The Eight Steps to the QCDSM Process
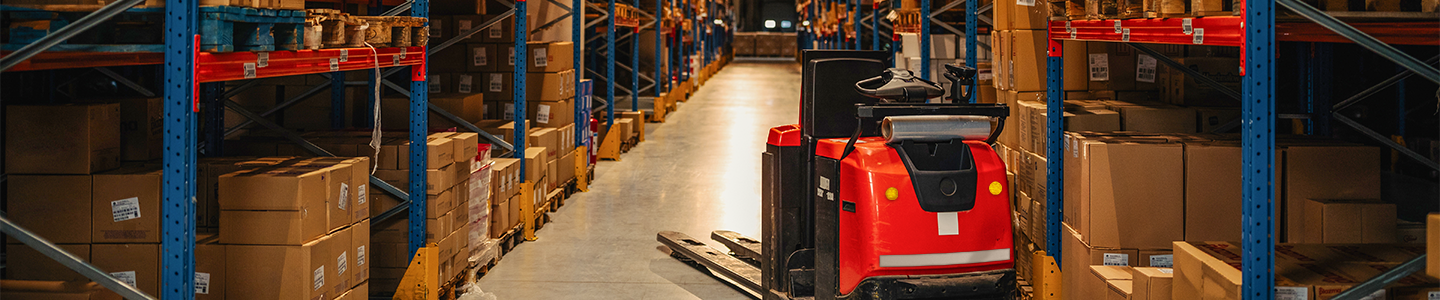
QCDSM is a mouthful of an acronym. Once you learn its meaning and apply its principles to your business processes, your company will meet its goals faster and with less effort than you had imagined. Achieving consistent Quality, competitive Cost, and on-time Delivery,while maintaining the highest levels of Safety and Morale, is obtainable through the QCDSM process.
Imagine your employees creating their own accountability. Through QCDSM they can measure their own performance on a daily or weekly basis. Your employees author their own procedures, establishing a sense of ownership in each work area. QCDSM's focus is on the performance of people in your company. It enables employees to communicate about, and manage, the systems that they work with on a daily basis. This empowerment boosts morale and helps your staff achieve quality, cost, and delivery targets.
The implementation of the QCDSM system has seen Jucy By Design transform its business.
We have seen a marked increase in productivity and decrease in defects which has ultimately resulted in a better product for a cheaper price. The buy-in from our staff has been key and the daily (training) meetings have given them the opportunity to make suggestions and also deal with any issues there and then rather than days or weeks down the track. The transformation has been great to see?
The lean business technique of QCDSM is a simple, step-by-step process in which the key players in a company are trained on visual management within small teams. Later they teach these methods of empowerment to those who will soon be leaders in the business.
Step 1. Seminar
The seminar is a three-day intensive hands-on learning experience for executives and managers to master QCDSM principles. The group goes through three continuous improvement cycles based on lean manufacturing techniques. They develop ideas, formalize a process then test the results.
Through this process the attendees learn:
-
- Appreciation for the challenges involved in managing the processes and the people.
- Everything is a process.
- The importance of the "Detail Process Sheet."
- Discipline of sticking to the environmental changes being instigated.
- The importance of team work and its effect on Quality, Cost, Delivery and Safety and Morale measurements.
Step 2. Training Meetings
During training, participants holistically view the QCDSM process and understand how their facility and company must move forward to ensure their future. The training objective is to look at ways to improve how business is managed and operated. At the conclusion of each training meeting, expectations are set for further training. Participants create the schedule for the remaining training sessions and specific tasks are assigned to various team members. The new way of doing business is now underway.
Step 3. Strategy Session
There are three goals of the strategy sessions:
- To ensure that individual teams are prepared to move forward Each team will have defined tasks that will be charted from their previous training meeting. Leaders in each group will follow daily progress from each team's data.
- To train the leaders of the teams Team leaders will master proper techniques and methods to facilitate ongoing training meetings for their groups. Learning a set format ensures that the teams are productive and solutions to problems are found via the daily tracked charts. Following this process creates an ongoing cycle of emerging leaders to carry on the processes learned from QCDSM.
- Establish the framework for the Support Level and Management Level Meetings within the company. Buy-in from the entire company is required of the QCDSM system for it to be successful. To support the first level training meetings, daily and weekly meetings should be organized to ensure that concerns and issues are being addressed and communicated to key players. Management must understand issues the team faces in order to provide support.
