Maximize Safety on a Budget

Budget-Friendly Protection: Smart Tips to Maximize Safety Without Breaking the Bank
In order to implement any new plan, it often costs a pretty penny to create. Creating a safe environment for your employees should be a concern for many facility managers, but it does not need to cost an arm and a leg to maintain. How does one maximize their facility’s safety while being on a budget?
According to the National Safety Council reported that the average company spends:
- $1,100 per injured worker
- $1,310,000 per worker death
- $163.9 billion total for workplace injuries in 2020
An article in Training Magazine said companies spend an average of $1600 per employee on training. Mid-sized to large companies invest an average of 2-5% of their salary budgets on training their employees, according to a 2020 industry report.
OSHA offers several safety training courses for $60-$190 a course. The 10-hour class is intended to provide workers with awareness of common job-related safety and health hazards, while the 30-hour class is more appropriate for supervisors or workers with some safety responsibility. These types of courses are great options for the on-a-budget employer that won’t break the bank and a certificate of completion is given at the end of the course.
What Should a Safety Budget Include?
First things first, having a safety plan in place is the most important step before creating a budget. This is known as the three E’s and includes a workplace safety evaluation, education, and enforcement. Once the evaluation has been created, decide how much you will be able to spend. Here are four areas to focus on:
- Education and safety training— Education and training help inform workers about workplace hazards and provide effective methods to keep them safe and more productive. When employers invest in employee training, they are less likely to cause accidents. A cost effective way to save on training is to use online resources and free training materials from reputable organizations.
- Personal Protective Equipment (PPE ) training—Personal protective equipment is most effective when the wearer knows how to utilize it. The best way for workers to know how to use their equipment is through proper training. Safety professionals should run a risk assessment to identify hazards that would require the use of PPE. Here are some situations where PPE is required:
- Dangerous procedures
- Environmental hazards
- Chemical hazards
- Radiological hazards
- Mechanical irritants
Each type of PPE has its own features and certain rules should be followed when wearing them. PPE should be maintained cleanly and reliably. Before putting on a piece of equipment, it should be inspected to confirm it’s sanitary and in good working order. There are four types of PPE to be on the lookout for and here are the situations in which they should be used:
Eyes and face protection - This PPE protects your eyes and face from hazards such as chemical splashes and flying debris. Some examples of eye and face protection equipment include face shields, general safety glasses, laser safety glasses, chemical splash goggles, and impact goggles.
- Hand protection— This equipment is worn to protect workers' hands from sharp edges, rotary machinery, and chemical exposures. Some examples of hand protection are gloves, finger guards, and arm coverings.
- Body protection— This PPE is good for protecting workers from bloodborne pathogens. It comes in a variety of different materials suitable for various hazards. Coveralls, splash suits, and surgical gowns are all examples of body protection PPE.
- Respiratory protection— This PPE protects wearers from inhaling hazardous substances. Respiratory Protective Equipment (RPE) is divided into two types:
- Respirators—a mask
- Breathing apparatuses—a ventilator
- External consulting— Safety Consultants can be a cost-saving alternative to training. Many of these consultants offer OSHA training on-site, perform site audits, and solutions to safety challenges. The goal is to develop a strong safety plan to prevent accidents and promote a healthy safety culture. OSHA even offers free, on-site consulting to many employers.
- Signage— Safety signage is important as it makes people aware of the potential risks for the environment they are in. The color, shape, and design of the signs are intentional and intended to engage its viewers to act. Clearly mark hazardous areas and provide safety instructions using affordable signage. Ensure that emergency exits, fire extinguishers, and first aid stations are well-labeled.
Stretching the Budget
Maximizing workplace safety on a budget requires creativity, resourcefulness, and a commitment to prioritize safety. Here are some tricks to help you achieve this goal:
- Safety committees— Establish a safety committee with representatives from different departments. This group can identify potential hazards and suggest cost-effective solutions.
- Regular safety inspections—Conduct regular safety inspections to identify and address potential hazards before they become serious issues. Encourage employees to report safety concerns promptly.
