Three Essential Tips to Prevent Workplace Head Injuries

Brain Injury Awareness Month
Every year, the Brain Injury Association, the nation’s oldest and largest brain injury advocacy organization, raises awareness for brain injuries and their survivors in March.
According to the Brain Injury Association, brain injuries are the leading cause of death and disability in the United States. Brain injuries affect:
- 5.3 million individuals live with permanent brain injury-related disabilities
- One in every 60 people are affected
- 20-25% of workplace injuries are brain injuries
There are two types of brain injuries to be on the lookout for:
- Acquired brain injury (ABI)— not hereditary, congenital, degenerative, or induced by birth trauma.
- Traumatic brain injury— defined as an alteration in brain function or other evidence in brain pathology, caused by external force trauma.
The Center of Disease Control said workers in construction are at a higher risk for traumatic brain injuries, more than any other industry due to the type of environments in which they work and often involve risks of falls and flying objects. 20-25 percent of construction workers have experienced a TBI.
While head injuries are common in the construction industry, this is not the only industry at risk of brain industry. Workers in the steel and structural iron are at risk of serious injury too.
Workplace brain injuries are preventable. OSHA requires employers to keep their workers safe by providing necessary personal protective gear. Here are three tips employers can keep their workers safe, while reducing the risk of serious injury:
TIP 1: Implement Hierarchy of ControlsBy knowing where the hazards in your workplace are, it becomes easier to control exposure to those areas, and it becomes a vital part in protecting workers. The hierarchy of controls helps determine which actions will best control exposures. There are five levels of actions to reduce or remove hazards. The preferred order of action based on general effectiveness is:
Elimination—In this step you are physically removing the hazard. Employers can implement this step by changing the work process to stop using a toxic chemical, heavy object, or sharp tool. No exposure is the operative solution.
Substitution-This step is designed to replace the hazard
Engineering controls—During this step, it is designed to isolate workers from the hazard.
Administrative controls—Designed the change the way workers perform their work.
TIP 2: Wear Personal Protective Equipment (PPE)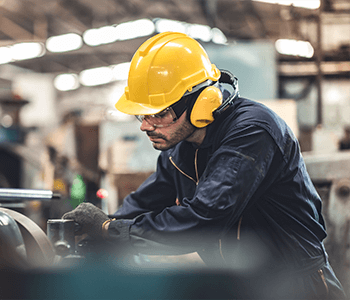
The use of PPE is essential to protecting workers from serious injury. According to OSHA standards, employees working in areas where the risk of head injury due to impact, falling, flying objects, or electrical shock must wear a helmet. This standard does not cover specific helmet criteria but refers to complying with ANSI Z89.1-200.
According to the American National Standards Institute (ANSI), industrial hardhats should not only absorb the impact of blows to the head, but should also serve as insulators against electric shocks, be water resistant and slow burning, and shield the scalp, face, neck, and shoulders. ANSI Z89.1 prepares hard hats for any of these anticipated forces through rigorous testing of the helmets.
- 84% of all head injuries were due to workers not wearing a helmet
Once a plan has been implemented to recognize hazardous areas, and PPE requirements have been created, employees need to be trained to reinforce the plan. Here’s a list of items that should be included in the safety training:
- Identify hazard areas
According to the CDC, the number one cause of workplace TBI is falls. Identifying areas in your facility that are common hazards for your workers or could be a hazard, and placing safety signage in those areas as visual reminders to workers to watch their step is crucial to the prevention of head injuries.
- Recognize signs of someone suffering from a TBI
There are 4 common signs that someone has experienced a brain injury:- Irritability
- Aggression
- Posturing
- Amnesia
Knowledge of helmet types and where they should be worn
Employers are required to provide protective coverings to workers in the following situations:- When objects or debris might fall from above and strike workers on the head
- When employees may strike their heads against fixed objects, like supports, beams, or other equipment
- When there is the possibility that workers' heads will make contact with electrical hazards
- Type I offers protection to the top of the head and is commonly used in the United States
- Type II offers protection to the top and sides of the head and is commonly used in Europe
-
- Hard Hat Classes: The three classes are based on the level of protection they provide from electrical hazards.
- Class G (General) hard hats are rated for 2,200 volts
- Class E (Electrical) hard hats are rated for 20,000 volts
- Class C (Conductive) hard hats do not offer electrical protection
- Hard Hat Classes: The three classes are based on the level of protection they provide from electrical hazards.
Assessing your facility and pinpointing where common hazards and potential hazards may occur the first step to preventing workplace accidents. The next crucial step is training employees on what to look out for, reinforcing this knowledge with OSHA-approved labeling and signage, and ANSI-approved PPE. There is nothing worse than being out of work due to a fall that could have been prevented by following facility guidelines.
DuraLabel offers a wide variety of hard hat warning signs, hard hat area message tape, and even reflective stick-ons for hard hats to promote safety and visibility. Just as it is important to wear a hard hat for safety, it's also important that your employees know where to wear their hard hats. A hard hat is only useful when it's being worn in the appropriate areas. With DuraLabel hard hat signs, tape, reflective stick-ons, and other products, you can adhere to OSHA guidelines and keep your employees safe. For more information on how we can help improve the safety in your facility, please give us a call at 1-888-897-5580 and one of our experts will guide you through the process
DuraLabel’s free OSHA Safety Signs Instant Action Guide helps readers understand regulations and standards and improve safety and efficiency. Download OSHA Safety Signs Instant Action Guide.
Want to learn how to create individual safety-related programs? DuraLabel's free Best Practice Guide for EHS Managers helps create core steps for both hazard-based and task-based risk assessments, as well as provides guidance through the Hierarchy of Controls to address workplace hazards. Request your free copy of the Best Practice Guide for EHS Managers.
Read Next:
OSHA and ANSI Hard Hat Requirements
Related Resources

Guidelines for OSHA Fall Protection Standards and Compliance
Ineffective or missing fall protection has been the Occupational Safety and Health Administration's (OSHA) ...
Read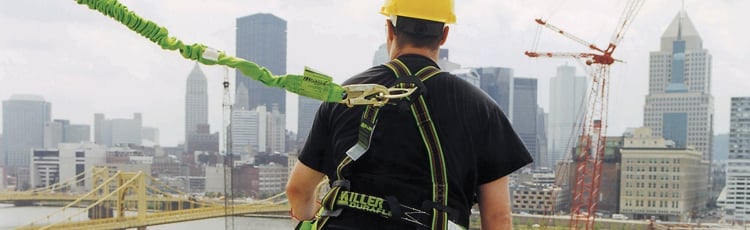
OSHA and Ironworkers Partner for Safety Outreach
OSHA and Ironworkers are partnering up to help boost safety programs and prevent the most common injuries, ...
Read
OSHA's Standard for Walking-Working Surfaces
Slips, trips, and falls can seem relatively minor in the grand scheme of things: Who among us, office workers ...
Read