What Is Kanban?
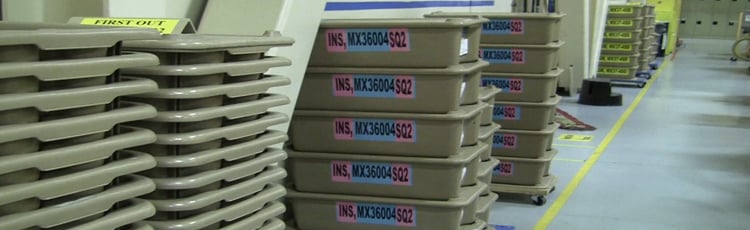
In the face of declining sales and profits during the 1950s, Eiji Toyoda began looking for ways to improve Toyota's manufacturing processes. He visited the Ford facility in Michigan to learn from the manufacturing giant. While he was impressed by the facility's scale and manufacturing rate, he saw many areas that could be improved, including the supply chain.
Collaborating with Taiichi Ohno, Toyoda developed Kanban as a method for controlling the flow of materials within a supply chain to reduce waste. Kanban means "billboard" or "visual signal." Using visual signals (cards), Kanban controls inventory by pulling supplies to the production floor based on customer demand.
Kanban in Action
Let's say a fabricator creates steel frames. The steel is placed on pallets. Every time a work station empties a pallet, a worker removes the attached card, and sends it to purchasing. A new pallet of steel is not ordered until purchasing receives the Kanban card.
A more realistic manufacturing example would include a series of workstations performing different tasks. One station might shape the steel, while a second does the welding and a third inspects the final product before it ships. Each station pulls work from the previous until the job is finished.
In this example, each station will only receive the work it can handle. The inspection station will not receive additional items to inspect until it sends a Kanban card requesting more work. This is true for every station on the production floor.
Using Kanban creates a leaner manufacturing process. It will optimize production, reduce wasted space, and increase the overall production quality.
Because the fabricator only orders supplies based on the customer's order and their own production capability, Kanban is referred to as a "pull system." It pulls supplies to the production floor based on what the customer needs and the work that has been completed. Kanban works because it pulls supplies based on six guiding principles:
- Based on the example above, the production floor may only order parts listed on the Kanban card.
- The purchasing or supply department may only send items that are listed on the Kanban card to the production floor.
- No supplies are made or ordered without a Kanban card.
- Every item must have a Kanban card attached to it in some manner so that the production floor can send it back to the supply department when more parts are needed.
- Incorrect parts or quantities of parts are never sent to the next production phase, and defects are more readily identified.
- The number of Kanban cards going to the supply department can help to identify potential problems. For example, if the number of cards suddenly drops, it may mean that the completed work is not being removed from the work area quickly enough.
Kanban depends on visual communication to ensure that each order receives the supplies it needs and that the supply chain works with little or no interruptions. Wasteful overproduction, underproduction, and large inventories are reduced or eliminated completely. By strictly controlling the supply chain, Kanban also creates predictable delivery times and improves quality.
Help improve your workflow by using signage and floor marking to display work procedures and changes to the overall workflow.
Is Kanban Right for Me?
The Kanban system is a powerful lean tool that can do more than reduce inventory. Kanban improves the overall production process and may be right for your business if:
Your customers need their products delivered on schedule. Kanban will make it easier to provide reliable delivery times because it makes your process more visible. The cards make it so you can track production times, lead times for additional supplies, and delivery times for new supplies. Delivery time is also improved because Kanban controls how much work can be done at any one time: items are completed more quickly because there are fewer conflicting priorities.
Your customers need every project to be of the utmost quality. Kanban increases quality in several ways.
- It will help to eliminate situations where projects are delivered late or incomplete because work started too early and parts are either reworked or overlooked. The system pulls work when there is a customer demand in the form of a finalized order.
- It will help to eliminate errors in manufacturing by reducing the work-in-progress (WIP). New work does not start until the current work is finished and removed from the workstation. For example, one process might include making a steel beam. Once the beam is completed, it is inspected. The beam must pass its inspection before it can be pulled to the next process. If the current batch has an error, it is corrected before the next batch starts.
Kanban Evolves
Businesses continue to become more automated, using robotics, barcode systems, and software. Recently, Kanban has begun to move from physical cards to an electronic system-E-Kanban. This system uses software and barcodes to automatically request new parts once they reach a specific level.
