilities rely on LO/TO label software and preformatted templates built for industrial label creation for LO/TO procedures.
Why Safety Labels for Electrical Panels Are Key to Preventing Arc Flash
Knowing how to prevent arc flash starts with visibility. Workers who are not directly involved in a task still need to know where hazard zones begin. Clearly marked OSHA signs and safety labels for electrical panels are critical to setting boundaries and keeping unqualified personnel safe.
When energized work is necessary, qualified personnel need precise information—such as incident energy, required PPE, and shutdown status. This is where custom industrial labels make a difference.
DuraLabel Tools to Prevent Arc Flash in Facilities
Where electrical hazards exist in your facility, it's important to train the affected workers to understand those hazards and follow safe practices. Employees who aren't performing work on a given piece of powerful equipment should know about the equipment's "danger zones" and how far back to stay by viewing the appropriate OSHA signs and labels.
When work must be performed on energized equipment, your team needs a labeling system built for speed, accuracy, and compliance. The DuraLabel Kodiak Max Industrial Sign and Label System makes it easy to create detailed OSHA-compliant labels for electrical panels, arc flash zones, and PPE requirements—all from one powerful, high-volume printer designed for industrial environments.
The Kodiak Max comes pre-installed with LabelForge PRO Design Software, giving your team access to compliant templates, customizable label formats, and a complete library of electrical hazard symbols. With LabelForge PRO, creating OSHA-ready arc flash and lockout/tagout labels is fast, consistent, and easy to manage across departments.
Get help crafting a system that will provide the safety communication you need. Call 1-888-820-4631 and one of our experts will guide you through the process.
Want a clearer path to compliance? Download the free Arc Flash Labeling Quick Start Guide to learn how to apply arc flash labels correctly, meet OSHA and NFPA 70E requirements, and improve electrical safety across your facility.
Read Next:
Importance of Lockout/Tagout Training
Related Resources

OSHA and NFPA 70E
When workers performing maintenance or repairs on energized electrical equipment, they could be exposed to an ...
Read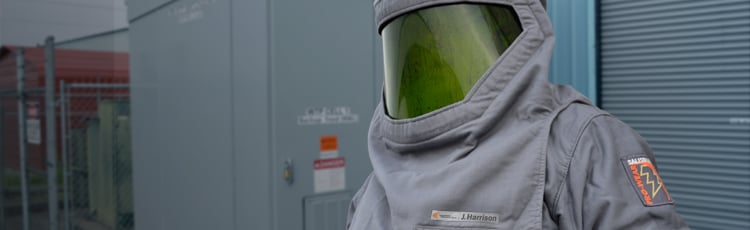
Arc Flash PPE
Personal Protective Equipment (PPE) is the last line of defense against injuries. When it comes to arc flash, ...
Read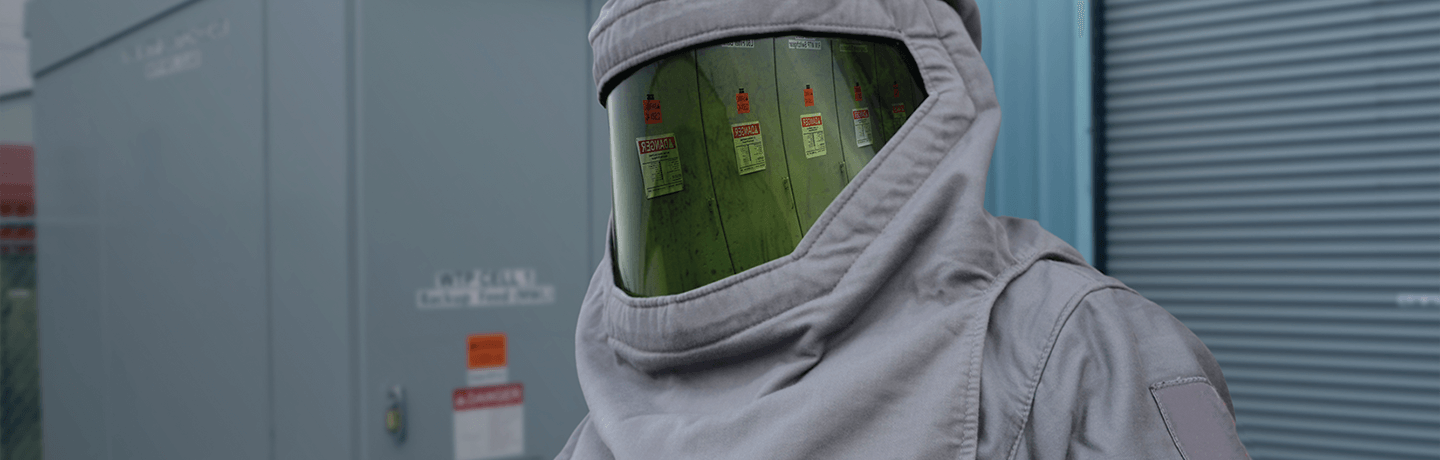
NFPA 70E Arc Flash with OSHA Signs
What is NFPA 70E? NFPA 70E, or the NFPA's Standard for Electrical Safety in the Workplace, outlines specific ...
Read