Guard Your Workers: 5 Easy Solutions for Machine Safety
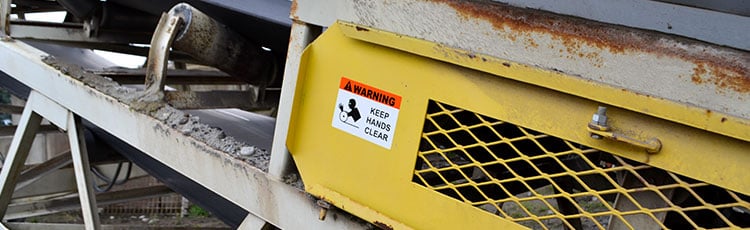
Powerful machines are critical to industrial production, but they also pose severe hazards if not properly guarded. The National Institute for Occupational Safety and Health (NIOSH) reported 738 machinery-related fatalities in 2022. This number reflects a 4.7% increase from the previous year.
The improper use or removal of machine guards remains one of the leading causes of serious injuries like abrasions, lacerations, and crushing. Yet, many facilities continue to operate with missing or damaged guards due to replacement costs or concerns about lost productivity. Some workers and managers even believe that removing guards can increase machine speed—a shortcut that leads to dangerous outcomes.
The Hidden Costs of Shortcuts
In an ideal world, all machines and equipment would be well-maintained, with every guard intact and functioning. The reality is that many facilities delay repairs or replacements, assuming that cutting corners will save money in the short term. Unfortunately, jury-rigging equipment often results in more expensive consequences, including Occupational Safety and Health Administration (OSHA) fines, reduced productivity from injuries, and even machine damage. Improper machine guarding consistently ranks among OSHA's top 10 most common citations.
Take the case of a manufacturer in Florida, where a decision to remove guards resulted in a worker's partial hand amputation. "Management made a conscious decision to remove guards on three machines that exposed workers to dangerous metal shears," said OSHA Area Office Director Michelle Gonzalez in Jacksonville, Florida. "They put profits over their employees' safety, and a young worker is permanently disabled."
5 Essential Tips for Machine Safety
Machines move in a variety of ways including articulated motions (robots) that can be hard to predict. When changes are made to machinery in the workforce, safety can be overlooked. Use these helpful tips to improve worker safety:
Take Time for Repairs
If something breaks—whether it’s a machine guard or an emergency stop button—it can be tempting to push repairs back to avoid slowing production. But that can be a costly mistake. Operating machines without their proper safety components makes accidents far more likely. The longer it goes unaddressed, the higher the risk.
Every facility should have a routine maintenance schedule for identifying and fixing issues quickly. Whether it's a small crack in a guard or a malfunctioning stop mechanism, prioritizing these repairs will keep your machines running safely and smoothly.
Install Proper Guards
Machine guards are designed to protect workers from serious injury by preventing contact with moving parts. In some places, guards are removed because they are thought to slow things down. This is a huge mistake. A machine without its guard can be dangerous—even deadly. Workers face serious risks when machine guards are missing or improperly installed.
Instead of bypassing the guard, make sure the correct one is installed for each machine. If it’s damaged or missing, fix it right away. Don’t let convenience get in the way of safety. Removing guards to speed things up may seem like a good idea in the short term, but the potential for injury—and the penalties that follow—aren't worth it.
Train for Safe Use
No machine safety system is complete without proper training. Workers need to understand the hazards each machine presents and how to operate it safely. This includes knowing when to stop using a machine, what to do in case of an emergency, and the importance of keeping guards in place. When workers know the risks and how to avoid them, they’re better equipped to stay safe on the job.
Training shouldn’t be a one-and-done deal. It should be ongoing. Every time there’s a change in equipment or a new hazard is introduced, workers should be retrained to stay informed. In many cases, injuries happen because someone wasn’t fully aware of how dangerous a machine could be. Make sure your team is ready to handle these risks.
Identify Hazards with Safety Labels
Not all machine hazards are obvious at first glance. Moving parts, pinch points, and areas with sharp edges are easy to overlook. That’s where visual cues come in. Safety labels and warning signs can draw attention to these danger zones to help workers stay cautious around machinery. Labeling areas that are particularly dangerous can also help your facility stay OSHA-compliant.
These visuals don’t just keep workers on alert; they reinforce safety procedures and serve as constant reminders about the risks around them. Even in the busiest environments, well-placed labels and signs make it easier to stay safe.
