OSHA's Standard for Walking-Working Surfaces

Slips, trips, and falls can seem relatively minor in the grand scheme of things: Who among us, office workers included, hasn't slipped on a puddle in front of the coffee maker, or tripped over a door jamb? The hazards, though they seem small, can have enormous consequences in a wide range of industries.
The Bureau of Labor Statistics (BLS) reported 238,610 trip, slip, and fall cases in 2015-up from 229,630 in 2011. That same year, the agency documented 800 fatal slips, trips, and falls-again, up from 681 in 2011.
OSHA's standard for walking-working surfaces, 29 CFR 1910.22, outlines requirements for ensuring that work surfaces are clean, dry (whenever possible), and properly maintained to ensure employee safety. Following these rules can cut down on injuries, improve safety, and save employers money.
The important standard was updated in late 2016, when OSHA issued a Final Rule that narrowed its focus and cleaned up its language, providing greater clarity and direction for employers.
Here's a look at what the standard includes, how it applies to your workplace, and how Duralabel can help.
Basic Requirements for Maintaining Walking-Working Surfaces
First thing's first: What exactly is a walking-working surface? OSHA defines it in 29 CFR 1910.21 as "any horizontal or vertical surface on or through which an employee walks, works, or gains access to a work area or workplace location."
Accordingly, the standard offers requirements for ensuring clean, accessible working conditions. Where hazards are unavoidable, OSHA offers requirements for mitigating those risks.
Here's a quick look at the key takeaways from 29 CFR 1910.22, OSHA's standard for walking-working surfaces:
- Workroom floors must be clean and (whenever possible) dry, and employers must account for weather-related hazards (such as snow or ice), loose boards, corrosion, spills, and other hazards
- When wet processes are used (such as in commercial food processing plants), employers must install drainage and provide dry standing places (such as floor mats)
- Employers must ensure that work surfaces can support the maximum intended load designed for that surface
- Employees must have a safe means of access to and from all walking-working surfaces
- All walking-working surfaces must be inspected (regularly and when warranted) and maintained in safe, working condition
Final Rule Update to OSHA's Walking-Working Surfaces Standard
As part of its Final Rule update issued in late 2016, OSHA made subtle modifications to 29 CFR 1910.22. These updates, which went into effect in January 2017, largely consisted of performance-based language that's easier to understand and follow.
Specifically, here's what's new and different after the update:
- Requirements for guard rails and surface covers were shifted to other standards that correspond more closely with fall protection
- The standard no longer requires employers to mark "permanent aisles and pathways;" rather, that obligation was folded into 29 CFR 1910.22(c), which now requires employers to provide "a safe means of access and egress to and from walking-working surfaces."
- OSHA now requires regular inspections of walking-working surfaces, making the rule more consistent with the agency's construction standards
How Floor Marking Can Help Compliance With 29 CFR 1910.22
OSHA required some form of floor marking in its previous iteration of 29 CFR 1910.22, most pointedly with the requirement, "Permanent aisles and passageways shall be appropriately marked."
Following the agency's Final Rule, however, that language has been stricken from the current standard.
Rather, OSHA's Final Rule indicates that floor marking is still required elsewhere in the standard; specifically, it points to 29 CFR 1910.22(c), which insists that employers provide (and ensure employees use) "a safe means of access and egress to and from walking-working surfaces."
In its Final Rule, the agency said, "One way employers can meet the performance language is by appropriately marking passageways and permanent aisles as a means of identifying safe access and egress."
To that end, employers should consider floor marking for ensuring safe, clean walking-working surfaces. Here's how floor marking can help:
- Stop slips, trips, and falls: Apply tread tape to stairs, docks, kitchens, and other areas where slippery conditions may pose hazards
- Highlight emergency egress paths: Offer safe egress paths in power outages, fires, and other lowlight conditions with glow-in-the-dark floor marking
- Increase visibility: Use reflective tape to call attention to hazards, electrical panels, edges, and more
Floor Marking Resources from Duralabel
Duralabel offers free resources for employers looking to better understand (and get started with) floor marking. Discover common floor marking uses with our Floor Marking Color Chart, and brush up on standards and common applications with our Best Practice Guide to Floor Marking.
Improve safety and meet OSHA's requirements for walking-working surfaces with PathFinder floor marking, wayfinding, and safety tape by Duralabel. PathFinder Tread Tape can help workers avoid slip, trip, and fall hazards, while PathFinder Glow Tape can guide employees to safety by highlighting pathways in emergency situations.
Related Resources
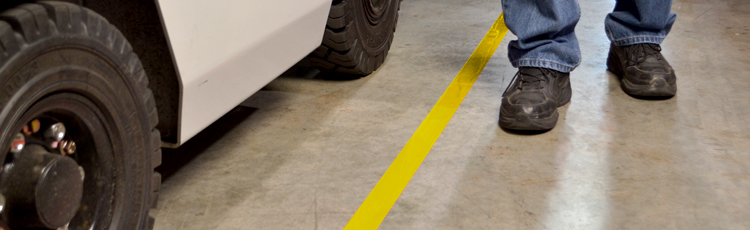
OSHA Announces Walking-Working Surfaces Rule
OSHA pushed through updated standards for walking-working surfaces in late 2016. A walking-working surface is ...
Read
Floor Signs
When employers imagine floor marking, most think of aisle markers, pathway designations, and hazard stripes. ...
Read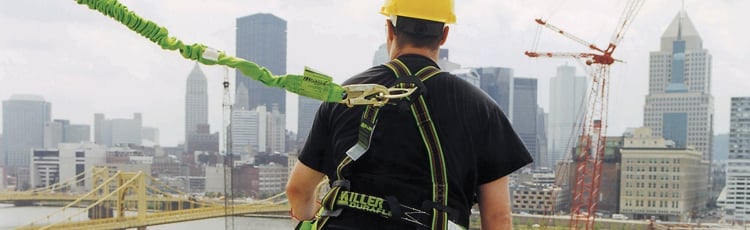
OSHA and Ironworkers Partner for Safety Outreach
OSHA and Ironworkers are partnering up to help boost safety programs and prevent the most common injuries, ...
Read