Heijunka Box for Lean Production Leveling
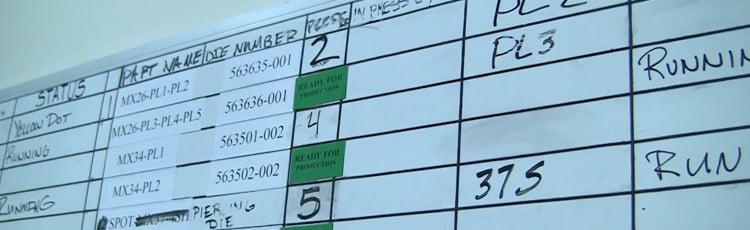
What Is a Heijunka Box and How Does It Support Lean Production?
The Heijunka box is a scheduling tool used for production leveling in Lean systems. It forms an important part of the Toyota Production System (TPS) and is critical when just-in-time principles are being used. By sequencing work visually, it helps reduce waste, improve delivery flow, and ensure flexibility. These Lean tools for workflow leveling support just-in-time operations and consistent output across teams.
Simply put, heijunka is the sequencing of orders in a repetitive pattern of production, aimed at smoothing day-to-day variations in total orders. A term perhaps not as widely known as kanban, kaizen, six sigma, or 5s, heijunka is nonetheless equally important because it contributes to inventory reduction and more efficient use of labor.
Heijunka Box Description
The heijunka box is essentially a wall-size scheduling tool. A common type of heijunka box is a grid of small boxes, or "pigeon holes," mounted on a wall. Each row of boxes represents a component or process, while each column represents a time period. The length of a time period might be an hour, several hours, a day, or even a week, based on the shortest amount of time that it takes to deliver one unit of whatever is being produced.
Colored kanban cards are placed in the pigeon holes in the heijunka box. Each kanban card represents the need for one unit of production. This provides a visual overview of the upcoming production runs.
The Heijunka Box, or leveling Box, is a physical device to level production volume and variety over a specified period of time. The load is leveled with consideration for the most efficient use of people and equipment. In a lean system this is the only place to input information on the production requirements for the day.
An Example of Heijunka
Let's take a simple example of three items needing to be produced: widgets, gizmos, and thingamabobs. A widget takes 30 minutes to produce, a gizmo only takes 15 minutes, and it takes 45 minutes to make a thingamabob. The columns in the heijunka box will represent fifteen minute increments, corresponding to the 15 minutes it takes to make a gizmo.
If four widgets need to be made, then four kanban cards are placed in one of the rows in the heijunka box, with an empty pigeon hole between each card. That is because it takes 30 minutes to make a widget, and that time span is represented by two pigeon holes in the heijunka box.
Let's say that widgets and gizmos are used to make thingamabobs and that it takes one widget and one gizmo to make each thingamabob. Let's also say that widgets and gizmos are made using the same machine. That means that the machine needs to be scheduled to make widgets at some times and gizmos at other times. Some facilities would produce a large batch of widgets, and then a large batch of gizmos ? but the production of thingamabobs can't be started at all until there is at least one gizmo ready to be used, halfway through the day. To avoid this delay, those facilities would have to maintain an inventory of components, defeating the purpose of lean manufacturing methods.
The heijunka approach is to balance the production of widgets and gizmos over the course of the work day, minimizing the need for an inventory of parts or delays in production. The plan for production would be shown by the heijunka box, which might be arranged like this:
7:00 | 7:15 | 7:30 | 7:45 | 8:00 | 8:15 | 8:30 | 8:45 | 9:00 | 9:15 | |
---|---|---|---|---|---|---|---|---|---|---|
Widgets | X | X | X | X | ||||||
Gizmos | X | X | X | |||||||
Thingamabobs | X | X | X |
Each letter "X" above represents a kanban card, which will be taken from the box at the marked time and delivered to the appropriate production area or machine. This movement of cards controls production so that the needed components are always available.
