OSHA Announces Walking-Working Surfaces Rule
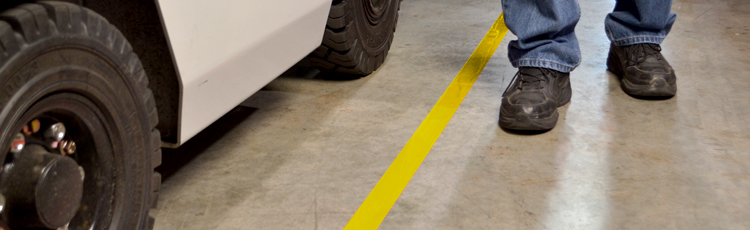
OSHA has been quiet from mid-January to mid-March 2017, which has not gone unnoticed by members of the safety trade media. Industry magazine ChemInfo conveyed that, "For years, the Occupational Safety and Health Administration has released a string of news releases every week detailing which companies are getting slapped with fines for what offenses. In a way, the press release feed read like a gossip rag for industrial safety wonks?But since Jan. 18? Not a peep."
Theories abound on the reason for the agency's silence, yet a thought remains; if we don't know what safety violations are happening in the world, how are we supposed to learn from others' mistakes? In other words, if you don't know the danger is there, how are you to avoid it?
OSHA's New Walking-Working Surfaces Rule
One regulation that OSHA did manage to push through in late 2016, days before the silent period began, is a new standard for walking-working surfaces. A walking-working surface is defined by the agency to be "any horizontal or vertical surface on or through which an employee walks, works, or gains access to a work area or workplace location."
OSHA's standard for walking-working surfaces, 29 CFR 1910.22, outlines requirements for ensuring that work surfaces are clean and properly maintained, and dry, when possible. This is important because following these rules can cut down on injuries, improve safety, and save employers money.
The walking-working final rule update went into effect January 2017. While the revised requirements upheld the basic rules, such as, "Employees must have a safe means of access to and from all walking-working surfaces," the updates provide greater clarity and direction for employers, including these easily-digestible updates:
- Requirements for guard rails and surface covers were shifted to other standards that correspond more closely with fall protection
- The standard no longer requires employers to mark "permanent aisles and pathways;" rather, that obligation was folded into 29 CFR 1910.22(c), which now requires employers to provide "a safe means of access and egress to and from walking-working surfaces."
- OSHA now requires regular inspections of walking-working surfaces, making the rule more consistent with the agency's construction standards
Great Visual Communication, Even During Quiet Times
Visual communication, such as safety signs and labels, can speak volumes, even when the foremost safety agency in the U.S. is a bit on the hushed side. Floor marking is an integral part of safe walking-working environments. For example, applying PathFinder Tread Tape to stairs, docks, kitchens, and other areas with slippery conditions can help stop slips, trips, and falls. Similarly, PathFinder Glow Tape offers safe egress paths during power outages, fires, and other low-light conditions with glow-in-the-dark floor marking. A variety of reflective tapes can increase visibility to call attention to hazards, electrical panels, edges, and more.
For a full explanation of floor marking standards and common applications, download a complimentary copy of Duralabel' Best Practice Guide to Floor Marking.
Related Resources

OSHA's Standard for Walking-Working Surfaces
Slips, trips, and falls can seem relatively minor in the grand scheme of things: Who among us, office workers ...
Read
Floor Signs
When employers imagine floor marking, most think of aisle markers, pathway designations, and hazard stripes. ...
Read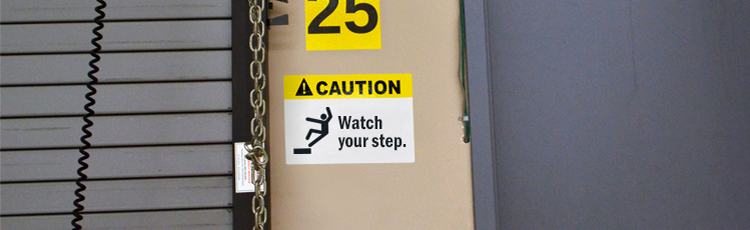
Workplace Injuries: The Common, the Costly
Some of the most common injuries cost employers more than $59 billion a year. We cover the top types of ...
Read