Step 4. Trial RunA 2-4 week trial run is built into QCDSM in order to continue momentum and build the habits that will carry the new system through to full implementation. This is the time to establish goals, rehearse meetings, and determine how data will be collected and messages communicated up the chain of command.
Step 5. Day before First Training Meeting
After the trial run is complete, the department is ready for its first training meeting. It is critical that participants understand the philosophy behind the system. Ideally a presentation should be given to the first group of the QCDSM system before official hand-over to meeting facilitators.
Step 6. Detailed Process Sheet
During the first meeting, a detailed document is created to track the process of continuous improvement. The detailed process sheet is used going forward to capture methods and data for tracking. Training meetings will compare the document against actual results, allowing suggestions for improvement. The group can assign a person to monitor the progress and how the information is tracked.
The detailed process sheet may contain categories such as:
- Description of work
- Which department work is performed in
- Who the work is performed by (initials could be used to sign off on rotating shifts)
- The date the work was performed
- An outcome of work performed
- Key points, observations or suggestions for improvement.
Step 7. Idea and Suggestion Process
The training room format takes precedence in this step. Measurements are tracked from the detailed process sheet and a story needs to be told in the training meetings.
- What went right?
- What went wrong?
- What can we do to fix/improve it?
Every person's point of view must be considered. This empowers all employees to develop a plan of action when re-grouping during future training sessions. A to-do list is created for all meeting participants. A plan is set and managed until new ideas emerge. This is a totally integrated approach to continuous improvement.
Step 8. Customer Concern Database
The main objective of the training meetings is to identify problems and encourage employees to solve them before they move up the chain of command. The QCDSM process sets up a database in either Excel or Access to record internal customer concerns and track progress. It is the most relevant tool to track what is actually preventing or encouraging consistent quality, competitive cost, on time delivery, and high levels of safety and employee morale. This system solves the problem of little or no follow-up to employee suggestions, and builds trust in management that issues will be addressed and worked through.
The QCDSM techniques have been developed by QCD Systems, experts in lean business approaches who provide training and related materials. If you have implemented other lean tactics such as Kaizen, Kanban or Total Productive Maintenance, then QCDSM will complement the company culture already established-making it easier to hit your targets.
Related Resources
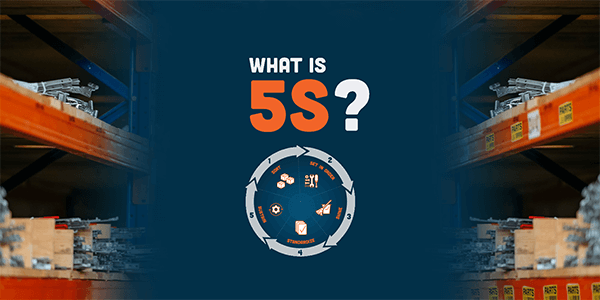
The 5S System Explained: From Origins to Implementation
What Is the 5S System? The 5S system is a lean manufacturing tool that improves workplace efficiency and ...
Read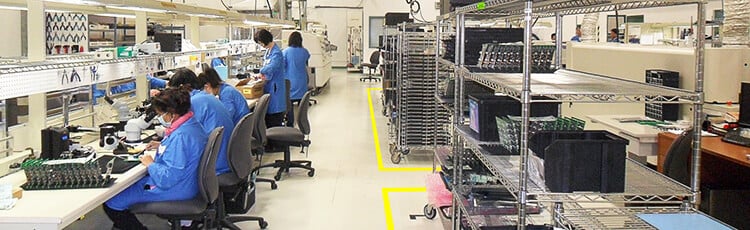
Lean Manufacturing and the 5S System
What is 5S in Manufacturing? 5S is a lean manufacturing method used to eliminate waste, improve workplace ...
Read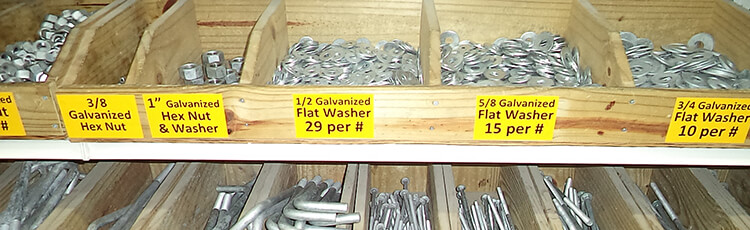
Lean Manufacturing Process
What is the Lean Manufacturing Process? The Lean Manufacturing processis a structured system for eliminating ...
Read