Safety Risk Management
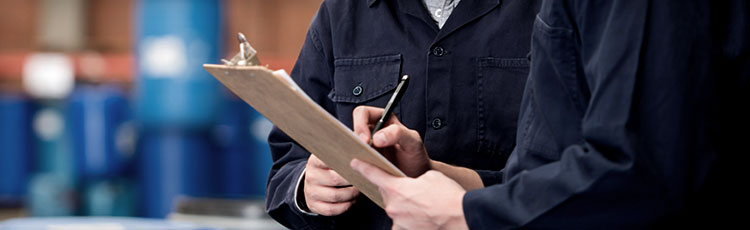
In our experience, those companies who place major significance on risk management are the most successful in the total business effort. This is not to say safety and risk management is the only element to provide them with success. But, without it, long-term success will not occur. Paying attention to people, safety, environmental protection, assets protection, and continuous efficient production makes a company successful.
There are various methods to assessing risk in your facility. Safety risk management begins with a hazard analysis of the workplace to ensure compliance with health and safety laws.
Safety Risk Management Plan
Once the hazard risk analysis is complete, a safety risk management plan can be developed. The ideal response to identifying a hazard is to eliminate it. This may be possible through redesigning the process, or changing the equipment and materials used. If the hazard is eliminated, a safety risk management plan is not needed.
If the hazard cannot be eliminated, the next best option is to prevent access. This is done though isolating or guarding. Isolation means placing dangerous equipment in a location that is not generally accessible, such as within an enclosure or room. For example, electrical equipment that might be subject to an arc flash may be located within a room that only appropriately trained and equipped employees may enter.
Operating Procedures
Clear, consistent, and appropriate operating procedures must be included in the Safety Risk Management Plan. Based on OSHA requirements operating procedures for normal operation, as well as emergency and out-of-specification operations must be established and documented in writing. The procedures should include:
- Initial startup
- Normal operations
- Temporary operations
- Emergency shutdown, including:
- identifying the conditions under which emergency shutdown is required
- the assignment of shut down responsibility to qualified operators
- the safety of those engaged in an emergency shut down
- Emergency operations;
- consequences of deviations
- steps to take to correct the deviations
- precautions that are necessary
- Normal shutdown
- Start-up following a turnaround, or after an emergency shutdown
The operating procedures must be readily available to those operating the equipment ad process. Operators and operations supervisors should review them regularly to ensure written procedures correctly reflect current operating practices. The Safety Risk Management plan should require that operating procedures be reviewed any time there is a change in the materials, technology, equipment, or facility used for the process. OSHA requires that processes using highly hazardous materials, the employer must review and certify the operating procedures annually.
An area of safety risk management that is often cited by OSHA is the control of hazardous energy through lockout/tagout (LOTO). The Safety Risk Management plan must establish LOTO procedures, and those procedures must always be followed with no exceptions.
Training
A safety program and operating procedures are of little value without training. That training must include an emphasis on the specific safety and health hazards of the equipment and process. For operating staff it must cover normal operations, as well as emergency conditions. For maintenance staff it must cover maintenance procedures, as well as safety related to the tools required for performing maintenance. Everyone involved with the process should be fully trained on the hazards associated with the materials used in the process.
Providing initial training does not end the employer's obligations for training. The Safety Risk Management plan must include refresher training. For processes involving highly hazardous materials OSHA requires that refresher training be provided at least once every three years. The true criteria is that employees must have whatever training is necessary, as often as necessary to ensure they adhere to the established procedures and safety requirements.
Finally, the employer must document each employee's training, including the identity of the employee, the date of the training, and include verification that the employee understood the training. The documentation must prove to OSHA that the employee was adequately trained, and understood that training. Need help with OSHA signage? Download our free guide.
Related Resources
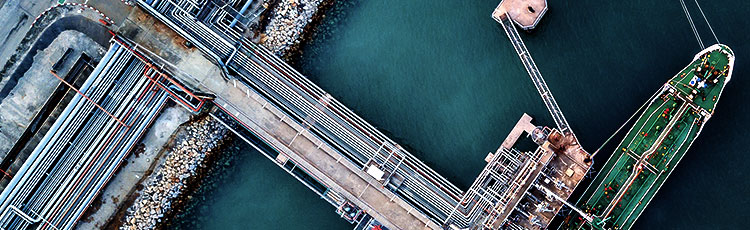
LNG Demand Calls for Effective Safety Solutions
Demand for liquid natural gas is surging. From liquefaction to transport to electricity generation, LNG is a ...
Read
10 Safety Tips for Oil and Gas Industry Workers
Workers in the oil and gas extraction industry continue to be one of the highest at risk of injuries and ...
Read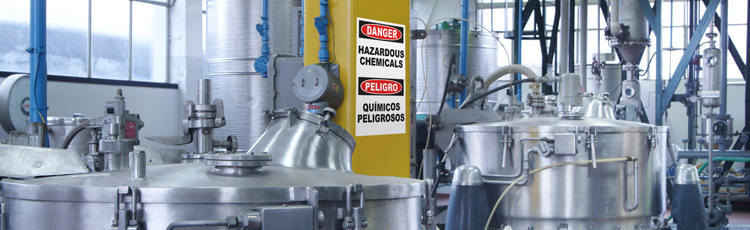
OSHA's Process Safety Management Standard
OSHA established a Process Safety Management (PSM) standard that applies to all companies that use any one of ...
Read