Protect Your Ears: Strategies to Prevent Work-Related Hearing Loss

It is no secret that noise plays a factor in day-to-day industrial manufacturing. Unfortunately, it is also one of the most pervasive occupational health problems within the industry too.
Exposure to elevated levels of noise can cause permanent hearing loss and other harmful health effects. The extent of damage depends on the intensity of the noise and how long a worker has been exposed to it.
Occupational hearing loss affects 1 in 4 workers each year and is the third most common work-related illness. According to the Center of Disease Control (CDC):
- 22 million workers are exposed to hazardous noise on-the-job each year.
- 1 in 8 people in the U.S. working population has hearing difficulty.
- 16% of noise-exposed tested workers have a material hearing impairment
How does Occupational Hearing Loss Occur?
There are a couple of ways in which hearing loss can occur in the workplace. Two of those ways are due to:
Loud Noises: Exposure to sound becomes hazardous when it reaches 85 A-weighted decibels (dBA) or higher. These types of noises can cause both permanent hearing loss and tinnitus.
Hazardous Chemicals: Exposure to certain chemicals, called ototoxicants, may cause hearing loss or balance problems, regardless of noise exposure. Ototoxicants come in three forms:
- Solvents
- Metals
- Asphyxiants
These chemicals can cause damage to the ears, which can include permanent hearing loss. The main issue with these types of chemicals is when they are combined with loud sounds, because it enhances the damaging effects of these drugs.
Occupational Hearing Loss is Preventable
Hearing loss is not curable, but preventable in most instances. Employers can do their part by providing hearing protectors to all workers exposed to 8-hour TWA noise levels of 85 dB or above. According to Occupational Safety and Health Administration (OSHA), this requirement ensures that employees have access to the tools needed to prevent hearing damage.
Noise controls are the first line of defense in protecting workers from work-related hearing loss. Reducing the noise even a little bit can reduce the risk of hearing damage and noise-related annoyances, as well as increase communication. OSHA suggested that employers implement these four protective measures into their facilities to keep workers safe.
- Engineering Controls— Engineering controls involve modifying or replacing equipment to reduce the noise level that is being transmitted to the worker's ear. According to OSHA, some ways this can be accomplished are:
- Place a barrier between the noise source and employee
- Isolate the noise source
- Place a barrier between the noise source and employee
- Administrative Controls— Make changes in the workplace that reduce or eliminate the worker exposure to noise.
- Limit the amount of time a person spends at a noise source
- Provide quiet spaces for workers to decompress from hazardous noise
- Create boundaries that restrict worker from entering areas with noisy equipment
- Limit the amount of time a person spends at a noise source
- Hearing Protective Devices— Workers should wear Personal Protective Equipment (PPE) at all times when exposed to hazardous noises during their shift to get the best level of protection. Invest in Personal Protective Equipment (PPE) such as earmuffs and plugs.
- Hearing Conservation Program—This type of program must be implemented whenever worker noise exposure is equal to or greater than 85 dBA for an 8-hour exposure or in the construction industry when exposures exceed 90 dBA for an 8-hour exposure. This program is designed to provide workers with the knowledge and hearing protection devices to protect themselves from long-term hearing loss.
DuraLabel Resources
Through the Hearing Conservation program, employers can train their workers on how to be safer while on-site. A great way to ensure this is to create visual cues for workers for workers as a way to reinforce training.
DuraLabel's free OSHA Safety Signs Instant Action Guide helps you create OSHA/ANSI compliant safety signs. The guide helps readers understand the appropriate regulations and standards and improve safety and efficiency. Request your free OSHA Safety Signs Instant Action Guide.
Want to learn how to implement 5s with all your industrial label needs? Download a free copy of the 5s Instant Action Guide. Give us a call today at 1-888-326-9244 and one of our experts will guide you through the process.
Read Next:
Police Officers and Hearing Loss
Related Resources

Tips from Fipps: Be Your Own Safety Superhero
Ensuring a safe and secure work environment is a shared responsibility that each one of us plays a crucial ...
