Best Workplace Upgrades to Make Before Fall
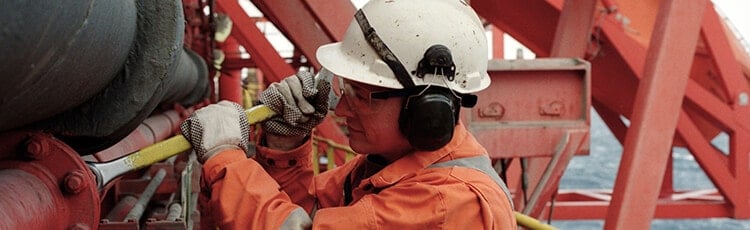
As summer winds down, leaves begin to fall gently from the trees and a coolness sets in, signaling seasonal changes are coming. Workplaces should take the time to prepare before the fall is in full swing; keeping ahead of known seasonal problems before they become a bigger one is part of a commitment to worker safety. Known as lean maintenance, it also establishes protections that keep facilities running efficiently, which in turn protects the company's bottom line.
Peak Performance
Will that old roof last another winter? A few machines are making a strange noise, but can they last through this next production cycle? Factories lose up to 20% of productivity because of downtime, and most downtime is underestimated, as it fails to consider losses in labor, product, startup costs, bottlenecks, and sales expectations, among other occurrences, according to the International Society of Automation.
Building a risk control strategy and consistently following it is ideal. How does your company create this strategy? Is there a way to improve it? Seasonal changes are important to keep in mind as policies, procedures, staffing, and other changes coincide.
What are some autumn safety topics workplaces can start working on? That depends on a facility's unique needs and geographic location. Additionally, there are some things that automated workplace monitoring might not pick up. Here are a few universal inspections and safety tips that can help workplaces prepare for fall/winter.
- Lighting: As daylight gets shorter, lighting needs may change. Replace bulbs and batteries.
- Chimney/furnace/HVAC: Check air filters and ensure these areas are clean and in good working condition.
- Roof inspection: Look for weathered and weak areas. Check doorways and other roof access areas for safety.
- Stairs: Improve railing, lighting, and step grips to avoid slips, trips, and falls.
- Ladders: Ensure the correct type of ladder is near locations where necessary for the work performed. Check ladders for safety and maintenance.
- Traffic areas: Ensure markings are in plain view for pedestrian and forklift traffic. Evaluate signs, labels, and floor markings for traffic inside and outdoors of the facility.
- Floors: Check for slippery areas, leaks, low lighting, cracks, and other flooring flaws that can cause an injury.
- Emergency exits and equipment: Make sure emergency equipment has been inspected and is ready for use. Label all emergency exits and equipment, including signs for instruction in an emergency, such as fire or earthquake.
- Sanitation and disinfection: As illness seasons arise, ensure sanitation equipment and disinfection stations are fully stocked. Label biohazardous waste and create signs that include the protocol for disposal.
Seasonal Safety Schedule
While these are just a few items to improve upon, make a thorough evaluation for safety and efficiency in consideration of the cooler weather to come.
Planning maintenance and repairs regularly help mitigate downtime. As the season moves along, take notes of what maintenance to plan or prepare for in the following season or year. Follow through on that checklist by creating clear visual communication.
Facilities can maximize the benefits of efficiency by reminding workers of what to do and when using cost-effective tools such as signs, labels, and floor marking. Reinforce safe and efficient behavior with routine training and safety education all year long.
Related Resources
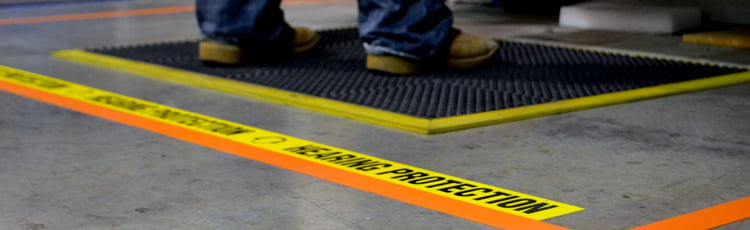
Spring Cleaning Safety Checklist: Floor Marking
When organizing and cleaning up work spaces this spring, consider changing up floor marking for safety, ...
Read
Five Essential Forklift Safety Tips
Forklifts play an essential role in warehouses, retail outlets, and other businesses throughout the United ...
Read
Industrial Wayfinding 101: Navigating the Terrain of Industrial Spaces
In the sprawling landscapes of industrial facilities, warehouses, and manufacturing plants, effective ...
Read