(Source: J. Olhager and E. Selldin. "Supply Chain Management Survey of Swedish Manufacturing Firms." International Journal of Production Economics)
Instead of attaching a card to each bin, a barcode is used to identify specific parts as well as the quantity of the parts in the container. Workers scan the barcode once they use the supplies. The software then reads the information from the barcode and sends a request for additional parts. The request can either be sent to the purchasing department or directly to the supplier.
While E-Kanban has become more prevalent over the years, physical Kanban cards are by no means obsolete. In fact, facilities may use physical Kanban cards in support of E-Kanban. Traditional Kanban cards create an obvious signal that visually informs workers that there is a specific need. A red card sitting in an empty bin lets workers know that they should expect replacement parts. If the bin is not filled in a timely manner, workers can more readily spot issues in the supply line.
Manufacturing and Beyond
While the origin of Kanban is directly tied to manufacturing, it can help companies outside manufacturing become lean. For instance, software development and healthcare can both benefit from using Kanban.
In both cases, Kanban has been adapted to meet the demands in a non-manufacturing environment by changing the visual cue to Kanban board. For healthcare claims, the board is used to visually represent claims that have been filed (Done), claims that are currently being filed (Doing), and claims that need to be filed (To Do). Like the card system, claims do not move until there is a demand to do so.
This allows claims to flow in a consistent and controlled manner. It also allows problems to be spotted more easily. Claims that move through too quickly are more likely to have errors, while claims that move too slowly may have other issues. Slow claims may indicate that information is missing or that there is another part of the process that needs to be fixed. Overall, Kanban increases awareness of the claim process and encourages problems to be addressed and resolved before additional claims are filed.
Kanban works by pulling work based on demand, and its principles can help many businesses, from manufacturing to IT and healthcare. Another lean tool, like 5S, should be used with Kanban to support problem-solving and standardization.
For more information on Kanban and how it can help create a lean work process, check out Duralabel' Best Practice Guide to Kanban.
Related Resources
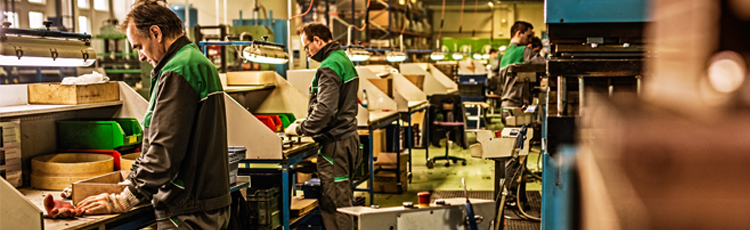
House of Lean: Building the Lean Manufacturing Framework
What Is the House of Lean? The House of Lean is a useful tool that can help you understand Lean Manufacturing ...
Read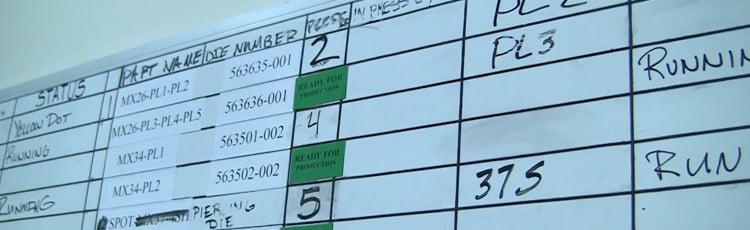
Heijunka Box for Lean Production Leveling
What Is a Heijunka Box and How Does It Support Lean Production? TheHeijunka boxis a scheduling tool used ...
Read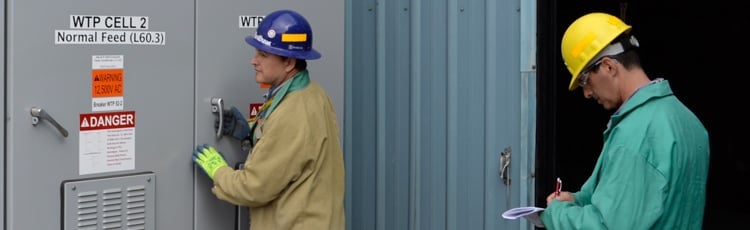
Gemba Walk: A Practical Approach to Lean Process Optimization
Gemba is one of the key principles of lean manufacturing and the Toyota Production System. Gemba is roughly ...
Read