OSHA's Process Safety Management Standard
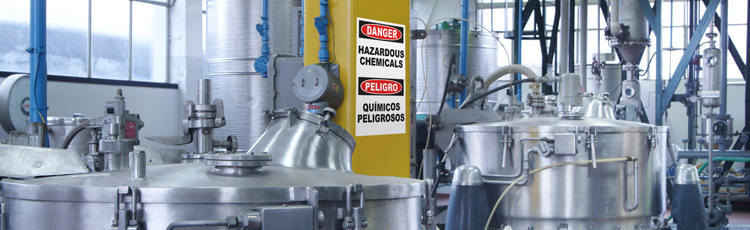
OSHA established a Process Safety Management (PSM) standard that applies to all companies that use any one of more than 130 dangerous chemicals. The OSHA Process Safety Management standard includes companies that use more than 10,000 pounds of flammable liquids and gases.
Overview of Requirements
Unexpected releases of toxic, reactive or flammable chemicals continue to be regularly reported. There is a potential for an accidental release any time these types of materials are not properly controlled. This creates the potential for a disaster. The purpose of the OSHA Process Safety Management standard is to prevent these types of releases.
Understanding OSHA's approach to process safety management requires an understanding of what OSHA means by the term "process." The OSHA definition of process is: "any activity involving a highly hazardous chemical including using, storing, manufacturing, handling, or moving such chemicals at the site, or any combination of these activities." In addition, OSHA defines any group of vessels that are interconnected, as well as separate individual vessels, that could result in the release of a highly hazardous chemical, as part of a single process.
Labels and Signs in Process Safety Management
Labels and signs play a critical role in all aspects of process safety management. They reliably provide hazard warnings, operating information, and safety reminders at the physical locations where this information is most needed.
Process Safety Management - OSHA Required Information
The starting point in process safety management is to compile written process safety information. OSHA requires that this be done before conducting a process hazard analysis. The compilation of written process safety information will help both the employer and employees identify and understand the hazards of processes involving highly hazardous chemicals.
Process safety information must include details about the hazards of the highly hazardous chemicals used or produced by the process. It must also describe the technology and equipment used in the process. OSHA requires that, at a minimum, the following be included:
Information about Chemical Hazards:
- Toxicity
- Permissible exposure limits
- Physical data
- Reactivity data
- Corrosivity data
- Thermal and chemical stability data, and the hazardous effects of inadvertent mixing of different materials
In some cases the above information may already be available in Material Safety Data Sheets which, as of June 2015 will be found on the HazCom 2012 converted Safety Data Sheets.
The Process Technology:
- A block flow diagram or a simplified process flow diagram
- Description of the process chemistry
- Maximum intended inventory
- Safe upper and lower limits for such parameters as temperatures, pressures, flows and compositions.
- An evaluation of the consequences of deviations, including those deviations affecting the safety and health of employees.
If the original technical information no longer exists, the needed technology information may be developed as a part of the process hazard analysis.
The information about the equipment in the process must include the following:
- Materials of construction
- Piping and instrument diagrams (P&IDs)
- Electrical classification
- Relief system design and design basis
- Ventilation system design
- Design codes and standards employed
- Material and energy balances for any processes built after May 26, 1992
- Safety systems (e.g., interlocks, detection, or suppression systems)
In addition, the OSHA Process Safety Management standard requires that the employer document that process equipment complies with recognized and generally accepted good engineering practices.
OSHA established a Process Safety Management (PSM) standard that applies to all companies that use any one of more than 130 dangerous chemicals. The OSHA Process Safety Management standard includes companies that use more than 10,000 pounds of flammable liquids and gases.
Overview of Requirements
Unexpected releases of toxic, reactive or flammable chemicals continue to be regularly reported. There is a potential for an accidental release any time these types of materials are not properly controlled. This creates the potential for a disaster. The purpose of the OSHA Process Safety Management standard is to prevent these types of releases.
