Unlocking Success: 5 Essential Tips for Effective Training

Workplace injuries are common occurrences. There are 12,900 worker-related injuries every day, according to the National Safety Council, and this equates to one injured person every 7 seconds. Most injuries are due to human error and are often preventable. OSHA's training standard for all industries says all workers must be trained in the tasks, situations, and tools they will use on the job.
- The average employer spent $1,300 per worker on training in 2021.
- 68% of employees prefer to learn and train on the job
- 87% of millennials believe learning and development in the workplace is important.
Training is an investment for both companies and the people they employ, so why are companies that shell so much money into it not receiving quality results? To understand what to do, we first need to understand what not to do. Here are 3 examples of how training can have a negative impact:
- No planning— If the material is thrown together at the last minute, this can negatively impact the company overall. If workers sense that you do not care about training, then it is likely they will not care either. Training can negatively impact your business without knowing the goals of your workers or business.
- Reduced morale – When training time feels wasted, no one benefits. Training workers on things that do not reflect in their day-to-day duties often adds stress.
- Too much money spent—If effort is not placed into the training session, workers will feel it has been rushed
There are major benefits to regular worker training and often includes enhanced employee performance and a boost in productivity. OSHA conducted a study on safety programs in 8 states and found that training workers on how to be safter reduced the number of injuries by 9-60%. Consider these 5 effective training practices to implement in your facilities:
Get to know your employees—New employees are 5 times more likely to be injured on the job, according to the Bureau of Labor and Statistics. It is important to provide safety training. After that, create a training environment with your employees’ learning preferences in mind. The more information you gather from your team, the better those training sessions will be.
- Set clear objectives—People tend to listen to caution when they understand why it is important. Explain how training will keep them safe in their jobs, then tailor training to how they can apply those new skills to their day-to-day tasks.
- Create an obtainable learning path—Create an environment where employees are encouraged to give their honest feedback about safety. Employees should be able to trust leadership with the information they provide, and they need to trust their coworkers to speak up when they observe safety concerns. A great way to establish this type of environment is by rewarding your staff when they come across situations that can be unsafe and then fixing those issues.
- Provide regular constructive feedback—Research suggests positive feedback is an important feedback tool. If the goal is to promote a positive environment, limit negative feedback and give twice as much positive feedback. Providing feedback to your workers not only helps them improve their performance, but it also helps prevent accidents.
- Use signs and labels— Visual communications tools are great at reinforcing workplace training by providing workers with attention grabbing prompts. Training workers to be skilled visual communicators allows them the ability to identify hazards quickly and think critically too.
How Can Visual Communication be Implemented in Training?
Signs and labels must comply with OSHA and ANSI applicable regulations by using universally recognized symbols or icons, and be strategically placed in visible locations to maximize their impact and effectiveness. Training workers on where these signs are located and why they have been place there is an important step for reducing workplace injuries. Here are three types of signs and labels you may see in your facilities and their purposes:
- Safety signs: Create visually clear and concise safety signs that remind employees of important safety procedures and precautions. These signs can be placed in relevant areas such as near machinery, on doors, or in hazardous zones.
- Color-coded labels: Implement color-coded labels to signify different categories or types of items or areas. This can help employees quickly identify and organize items or navigate through different sections of the workplace.
- Hazard warning signs: Use visually striking hazard warning signs to alert employees about potential dangers in specific areas. These signs should include universally recognized symbols or icons to convey the message quickly and effectively.
If the fear of losing good workers is weighing on you, try creating an environment where worker growth and safety becomes a regular part of the company culture. This will not only result in a safer work experience, but a positive one for everyone. Creating a culture of safety will take time and effort. Consistency and active employee engagement are two primary components to improve workplace safety programs, which leads to fewer incidents, better productivity, and higher morale.
Related Resources

Protect Your Ears: Strategies to Prevent Work-Related Hearing Loss
It is no secret that noise plays a factor in day-to-day industrial manufacturing. Unfortunately, it is also ...
Read
Get the Most Out of Toolbox Talks: Workplace Safety and Communication
What Are Toolbox Talks? Toolbox Talks, short safety meetings typically held at the job site before the ...
Read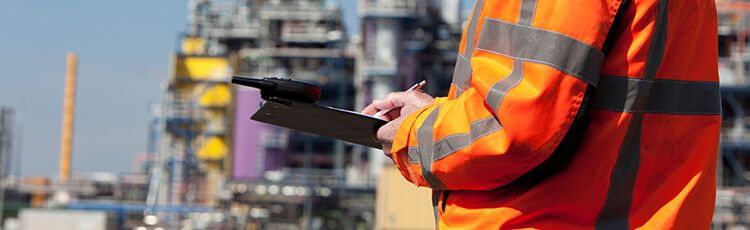
ASSP: Advancing Safety with Education and Research
The American Society of Safety Professionals has created a new academic and research council. The council ...
Read