Optimize Efficiency & Stay Safe: Visual Communication Signs & Labels

A primary mission for optimizing green energy efficiency in buildings through behavioral changes and facility upgrades is to reduce energy costs. However, there is a difference between wanting to improve energy efficiency in a facility and an employer who will do anything to save a dime. When done right, energy efficiency upgrades can not only save businesses money, but they can also ensure the health and safety of workers. Facility managers can look for ways to improve health and safety by employing safety best practice measures to reduce energy waste and amplify visual communication to help with hazard control.
Power Control Issues
Cutting energy costs is a brilliant way for facilities to save money. However, energy savings can be taken too far. "We had a lighting war in our facility with some people wanting lights on and others wanting lights off while working," said Sam Dobson, a floor worker at a packing facility in North Carolina. "We ended up getting a workplace occupational health and safety rep, and they did an assessment and made recommendations that the company implemented as policy."
Types of lighting, and too much or too little light in a facility can cause strain on workers' eyes and can cause discomfort such as burning or throbbing and headaches. Adequate facility lighting helps workers stay alert and perform tasks easier. Insufficient lighting can lead to an increase in error rates and, in turn, injuries. The Center for Disease Control (CDC) cites falling as one of the most common work-related accidents. Some common causes of workplace falls include:
- Reaching for something while on an unstable surface
- Tripping over loose carpeting, electrical cords, an open file drawer, or objects in walkways
- Improper or lack of ladder use
- Poor lighting/visibility
In some cases, inadequate lighting may be to blame for slips, trips, and falls. Without adequate lighting, it is difficult for a worker to see where they are going. Insufficient lighting can cause improper contrast for the eyes. Changes in the pavement, obstacles in the way, and even steps can be easily missed. Falls are the second leading cause of deaths worldwide with 37.3 million falls severe enough to require medical attention each year, according to the World Health Organization. In 2015, an Occupational Safety and Health Administration investigation found that forklift operators were exposed to a 20-foot fall and trip hazard while working in low-light conditions at a St. Louis warehouse.
"Allowing forklifts to be operated in low light conditions on open platforms that workers could easily drive off, is a recipe for disaster," said Bill McDonald, an OSHA director in St. Louis. "(The company) needs to immediately correct the many deficiencies in their facility. Each year hundreds of workers are injured on the job because employers fail to follow basic safety precautions."
Use Energy-Smart Safety
Using the power of visual communication, facility managers can add safety to energy reduction plans that save energy and operation expenses. For example, when cutting sight lighting, do so when a site is at its lowest occupancy. Keep perimeter site lighting on and all entrances lit. Make certain that lighting highlights all entrance and exit doors along with any egress pathways and emergency equipment (e.g. first aid stations.) Make accommodations in the building's lighting automation controllers to be able to shut off in areas that are least occupied. Lights can be dimmed or turned off in some areas as long as doing so is not impacting the ability of workers to do their work. Inadequate lighting can present a problem in stairwells, parking lots, front of buildings, and supply closets. Ensure safety in low-light areas by adding high-visibility floor tape to guide workers along pathways, highlight stations and doorways, and attract attention to uneven surfaces or open ledges.
Related Resources

5 Top Solar Energy System Strategies for Safety
Solar projects are in high demand and so is the solar installation and maintenance workforce. Here are five ...
Read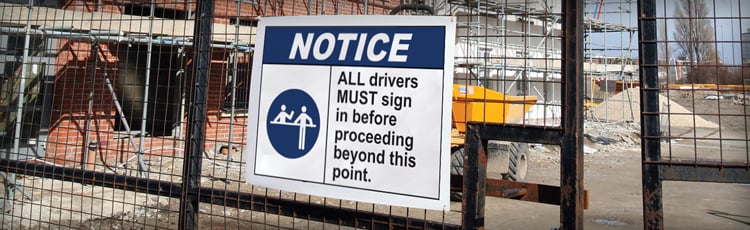
Signs Your Excavation Site Needs Shoring Up
Excavations of all types require a variety of tools and techniques for safety and efficiency. A few things ...
Read
Essential Electrical Labeling for Contractors and Facility Managers
In electrical work, precision is essential. Clear, durable labels enhance efficiency and organization in ...
Read