Cutting Corners on Machine Safety a Common Problem
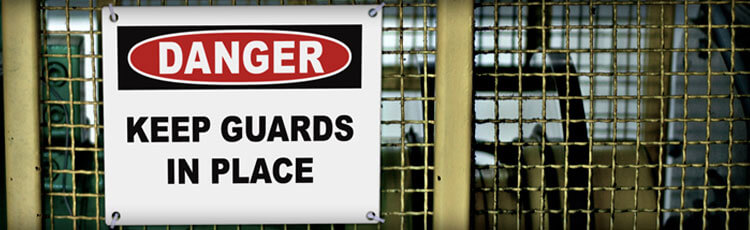
Powerful machines have stark hazards. Mechanical danger zones can bruise, slice, crush, maim, or even kill a worker. The last thing a workplace wants is to have a machine guarding mistake. Yet, machine guarding remains among the top 10 most common violations listed each year by the Occupational Safety and Health Administration. These days, there are several different types of machine guards. How is machine guarding changing to protect workers, and how are workplaces ensuring employees pay attention?
Costly Decisions
While it might be ideal to have new or refurbished tools and equipment, companies might forgo the option of purchasing them to replace a broken or missing machine guard. Stretching a few dollars or saving money on new tools is ideal. However, some managements take this concept too far; saving money and penny-pinching are not the same. Jury rigging equipment and cutting corners with machinery without regard for worker safety will cost more in the end.
Modifying or removing a machine guard is one of the most common causes of amputations and other injuries such as crushing, abrasions, and lacerations. It also causes more than 800 deaths per year, according to the Occupational Safety and Health Administration.
Why would a machine guard be removed? If the guard breaks, it is often removed and not replaced. Secondly, workers and management might think that removing the guard will make the machine work faster. It's safe to say: Safety tools and security are worth the expense.
Recently, a manufacturer in Florida was cited for removing guards during production. The result of a lack of machine guards: a worker suffered a partial hand amputation. "Management made a conscious decision to remove guards on three machines that exposed workers to dangerous metal shears," said OSHA Area Office Director Michelle Gonzalez in Jacksonville, Florida. "They put profits over their employees' safety and a young worker is permanently disabled."
OSHA also recently issued citations at workplaces where employees were allowed to work near unguarded equipment, which exposed them to struck-by and caught-in hazards. One worker lost fingers, another died. Why were the guards removed? The employer thought the machine would work faster, and OSHA deemed the acts "willful and serious."
Secure Safety Solutions
Machines move in rotation, back and forth, straight-line, and some newer ones have articulated motions (robots), which can be hard to predict. Often, when there are changes in workplace equipment and machinery, safety can be overlooked. Here are some common mistakes with machine guarding and how workplaces can reinforce machine guard safety.
- Damaged equipment: Promptly repair or replace essential safety measures for machines and equipment.
- Removed guards: If removing guards for maintenance, put them back once complete. Never remove guards to alter the performance of a worker or machine.
- New machines and equipment: Some machinery and equipment do not come with all the items necessary that help keep workers safe and meet OSHA compliance. Safety methods can vary and often take a dynamic approach.
- Use the correct materials: Make sure guards, fasteners, and other materials are the right type for the machine or equipment and made to withstand its force and application. Contact the machine manufacturer or use approved alternatives.
- PPE: While machine and equipment safeguards are in place, debris and other hazards are still present. Ensure workers have access to and use adequate personal protection equipment such as eyewear, hearing protection, gloves, and face shields.
Improving machine guarding and equipment safety requires vigilance and quick action. Managers can easily correct hazards and follow best practices by recognizing responsibilities and making robust and enforceable commitments to worker safety across the workplace.
Make machine and equipment evaluations routine. Report malfunctions, near misses, and other information using a job hazard analysis. Use the findings to prepare frequent toolbox talks and training. Address machine and equipment safety with workers by going over proper work etiquette, guards, maintenance, and what to do when there is a problem. Help workers maintain awareness of their surroundings through visual communication. Use machinery and equipment signs, compliant labels, and create safe distances around machinery hazards using floor marking. Not only will improving machine and equipment safety improve overall workplace safety, but it can also create a more efficient environment.
Related Resources
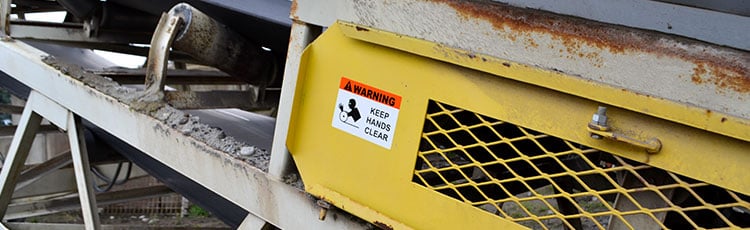
Guard Your Workers: 5 Easy Solutions for Machine Safety
Powerful machines are critical to industrial production, but they also pose severe hazards if not properly ...
Read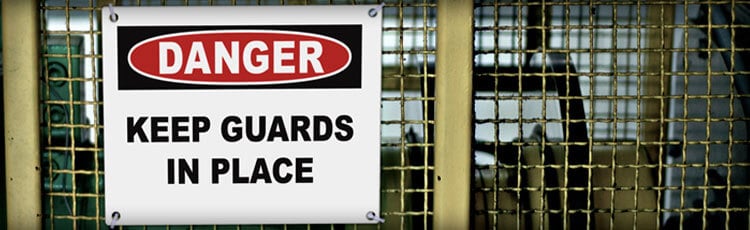
Worker Injuries Have Long-Lasting Effects
When a worker is injured on the job, the effects go beyond a simple report. Incidents can make tremendous ...
Read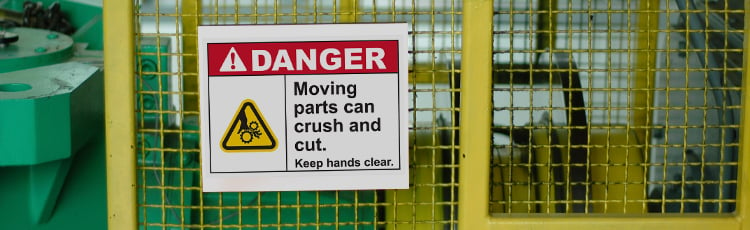
Avoiding OSHA Fines: Machine Guarding
OSHA produces an annual list of the Top 10 Most Frequently Cited Standards and year after year, machine ...
Read