Equip Workers with PPE
Even with machine guards and safety training, personal protective equipment (PPE) is still an essential part of machine safety. Workers can be exposed to flying debris, loud noises, or sharp objects during machine operations. Goggles, gloves, and hearing protection are just a few examples of PPE that can prevent injuries when something goes wrong.
It’s not enough to provide PPE—workers need to use it consistently. Even a quick task can lead to accidents if proper protection isn’t worn. Make sure that workers have easy access to the PPE they need and are reminded of its importance.
Simplifying Safety with Visual Communication
Maintaining hazard awareness is key to machine safety. Use visual communication to reinforce safe practices:
- Warning Signs: Mark specific machine hazards and identify the necessary PPE.
- Safety Labels: Highlight danger zones and mark emergency shutdown controls.
- Floor Marking: Use floor tape and signs to define work zones and safe pathways.
By regularly evaluating machines and equipment, you can prevent accidents before they happen. Conduct routine machine inspections and document findings in job hazard analysis reports. These reports can highlight malfunctioning machines, near misses, and areas for improvement, helping you to create effective toolbox talks and safety training sessions.
Protect Your Workforce with DuraLabel
Keeping workers safe around machinery starts with clear, durable safety communication. DuraLabel helps ensure that machine hazards are easy to spot with high-quality signs and labels built for industrial environments. Whether it’s warning labels for pinch points or signage for emergency stop controls, DuraLabel products provide the visual communication tools necessary to protect your team and maintain compliance with OSHA’s machine safety standards.
The DuraLabel Kodiak Max Industrial Sign and Label Print System is an ideal solution for facilities needing long-lasting labels for machine safety. With its ability to create highly visible labels that resist wear and tear, Kodiak Max helps you clearly mark machine hazards, guarding requirements, and PPE zones. This durable system makes it simple to produce safety labels that stick, even in the toughest conditions to ensure your team stays informed and protected.
Want to ensure your facility is up-to-date on the latest compliance standards? Download the free Facility Signage Handbook to learn more about the which signs and labels your facility can benefit from.
For more information on how DuraLabel can improve machine safety in your facility, call us at 1-888-965-3359. Our experts are ready to help you find the right labeling solutions to keep your workforce safe.
Read Next:
Machine Guards and Amputation Hazards
Creating Compliant OSHA Signs: Tips and Best Practices
Related Resources
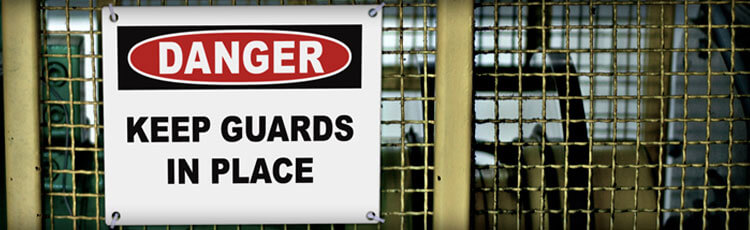
Cutting Corners on Machine Safety a Common Problem
Machine guarding violations are consistently among the OSHA top 10 violations. There are several common ...
Read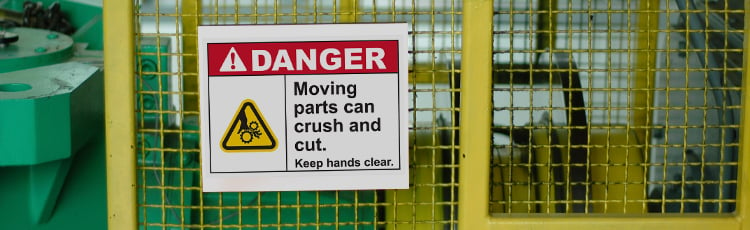
Avoiding OSHA Fines: Machine Guarding
OSHA produces an annual list of the Top 10 Most Frequently Cited Standards and year after year, machine ...
Read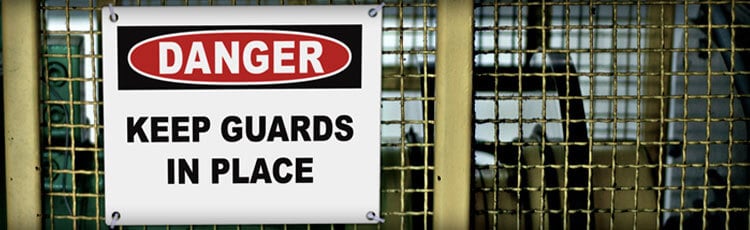
Machine Guards and Amputation Hazards
One of the first facets of workplace safety to be regulated by the Occupational Safety and Health ...
Read