Read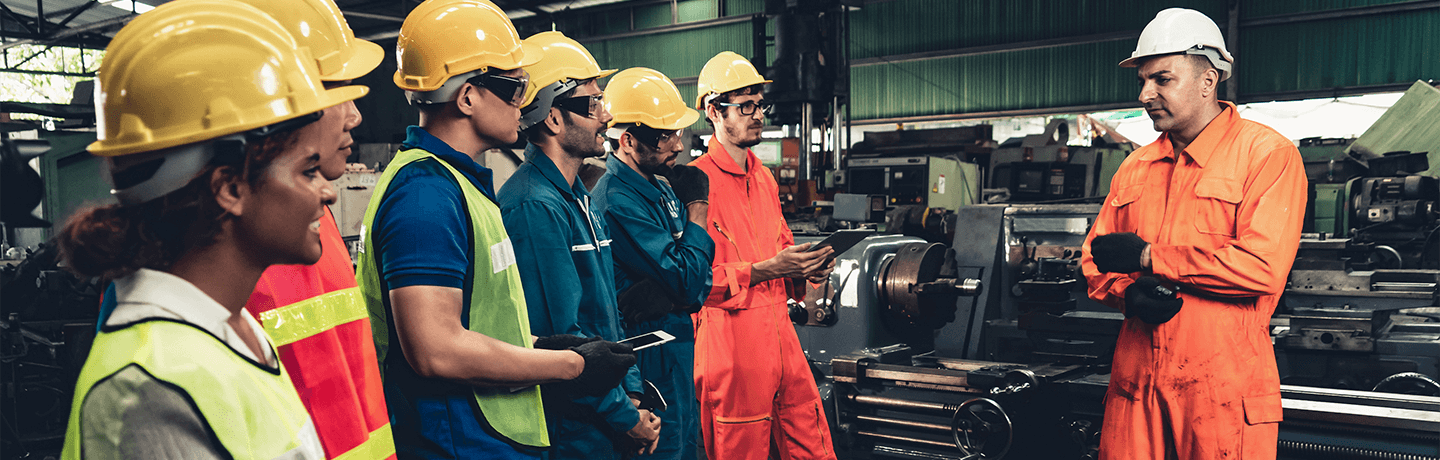
Building a Safer Work Environment: 5 Powerful Benefits of Safety Training
There are 12,900 worker-related injuries every day, according to the National Safety Council, and this ...
Read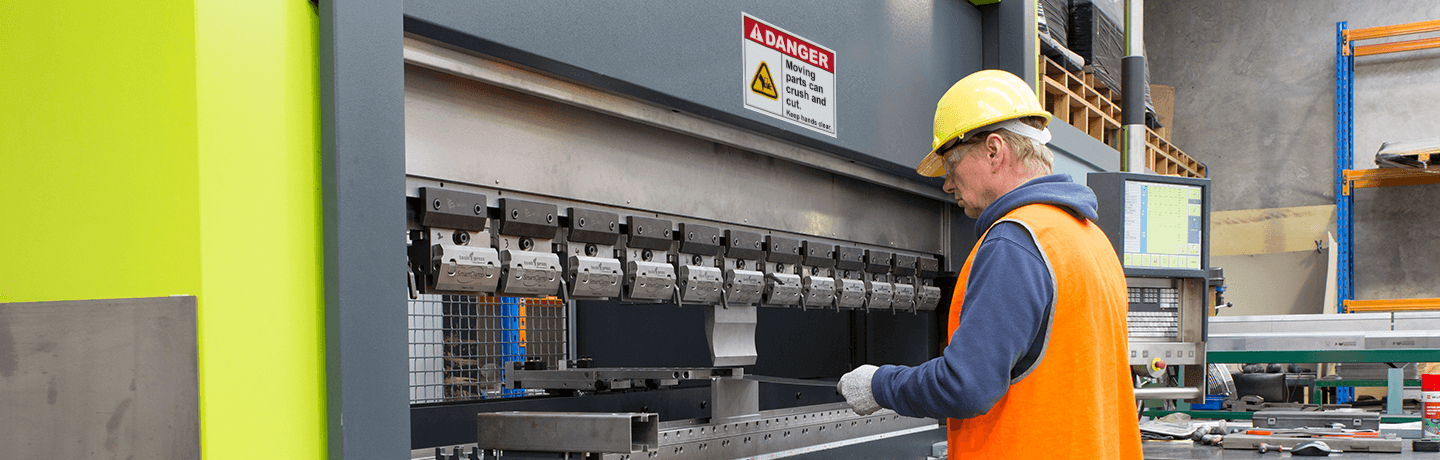
9 Tips for Effective Safety Messaging to Prevent Common Injuries
Organizations are required under the OSHA General Duty clause to provide a working environment "free from ...
Read