- Emergency response plans—Develop and regularly review emergency response plans. Ensure all employees are familiar with evacuation routes and emergency procedures. Conduct drills to practice responses to different types of emergencies.
- Benchmarking and networking— Connect with other businesses or industries facing similar budget constraints. Share ideas, best practices, and lessons learned. Attend workshops, webinars, or local safety events for insights into cost-effective safety measures.
- Utilize Technology—Explore affordable safety technology solutions, such as apps for reporting hazards, monitoring equipment, or providing safety alerts. Leverage free or low-cost safety apps and software.
- Review and improve—Regularly review safety practices and incident reports. Learn from near-misses and accidents to continually improve safety measures. Allocate resources to address the most critical safety concerns first.
By combining these strategies, you can enhance workplace safety without breaking the bank. Remember that a proactive and engaged approach to safety is key to preventing accidents and creating a secure work environment.
DuraLabel Resources
Training employees how to be safe should not have to break the bank, but it is an investment. Invest in the success of your employees by helping them remain safe while performing their daily job duties.
Combining different safety strategies helps employers and workers evaluate the safety of their workplace, understand industry hazards, and implement worker protections to reduce and eliminate hazards.
DuraLabel's free OSHA Safety Signs Instant Action Guide helps you create OSHA/ANSI compliant safety signs. The guide helps readers understand the regulations and standards and improve safety and efficiency. Request your free OSHA Safety Signs Instant Action Guide.
Want to learn how to implement floor marking with all your industrial label needs? Download a free copy of the Floor Marking Instant Action Guide. Give us a call today at 1-888-902-2148 and one of our experts will guide you through the process.
Read Next:
From Fear to Empowerment: How OSHA's Free Consultation Transforms Workplace Safety
Related Resources
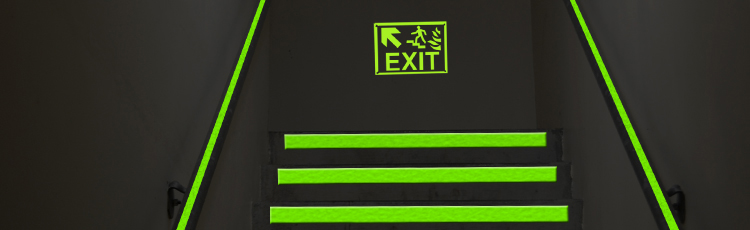
Plan Ahead: Enhance Emergency Safety
Accidents will happen, and so can emergencies. As equipment and processes change, it's important to keep ...
Read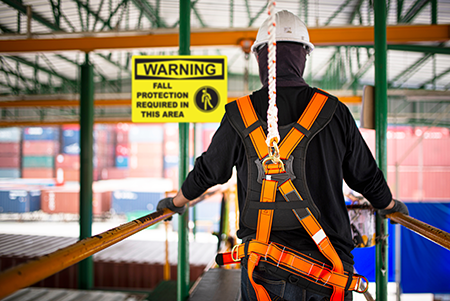
National Safety Month: Custom Signage to Combat Workplace Hazards
How Slippery When Wet Signs Prevent Common Workplace Injuries When it comes to slips, trips, and falls, one ...
Read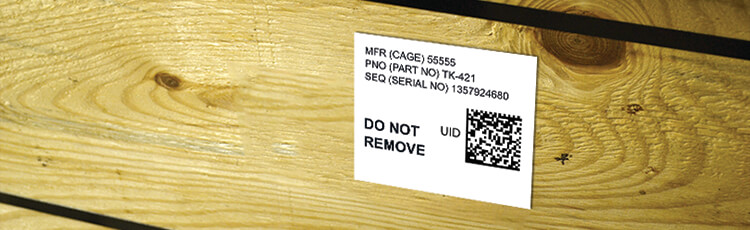
Marine Corps Air Facility Adds App, Steps Up Safety Program
A safety team at the Marine Corps Air Facility (MCAF) in Quantico, Virginia, tackled safety issues and ...
Read