The Heijunka Box in Visual Management
The advantage of a heijunka box is in the way it displays production processes and the relationships between component and product production. This provides a means for visually managing the flow of production for evenness and flexibility. Eliminating dramatic fluctuations in production will make the entire process more predictable and manageable, as well as maintaining just-in-time delivery of needed materials, and minimizing inventories. Waiting time is eliminated and the potential for overproduction is reduced.
The overall objective of heijunka is to match production to customer demand, while at the same time using production resources in the most efficient manner possible. The result is a smooth and predictable flow of production. However, customer demand is not always smooth and predictable. Managing production through the heijunka box offers a system for immediately responding to changes in demand, but it requires a workforce that is versatile and capable of handling a number of tasks. The workforce, equipment, and transportation systems must be flexible enough to handle a number of production and delivery requirements.
Using Labels and Signs to Support Heijunka
When setting up a heijunka box, labels will be needed to identify the columns and rows. However, that labeling need is insignificant compared with the need for labels and signs to support heijunka. For example, the flexibility required by heijunka requires some workers to do a variety of tasks. Labels on machines, equipment, controls, and components help to ensure proper operation and eliminate confusion. For workers to be both efficient and effective in their work, needed information must be available regardless of the worker's physical location. This is best accomplished using visual communication provided by labels, signs, and tags, ensuring the information is already in place when a worker arrives and needs it.
Take Action Today
Want help implementing a Heijunka box? Explore the best option for making the labels, signs, and tags in the industry, with DuraLabel® Industrial Sign and Label Systems. With more than 50 types of supplies available and the best warranties in the industry, DuraLabel is the label printer brand major corporations around the world trust to get the job done right.
Or call us at 1-888-788-9936 to learn how DuraLabel supports workflow leveling techniques and Lean visual management systems that reduce waste and improve flow.
Related Resources
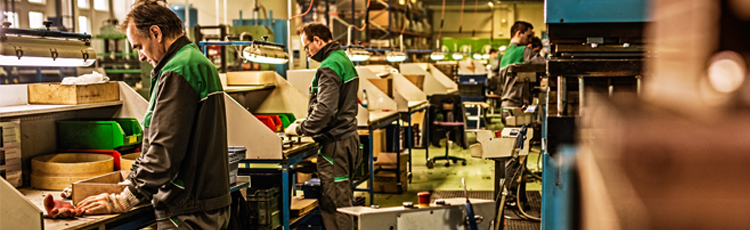
House of Lean: Building the Lean Manufacturing Framework
What Is the House of Lean? The House of Lean is a useful tool that can help you understand Lean Manufacturing ...
Read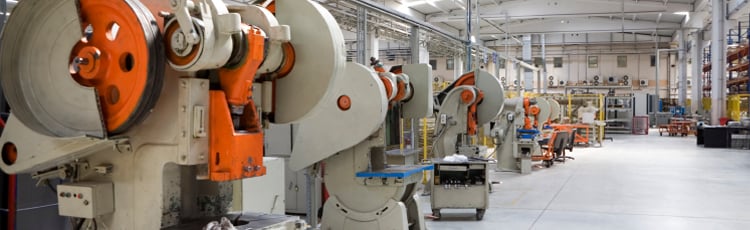
Lean Logistics Techniques
What Are Lean Logistics Techniques? Lean logistics techniqueshelp organizations streamline supply chain ...
Read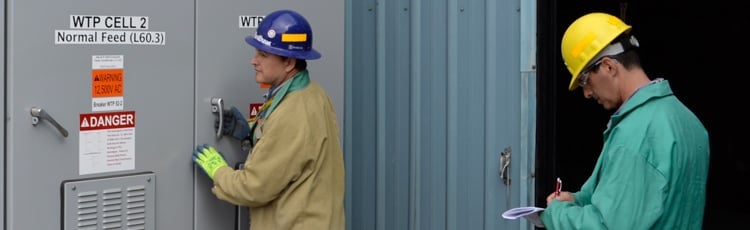
Gemba Walk: A Practical Approach to Lean Process Optimization
Gemba is one of the key principles of lean manufacturing and the Toyota Production System. Gemba is roughly ...
Read