Understanding OSHA's approach to process safety management requires an understanding of what OSHA means by the term "process." The OSHA definition of process is: "any activity involving a highly hazardous chemical including using, storing, manufacturing, handling, or moving such chemicals at the site, or any combination of these activities." In addition, OSHA defines any group of vessels that are interconnected, as well as separate individual vessels, that could result in the release of a highly hazardous chemical, as part of a single process.
Labels and Signs in Process Safety Management
Labels and signs play a critical role in all aspects of process safety management. They reliably provide hazard warnings, operating information, and safety reminders at the physical locations where this information is most needed.
Process Safety Management - OSHA Required Information
The starting point in process safety management is to compile written process safety information. OSHA requires that this be done before conducting a process hazard analysis. The compilation of written process safety information will help both the employer and employees identify and understand the hazards of processes involving highly hazardous chemicals.
Process safety information must include details about the hazards of the highly hazardous chemicals used or produced by the process. It must also describe the technology and equipment used in the process. OSHA requires that, at a minimum, the following be included:
Information about Chemical Hazards:
- Toxicity
- Permissible exposure limits
- Physical data
- Reactivity data
- Corrosivity data
- Thermal and chemical stability data, and the hazardous effects of inadvertent mixing of different materials
In some cases the above information may already be available in Material Safety Data Sheets which, as of June 2015 will be found on the HazCom 2012 converted Safety Data Sheets.
The Process Technology:
- A block flow diagram or a simplified process flow diagram
- Description of the process chemistry
- Maximum intended inventory
- Safe upper and lower limits for such parameters as temperatures, pressures, flows and compositions.
- An evaluation of the consequences of deviations, including those deviations affecting the safety and health of employees.
If the original technical information no longer exists, the needed technology information may be developed as a part of the process hazard analysis.
The information about the equipment in the process must include the following:
- Materials of construction
- Piping and instrument diagrams (P&IDs)
- Electrical classification
- Relief system design and design basis
- Ventilation system design
- Design codes and standards employed
- Material and energy balances for any processes built after May 26, 1992
- Safety systems (e.g., interlocks, detection, or suppression systems)
In addition, the OSHA Process Safety Management standard requires that the employer document that process equipment complies with recognized and generally accepted good engineering practices.
Related Resources
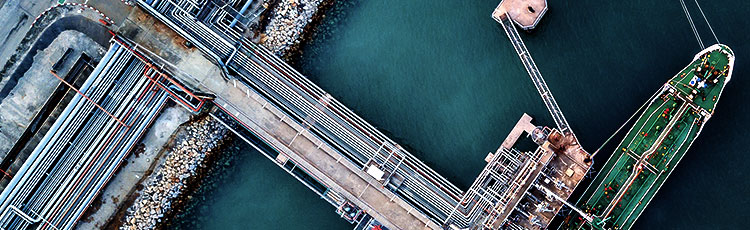
LNG Demand Calls for Effective Safety Solutions
Demand for liquid natural gas is surging. From liquefaction to transport to electricity generation, LNG is a ...
Read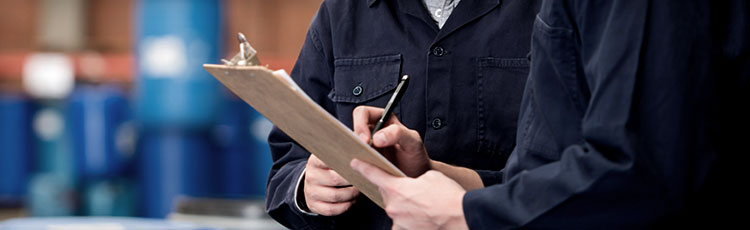
Safety Risk Management
In our experience, those companies who place major significance on risk management are the most successful in ...
Read
10 Safety Tips for Oil and Gas Industry Workers
Workers in the oil and gas extraction industry continue to be one of the highest at risk of injuries and ...
Read